Pressure Sensitive Adhesives
Designed for end-use applications across tape, label, graphic and specialty film industrial markets, Bostik’s pressure sensitive adhesive portfolio of hot melt, waterborne, specialty solution acrylic and UV technologies is the most expansive in the adhesive industry.
Tailored Adhesive Formulations for Every Application
With a deep understanding of pressure sensitive adhesive chemistry, Bostik develops high-performance pressure sensitive adhesive formulations designed to enhance efficiency and durability. Whether it's removable pressure sensitive adhesive for temporary bonding or silicone pressure sensitive adhesive for high-temperature resistance, our products set the standard for reliability and versatility.
A Trusted Network of Suppliers
Bostik collaborates with leading pressure sensitive adhesive suppliers to ensure seamless access to top-tier adhesive solutions. Our pressure sensitive spray adhesive technology provides effortless application, while our range of pressure sensitive adhesives examples showcases the breadth of possibilities across construction, packaging, and automotive industries.
- UV Acrylic PSAs for Building and construction tapes, Vehicle graphics and mobility tapes
- Specialty Solution Acrylic PSAs for vinyl graphics, high-performance tapes and durable labels
- Waterborne Acrylic PSAs for indoor graphics, specialty tapes and protective films
- Hot Melt PSAs for linerless labels, temporary films and mobility tapes
- Moisture-Cure PSAs for mobility tapes, building & construction tapes and durable lables
Pressure Sensitive Adhesive Definition: Understanding the Basics
A pressure sensitive adhesive (PSA) is a type of adhesive that forms a bond when pressure is applied, without requiring heat, water, or solvents. Its unique formulation allows for instant adhesion to various surfaces, making it ideal for applications in packaging, labels, tapes, and medical use. Bostik continuously innovates PSA technology to deliver enhanced durability and performance.
How Our Pressure Sensitive Adhesives Help You
Ideal for tape, label and specialty film applications, our hot melt pressure sensitive adhesives possess:
- Low VOC formulations to improve worker safety
- Compatibility with bio-based raw materials to increase sustainability
- Exceptional tack capabilities and ability adjust tack levels for different application needs to enhance performance
- Fast setup times to streamline automated assembly processes
- Ability to adhere to difficult substrates even in cold and humid conditions to extend durability
Specifically, our hot melt pressure sensitive adhesives include the following product family:
- Thermogrip®
How Our Waterborne Pressure Sensitive Adhesives Help You
Commonly used for packaging, tape, label and graphic applications where both permanent and removable bonds are required, our waterborne pressure sensitive adhesives offer:
- Low temperature application to ensure good performance regardless of environmental conditions
- Broad chemical flexibility to meet wide variety of application needs (such as high and low adhesion, general purpose, all-temperature, removable and wash-off)
- Good mechanical stability and cohesive strength to improve bond performance
- Excellent clarity and clean removability to enhance aesthetics
- High speed coating to increase plant efficiencies
Specifically, our waterborne pressure sensitive adhesives include the following product families:
- Aroset®
- Flexcryl®
- Encor®
KEY APPLICATIONS
- Indoor graphics
- Specialty tapes
- Protective films
How Our Specialty Solution Acrylic Pressure Sensitive Adhesives Help You
Used in high-performance applications, such as specialty tapes, durable labels, graphics, medical and films, our specialty solution acrylic adhesives provide:
- Superior durability, strength and multi-substrate adhesion in challenging conditions to improve end-use performance
- Weather, chemical, moisture and UV resistance to extend longevity
- Ability to bond across substrate types to increase design options
- Premium shear and peel adhesion to wide substrate variety to enhance durability
Specifically, our specialty solution acrylic adhesives include the following product family:
- Aroset®
KEY APPLICATIONS
- Vinyl graphic
- High-performance tapes
- Durable labels
How Our UV Pressure Sensitive Adhesives Help You
Ideal for high-performance applications, such as specialty tapes, durable labels, graphics, medical and films, our UV pressure sensitive adhesives provide:
- Fast cure speeds even with thick coat weights to optimize plant efficiencies
- 100% solids to eliminate handling of solvents
- Low energy consumption to reduce carbon footprint
- High temp performance to increase end-use application longevity
Specifically, our UV pressure sensitive adhesives include the following product family:
- Arocure®
KEY APPLICATIONS
- Building and construction tapes
- Vehicle graphics
- Mobility tapes
How Our Hot Melt Pressure Sensitive Adhesives Help You
Overall, our hot melt PSAs offer:
• Ability to adhere to diffi cult substrates even in cold and humid conditions to extend durability
• Low VOC formulations to improve environment
• Compatibility with bio-based raw materials to increase sustainability
• Exceptional tack capabilities and ability adjust tack levels for diff erent application needs to enhance performance
• Fast setup times to streamline automated assembly processe
KEY APPLICATIONS
- Linerless labels
- Temporary films
- Mobility tapes
How Our Moisture Cure Pressure Sensitive Adhesives Help You
Our moisture-cure PSAs possess:
• Ability to achieve high coat weights in one pass to increase operational efficiencies
• Balanced tack and peel as well as high adhesion to LSE substrates to heighten end-use versatility
• Low odor to improve worker safety
• High temperature and chemical resistance to enhance durability
• Additional capabilities, such as sound dampening, to extend application use
KEY APPLICATIONS
- Mobility tapes
- Building and construction tapes
- Durable labels
Why Choose Bostik for Your PSA Needs
An Arkema company, Bostik offers the broadest range of PSA technologies available on the market from a given supplier. Vertically integrated for supply security, we deliver the products you need when and where you want them. These products are designed for a range of ready-to-coat applications, though we also have the ability to custom formulate solutions to meet specific requirements. Additionally, our technical expertise and in-house capabilities enable us to help with testing and trialing processes to reduce your downtime and get you the right solution quickly. Further, because sustainability is at the forefront of all that we do, we also help reduce overall environmental impact and make it easier for you to meet sustainability initiatives, too.
