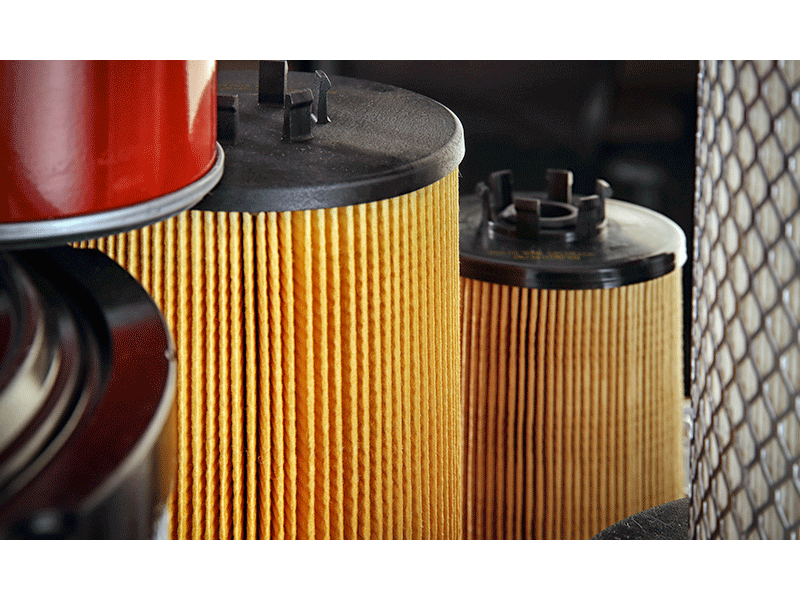
When assembling a filter, it’s important to keep in mind factors that impact its end-use performance levels. One factor in particular is the filter’s pressure drop. Take a look at how pressure drop impacts filter performance and how using the right adhesives during assembly can help minimize it. What is Pressure Drop? Pressure drop describes a change in pressure from point A (high pressure) to point B (low pressure). With filters, the higher the drop, the greater the impact on performance. For example, if pressure continues to build up when a substrate is trying to get through a filter, it indicates too much resistance to flow. In other words, the filter is clogged, causing a significant pressure drop when going from point A to point B. This wastes energy in addition to impacting the filter’s performance.
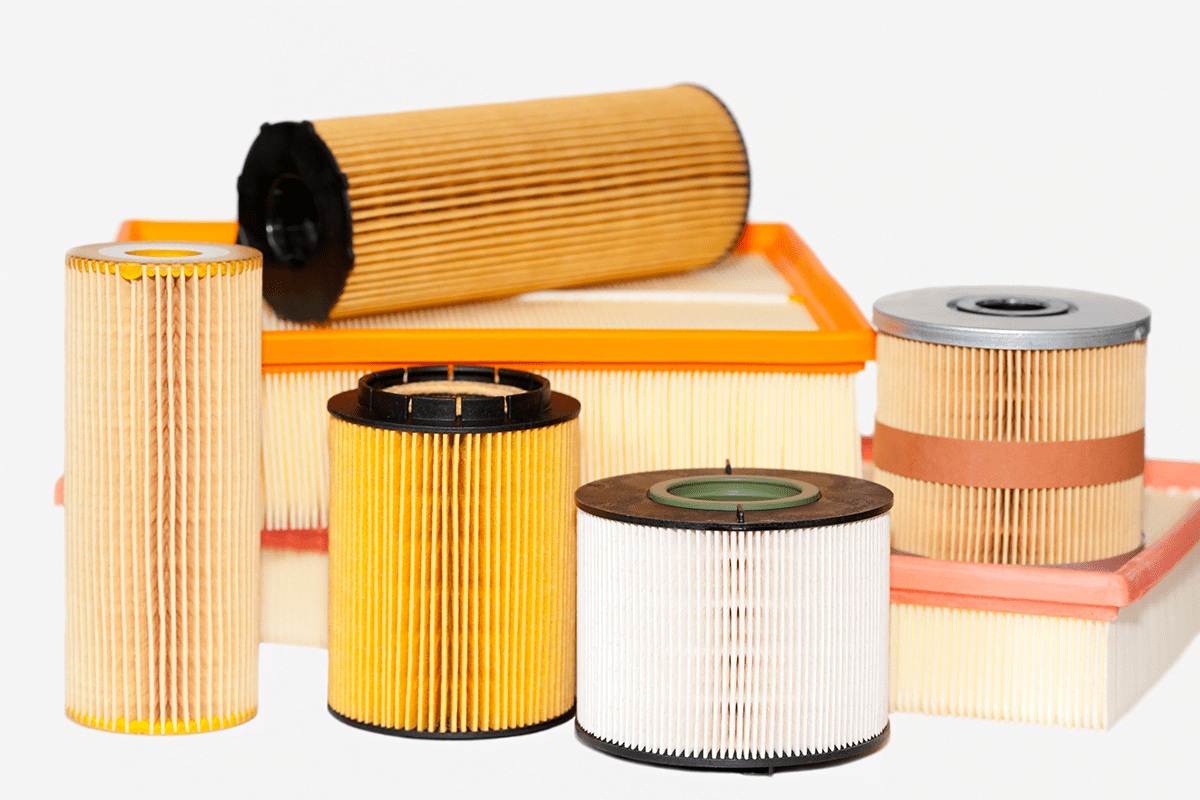
How Do Adhesives Minimize Pressure Drop? Adhesives play an important role in filter media manufacturing. For example, they’re used in assembly filter pleats, molded end caps and wound filter elements. Web adhesives in particular are a smart choice when looking to minimize pressure drop. They're laminated onto the filter media using heat. These adhesives are porous, which enables them to create a breathable layer in the filter media. They also can easily form to the filter’s contours in a discontinuous, nonwoven sheet. Other adhesives may be too thick, causing the filter to clog and increase the amount of pressure drop. Spray/melt blown adhesives are another smart option when looking to aid in filtration efficiency. Like web adhesives, these solutions form porous, breathable bonds in a discontinuous pattern. However, with these adhesives, manufacturers must first take the adhesive resin and spray/melt blow it directly onto the media with proper equipment. In addition to minimizing a filter’s pressure drop, web and spray/melt blown adhesives decrease adhesive use in the assembly process. This helps companies in the following ways:
- Lower costs
- Reduce material waste
- Low viscosity
- Sufficient heat resistance