Jun 18, 2024 - 3-5 minutes
What to Consider with a Compostable Hot Melt Adhesive
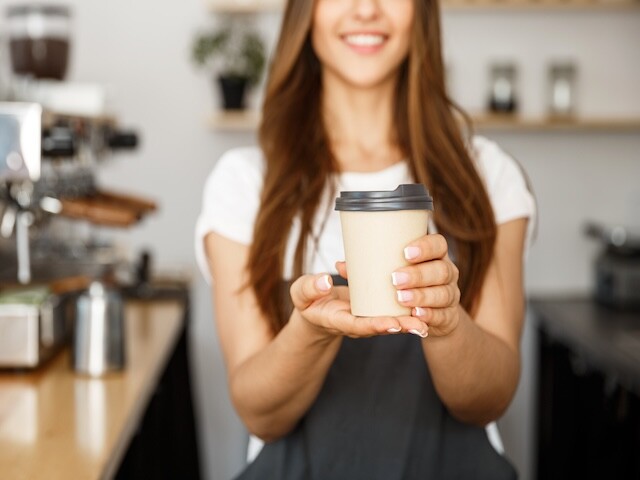
Learn how to integrate compostable hot melt adhesives into your to-go cup and packaging production lines, helping you to enhance sustainability and reduce environmental impact.
As a package manufacturer, you likely want to reduce your packaging’s environmental impact and are considering compostable packaging to do so. However, it may seem like a challenging task to handle compostable packaging materials, especially a compostable hot melt adhesive. You may think it will require significant investment to implement the adhesive and achieve proper performance levels.
This is not the case.
By understanding the compostable adhesive’s formulation, it can be easy to properly handle it, enabling you to manufacture 100% compostable packaging. Find out what you need to consider for it to be a reality.
Understanding Compostable Hot Melt Adhesives in General
Compostable adhesives are designed to degrade in composting conditions with other compostable materials, leaving no residue behind nor producing any harmful emissions during decomposition. To be deemed compostable, all materials must meet the Biodegradable Products Institute (BPI)’s testing certification.
Compostable adhesives’ formulation allows them to work well in packaging applications for the following reasons:
- Compatibility with other biodegradable materials: Compostable adhesives have a chemical affinity for commonly-used packaging substrates such as paper and corrugate. This allows them to form a sufficient bond without negatively impacting substrate quality or end-use package performance.
- Ability to meet necessary performance criteria: Compostable adhesives also provide lasting bond strength throughout temperature and moisture fluctuations. This helps packages maintain their integrity during transportation, storage and use.
How to Handle Compostable Hot Melt Adhesives
Compostable adhesives can form strong bonds to many of the same materials as traditional adhesives; however, because they are designed to decompose at the end of their life, certain production elements need to be optimized to mitigate decomposition likelihood during the manufacturing process itself.
Pot Life
Prolonged exposure to increased temperatures can cause all adhesive polymer types to break down and lose their bond strength. Because compostable adhesives are designed to decompose when exposed to heat, they are more sensitive to heat exposure than traditional adhesives. Therefore, you need to ensure they are not subjected to heat for extensive periods of time during manufacturing, as you don’t want the polymers to degrade prematurely. Assessing the adhesive’s pot life plays an important role in this, because it can help you discern how long the adhesive can remain melted and viable before degrading.
Typically, a pot life of 30 minutes or less is recommended for compostable adhesives. However, you should be sure to consider your specific adhesive usage rate compared to your melt tank size. Your equipment supplier can help ensure your equipment is right-sized and compatible with compostable adhesives. You want the ratio between the two to be optimized so that adhesive is not sitting stagnant in the tank unused. With compostable adhesives, it’s recommended to use a small melt tank or a melt-on-demand system. A melt-on-demand system is an automatic process that detects when adhesive is in the tank and melts only what is needed for a given application. These methods are to reduce the amount of adhesive in the tank at a given time and how long it’s exposed to heat at a particular temperature.
Adhesive Pot Life Pro Tips
Many manufacturers believe that the act of turning melt tanks on and off contributes to degradation likelihood across all adhesive types. This is because they think exposure to rising temperature is what triggers polymer break down. However, this is not the case. Instead, exposure to sustained high temperatures causes degradation. Temperature is essentially a measurement of how fast molecules are moving. When temperatures are high, the molecules move quickly, and chemical reactions, such as degradation, can occur rapidly. You want to be careful about over-exposure to sustained heat with any type of adhesive but especially compostable adhesives, given that they are more sensitive to heat by nature.