Ready to get started with a hot melt, waterborne, specialty solution acrylic or UV pressure sensitive adhesive?
Contact an expert
Exploring the Spectrum of Pressure-Sensitive Adhesives: UV Acylic, Waterborne, Specialty Solutions Acrylic, Hot Melt and Moisture cure
How Each Technology Improves Sustainability
Our PSA technologies are formulated to be safer solutions than competitive options,
possessing sustainable attributes that enable a reduced carbon footprint across the value
chain to aid in the circular economy and preserve resources
UV ACRYLICS
- 100% solids formulation
- Smaller plant footprint than other options
- Long-term durability
Waterborne Acrylic PSAs
Eco-conscious and versatile, waterborne PSAs are formulated using polyacrylic emulsions or natural polymers. Their advantages include:
- Low VOC emissions and compliance with environmental regulations.
- Excellent adhesion to paper, cardboard, and some plastics.
- Cost-effectiveness for high-volume applications like labels, tapes, and packaging
Specialty Solution Acrylic
• High solids content
• Safer solvent packages than alternatives
• Extended product lifespans
HOT MELT PSAs
• 100% solids formulation
• Decreased energy usage during application
• Low VOCs
Moisture Cure PSAs
• 100% solids formulation
• Increased performance capabilities
• Reduced waste
Frequently Asked Questions about Pressure Sensitive Adhesives (PSA)
PSA stands for Pressure-Sensitive Adhesive, a type of adhesive that forms a bond when pressure is applied, without needing heat, water, or solvents. It's commonly used in tapes, labels, stickers, and glue dots1. The strength of the bond depends on the amount of pressure applied and the surface characteristics.
PSAs are designed to work at room temperature but can lose tackiness in extreme temperatures. They are different from structural adhesives, which require curing processes like evaporation or chemical reactions1.
PSAs are formulated with plasticizers, which enable a workable viscosity for coating and help maximize wet out for bonding. Plasticizers are oils so over time, they can bleed into paper and cause a stained appearance. Bostik has patented PSA technology that can provide stain resistance on paper face stocks.
PSAs will degrade with extended time at elevated temperatures when the line is not running. Degradation can negatively affect the appearance, processability, and performance of an PSA. To prevent producing PSA labels or tapes out of specification, it's important to control the temperature of the melt tank, hose, and coating head during equipment-related downtime.
Linerless labels allow you to reduce waste. They are similar to tapes in that silicone is coated on the surface of face stock, eliminating the need for a separate release liner. Along with reducing waste, linerless labels offer operational and inventory efficiencies. Linerless labels with Bostik hot melt adhesives can be used in e-commerce, grocery weigh scale, and quick service restaurant applications.
- Adhesion Mechanism – PSAs remain tacky at room temperature and bond instantly when pressed onto a surface.
- Viscoelastic Properties – They balance flow and resistance, allowing them to conform to surfaces while maintaining strength.
- Molecular Interactions – Van der Waals forces contribute to bond strength, ensuring durability.
- Temperature Sensitivity – PSAs may lose tack at low temperatures or reduce shear strength at high temperatures.
Pressure-Sensitive Adhesive (PSA)
- Sticks with light pressure: No need for heat, water, or solvents—just press it on.
- Tacky to the touch: Always slightly sticky, allowing for repositioning (in some cases).
- Removable or permanent: Available in both kinds depending on application.
- Common uses: Packaging tape, stickers, medical bandages.
Pressure-sensitive adhesives (PSAs) are fascinating little marvels of chemistry! They’re made from a blend of materials that give them their signature stickiness without needing heat, water, or solvents.
Slot die is the most common type of coating method used with PSAs. Typically hot melts are transfer coated from the release liner to the face stock to achieve the smoothest surface on the adhesive for bonding. Roll coating or gravure printing may be used to pattern coat hot melts.
