Aug 12, 2024 - 3-5
How to Improve Your Case and Carton Sealing Line Efficiencies
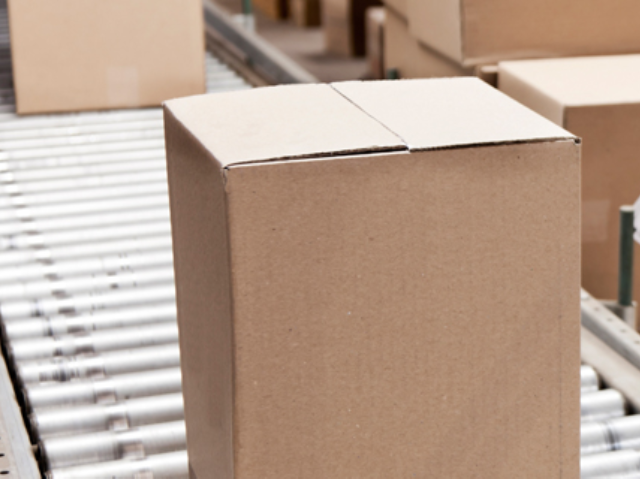
Improving case and carton seal production line efficiency can be a challenge for many plant managers and operators. Bostik’s experts have compiled a list of four key areas to consider before making an adhesive choice.
Packaging operations that are fast ... efficient … trouble-free ... these are common goals for high-volume production line managers. Automated systems for end-of-line hot-melt adhesive application are one popular solution. But, the wrong choice of glue can have unpleasant consequences for productivity.
To help you keep your packaging equipment running smoothly, Bostik’s experts have compiled a short list of watch-outs and attributes to look for when choosing your adhesive for case and carton sealing.
4 Key Needs for Efficient Hot Melt Application
1. Inadequate Adhesion Causes Pop-Opens
Reduce your line downtime by choosing a hot melt that offers specific adhesion to your packaging materials. This is especially relevant for difficult-to bond-substrates such as highly recycled cardboard boxes.
2. Slow Set Times Reduce Line Speed
Adhesives that can’t keep up with your fast-moving line can have two negative results. They don’t bond in the allotted time, or they force you to slow down production. Neither is good for business.
3. Charring Increases Your Downtime
Inadequate adhesive quality can lead to increased maintenance in multiple ways. Those that char easily can cause clogging and require additional nozzle maintenance. Hot melts that do not apply cleanly can lead to increased time for cleanup.
4. The Need to Juggle Multiple SKUs
Some adhesives target fewer types of packaging substrate. This can necessitate stocking and ordering multiple hot melts, sometimes from different suppliers. This creates more complexity in your supply chain and on the line. It can also magnify the chance of errors in matching substrate to adhesive. Either may decrease bonding effectiveness and, in the end, consumer satisfaction.
The Benefits of Kizen® for Your Production Line
To avoid these issues, we recommend choosing a hot-melt bonding solution that avoids all four of these key pitfalls. That’s why our experts have created the Kizen® line of adhesives. Bostik’s proprietary high-performance hot-melt adhesive technology delivers comfort, environmental advantages, and operational efficiencies. With Kizen, rest assured that you can:
Reduce Pop-Opens
Kizen decreases the likelihood of pop-opens, which reduces the risk of unplanned downtime. Production line operations remain on target and cost-effective.
Increase Line Speeds
With quick set time ideal for auto-feed systems, Kizen enables production lines to run faster. This enables plants to meet higher output demands.
Decrease Maintenance
Kizen limits adhesive residue on equipment and is formulated to reduce char. As a result, you’ll need less downtime for case and carton sealing equipment maintenance.
Reduce SKUs
Offering a wide processing window, Kizen is able to bond packages across case and carton sealing production lines. This helps plants consolidate SKUs, further streamlining processes on and off the production floor.
The Many Uses of Kizen for End-of-Line Packaging
In addition to case and carton sealing, Kizen adhesives are ideally suited to a wide range of packaging industry needs, such as:
- Palletizing
- Spot packaging
- Freezer-grade goods
- Ecommerce packaging
Kizen is designed for the packaging of medical, food, beverage, personal care, and pharmaceutical products, as well as absorbent hygiene product manufacturing. Ask how can Kizen boost the efficiency of your case and carton packaging line today.
See also
Back to all articles- Disposable Hygiene
- Disposable Hygiene
- Disposable Hygiene