Jun 17, 2018 - 10 min
SELECTING THE RIGHT SKIN TO CORE ADHESIVE FOR SANDWICH PANEL BONDING
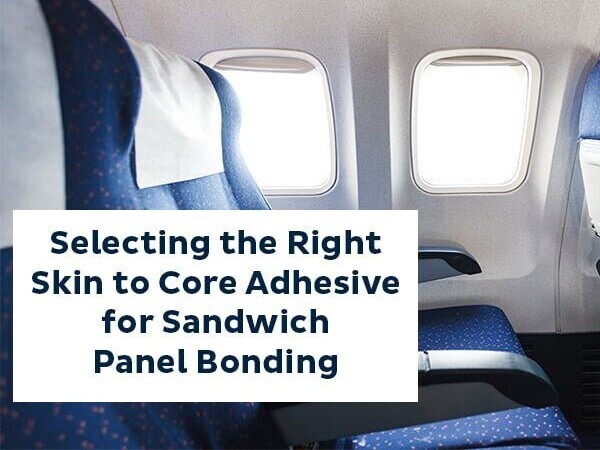
As cited in Composites World, sandwich panels are the largest composite application for aircraft interiors. These composites, comprised of a skin and core material, can be bonded together with an adhesive, and are used in aircraft flooring, ceilings, galley walls, lavatories and cargo hold liners.
Selecting the right materials for these structures is critical. Failure to do so can result in poor performance, higher cost, unnecessary weight or over-engineering. Additionally, it’s important that the finished product meets all aircraft interior application regulations, which can make selection even more complicated.
In addition to understanding the end-use application requirements, consider the following items in order to select the right skin to core adhesive for sandwich panel bonding:
1. Strength of the Bond Line to the Skin
The first consideration to make when selecting an adhesive chemistry for sandwich panel bonding is the strength of the bond line to the skin.
High strength application requirements can quickly eliminate most thermoplastic adhesive options, which narrows the selection process. Oftentimes structural applications require the use of a strength thermoset adhesive that will exhibit failure modes within the core material rather than adhesive or cohesive failure.
Adversely, if high strength is not required, yet a high strength material is selected, this could be detrimental to the other requirements. By using an adhesive with a high modulus, unnecessary rigidity can be imparted onto the part. Also, typical high strength adhesives, such as epoxies, require curing parameters that may not allow for the use of the lowest-cost cores or skin materials.
As a result, it’s important to determine the strength requirements prior to bonding materials together.
2. Processing Parameters
Once the strength requirements are determined, it’s important to look at the processing specifications of the materials selected. Using an adhesive chemistry that fits into the processing parameters of the other materials will help ensure uniform and repeatable parts.
For example, some low Tg polymer foam core materials cannot be processed at the high temperatures often required for curing epoxy systems. Many skin mat drills have a higher Tg than the cores that are often chosen. A thermoplastic adhesive can be tailored to have a Tg that closely matches with the skin and cores chosen.
3. Flame Resistance Requirements
When selecting a skin to core adhesive, take a look at the flammability requirements of the application. Aircraft interior applications require compliance to FAR 25.853; however, flame, smoke, toxicity and OSU testing may not always be applicable for every end-use application.
For example, private and business jet requirements vary from those of commercial aircraft. Another factor to consider is the flammability of the skin. For example, if a PEI skin is used on the outer layer of the sandwich panel, flame resistance of the adhesive selected may become less critical. This is due to the PEI skin’s high heat resistance.
However, if a less heat resistant skin is chosen, then the selection of a flame retardant adhesive that is OSU compliant becomes more vital.
4. Puncture Resistance Requirements
End-use applications have different puncture resistance requirements. For instance, an adhesive’s puncture resistance is very important for sandwich panels used in flooring applications. However, it is less critical for ceiling panel applications.
5. Forms
After the adhesive chemistry is chosen, the adhesive’s form must be considered. The form can often assist with processing efficiency.
For example, a film adhesive is easier and quicker to process than a liquid resin system, which requires more time to be pumped and wet out.
6. Quantity and Thickness
It’s important to use the right amount of adhesive when bonding sandwich panels. Too much adhesive can weaken the bond line by allowing the bulk adhesive properties to dictate the failure point of the sandwich panel. This can often be identified as cohesive failure in the testing of the panel.
Likewise, too little adhesive can also cause issues such as adhesive failure from the honeycomb or foam during adhesion testing.
Adhesive thickness is important to the flammability of the system. Thick bond lines can become softened during flammability testing and cause system failure. Additionally, thick bond lines add organic material to the overall system fuel which need to be counterbalanced with additional flame retardants.
For more information on adhesive for sandwich panels, visit www.bostik.com.