Bostik Pressure Sensitive Adhesive Products
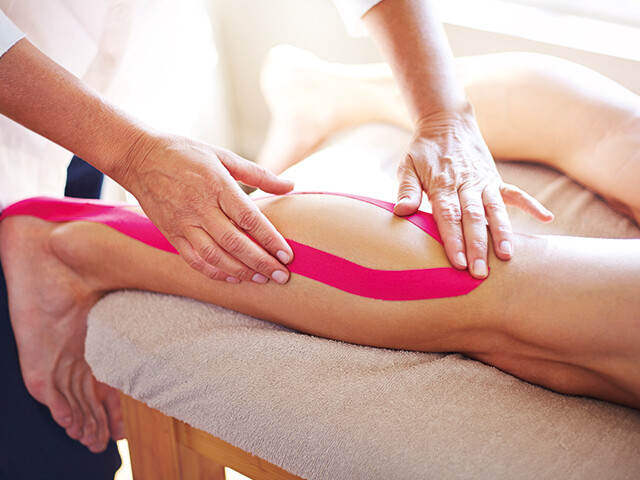
HM 2110
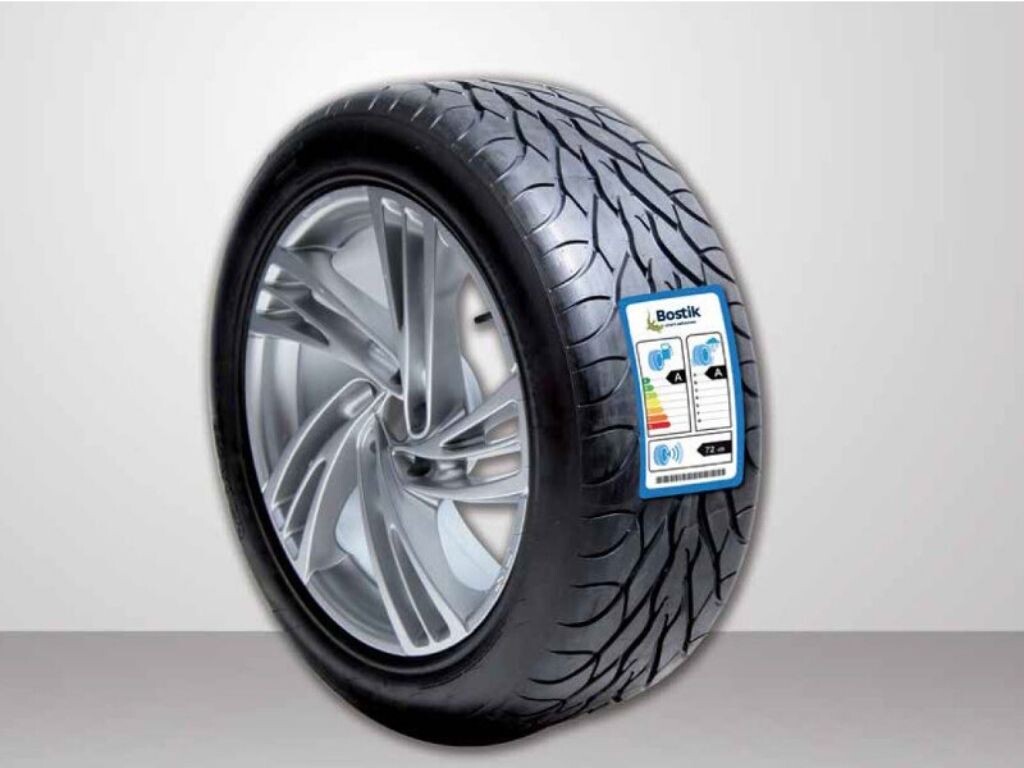
TLH 2549 E
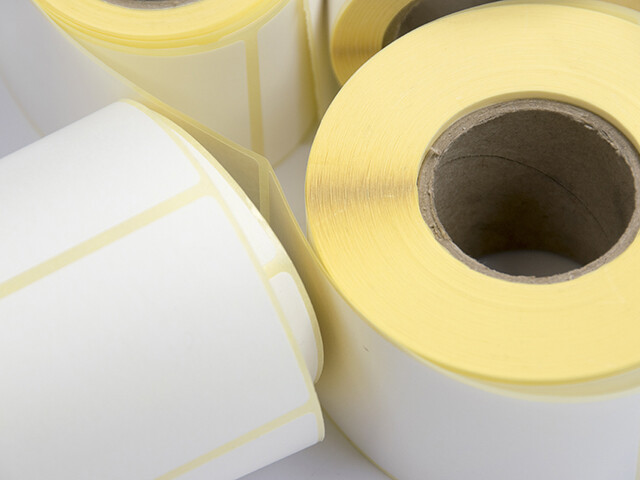
TLH 4272E
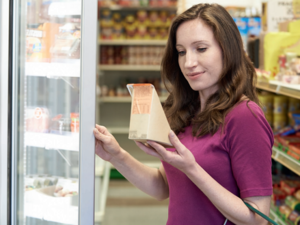
TLH 9100E
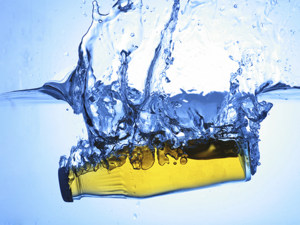