To avoid inadvertently going beyond your adhesive’s recommended pot life, conduct a qualification test that confirms the adhesive is not degrading on the production line. To do this, consider stopping the line for given periods of time and checking the adhesive to assess the ideal production window for your application needs. It’s recommended to do this test in addition to typical qualification tests that occur with conventional adhesives, such as ensuring they can meet end-use application performance requirements.
Viscosity
When considering your compostable adhesives’ needed pot life, it’s also important to know that it impacts viscosity. Viscosity is the adhesive’s resistance to flow, which influences its surface wet out capabilities, cure speeds and ultimate bond strength. Therefore, you want to have an optimized viscosity level so that production processes and performance needs are met. When an adhesive is heated during its pot life, the viscosity level naturally decreases. You can discern the viscosity decrease by assessing the adhesive pressure level. A higher viscosity adhesive will require more pressure to pump through at the same rate as a lower viscosity adhesive. Therefore, if the pressure goes down at a constant flow rate, you can deduce that the viscosity is decreasing, too.
The decrease in viscosity applies to traditional adhesives in addition to compostable adhesives. However, because compostable adhesives are more susceptible to heat to begin with, they are formulated with a higher viscosity to start. In addition to increasing polymer strength, it allows their viscosity to be able to naturally decrease slightly without losing bond capabilities.
Adhesive Viscosity Pro Tips
To help achieve desired viscosity, consider:
- Adjusting the adhesive temperature via quality control tests until you achieve a balance between viscosity and pot life: You want a viscosity level and pot life window that allow you to run the adhesive consistently without issue. Keep in mind that as the temperature goes down, the pot life increases. However, the viscosity rises as well during this time. If the viscosity gets too high, it can be difficult to pressure through the equipment.
- Sizing the adhesive tank to match the consumption rate within the adhesive’s pot life: You want to ensure you’re able to use all the adhesive in the tank before the viscosity level becomes too low and increases degradation likelihood. Right-sizing your equipment can help reduce this.
- Reassessing line speeds: Because compostable adhesives have a higher viscosity to accommodate heat exposure, it can cause increased pressure in seals and valves that push the adhesive out. To not overexert your equipment parts, you may want to reassess line speeds.
To that end, if the adhesive pressure changes dramatically and is outside the normal range, then it can be an indication that an element of the process has changed and needs to be troubleshooted.
How to Implement Compostable Hot Melt Adhesives
By optimizing your production for your adhesive’s pot life and viscosity levels, you can easily incorporate compostable hot melt adhesives into your production lines. While they are more susceptible to heat and require finding the right processing window, they otherwise function very similarly to traditional hot melts. Additionally, incorporating them into your production lines allows you to manufacture 100% compostable packaging, addressing brand owner and consumer demand for more sustainable packaging.
To get started, consider working with a Bostik expert. Bostik, adhesive solutions by Arkema, manufactures the market’s first BPI-certified compostable hot melt adhesive, Kizen® LEAP 1.0. Designed to enable 100% compostable packaging, Kizen LEAP 1.0 also matches performance expectations for conventional adhesives and works well for to-go packaging.
Additionally, this compostable adhesive can run on existing equipment; no equipment investment is needed, and startup downtime can be kept to a minimum.
Bostik also will work directly with you to establish the right processing window for your application needs. In particular, we offer line assessments to optimize existing processes, conduct any troubleshooting and determine the right adhesive for your production needs. We can also assist with development, qualification and rollout trials to help streamline and reduce complexities. Further, our experts offer pilot coating on certain substrates and have an in-house analytical lab to conduct additional testing.
As an Arkema company, we also put sustainability at the forefront of our efforts to develop products that contribute to a more sustainable world. This includes the market’s first compostable cold seal, Turbo-Seal® LOOP 1.0, as well as the market’s first APR-approved, all-temperature wash-off label adhesive, Flexcryl™ Clearcycle 1000. Contact a Bostik expert today to learn more about our solutions and how they help you reduce your environmental impact.
©2024 Bostik, Inc. All Rights Reserved
All information contained herein is believed to be accurate as of the date of publication, is provided “as-is” and is subject to change without notice. To review our full U.S. Legal Disclaimer, visit: https://bostik.com/us/en_US/privacy-policy/legal-disclaimer