Jul 28, 2023 - 3-5 minutes
How the Right Cold Seal Adhesive Supplier Gives You a Competitive Advantage
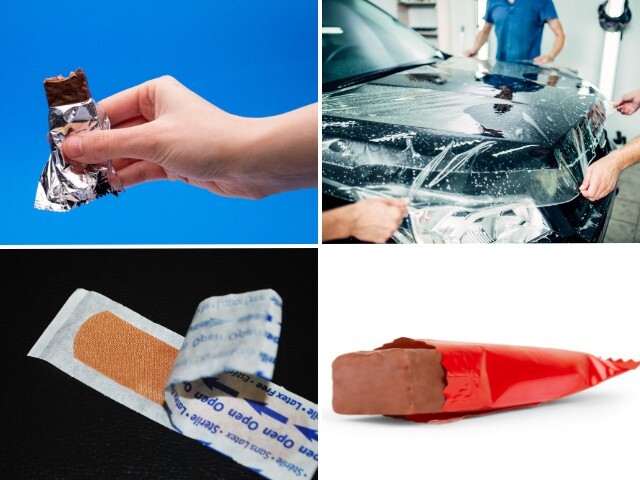
Learn how the right supplier can help you navigate sustainability regulations, non-food applications, and production complexities. Find out how Bostik's cold seal adhesives enhance recycling, design options, and product integrity.
- Increase recycling capabilities: Water-based, cold seal adhesives provide easy wash-off capabilities during the repulp process, allowing your end-use products to enter the recycling stream.
- Enhance design options: Water-based, cold seal adhesives are designed for both paper and film packaging including OPP, PE, PET and compostable substrates, allowing you to use either option on your production lines without adding SKUs or complexity.
- Preserve product integrity: Unlike heat seal technologies, they do not require heat to seal. This enables fast packaging line speeds and does not distort the substrate while it’s getting sealed.
Problem #1: Evolving sustainability regulations make it difficult to rely on cold seal adhesives
As brand owners face pressure to produce more sustainable packaging into the market, it can be challenging to keep up with changing regulations and sustainable certifications. For example, How2Recycle, the leading sustainable certifying body in the U.S., now requires cold seal adhesive to be tested for recyclability when applied to flexible PE film. This means any suppliers that have cold seal adhesives with labels or prequalified How2Recycle letters from May 2022 or prior could be investigated if they do not retest. Further, if you don’t communicate this change with brand owners, it could cause them to advertise sustainability capabilities that are no longer true, causing complications to the recycling process if end-users are recycling items that are no longer deemed applicable.
The right supplier can help you address changing regulations to improve recycling
Suppliers who know the importance of enhancing recyclability understand a certification like How2Recycle is crucial to ensuring confidence for converters and brand owners. Therefore, the right supplier will be quick to act on this change, determining again whether their cold seal adhesive meets recyclability requirements for the flexible PE recycling stream.
Further, the right supplier will test with more than one organization to ensure they are meeting the necessary recycling standards. Along with regaining pre-approval from How2Recycle, they will also ensure their cold seal adhesives meet the Association of Plastic Recycler’s (APR) critical guidance testing using a third-party lab. They will use the most difficult combination of factors to pass, such as product choice and coat weight. This helps you and your brand owners know your supplier’s cold seal adhesives meet performance needs for the most stringent situations. When creating or designing new sustainable packaging, partnering with a supplier that goes above and beyond with testing gives you assurance your package will pass the U.S. sustainable certifying bodies’ requirements, while also saving you valuable resources to complete the testing yourself.
Problem #2: Performance needs are not met for non-food applications
However, if a non-food package must meet specific sterilization requirements to be considered usable in medical-grade packaging, your cold seal adhesive may not be compatible. This could either prevent you from manufacturing new packaging opportunities or cause you slow-downs in finding an alternative solution.
The right supplier can help you address non-food packaging applications
Just like you, the right supplier is thinking about what’s coming next in the packaging industry, and how they can help you address the latest trends. This includes developing cold seal adhesive solutions that extend beyond food packaging, but also considering the specific needs of other industries, such as medical-grade. For example, the right supplier will have a cold seal adhesive option that is developed for sterilization medical packaging. Additionally, they will also provide latex and latex-free options; specifically, latex-free solutions help address allergen concerns. This will enable you to manufacture medical packaging that includes bandage wraps and overwraps to contain medical tubes.
Additionally, the right supplier will provide cold seal adhesives that are formulated with natural rubber latex (NRL) to provide sealing properties. This will allow you to use cold seal adhesives in non-food, industrial packaging applications that require strong seals such as mailers, napkin bands, protective films or blister packaging.
Problem #3: Production complexities can lead to coagulation, forcing packaging to be discarded
- Storage: Cold seal adhesives endure three processing stages that include wet storage, converting and product packaging. Each of these stages involve different storage recommendations. For example, when the cold seal adhesive is in wet form, it needs to be stored above 40°F (4°C), as it is not freeze-thaw stable and needs to be discarded if coagulated. Requirements like this can be difficult to monitor closely during a complex production, especially if the cold seal adhesives sit in the wrong temperatures for prolonged time periods.
- Processing: Most cold seal adhesive formulations contain NRL, which is a shear thickening raw material. This means the viscosity will increase under stress or pressure, which can make it difficult to process cold seal adhesives. If you apply more shear to NRL, it will coagulate from a liquid to semi-solid, resulting in additional downtime to address while converting. While finding a cold seal adhesive formulation without NRL may seem like the solution, NRL is necessary later when a product is being packaged to ensure fast line speeds. This may force you to spend additional time finding which methods are best for you to reduce or eliminate shear in your converting Further, if you don’t solve the problem, it can affect the end-use package performance and lead to more material waste from unusable products getting disposed.
The right supplier will have the expertise to either help you troubleshoot or provide solutions before you’ve even asked about it. This includes offering:
Shipping protection: The right adhesive supplier can alleviate your concerns by shipping cold seal adhesives in heated trucks during the winter months, ensuring the weather does not impact your supply before it arrives to your facility. Further, a supplier can include a freeze indicator on every pallet through winter months to help you track any potential issues. A supplier can also use specific shipping schedules to ensure cold seal adhesives do not sit in a storage container or on the dock for long periods of time during winter months.
Storage temperature recommendations: The right supplier will know how a cold seal adhesives should be stored throughout your processing steps. For example, once the cold seal adhesive is in converted roll form, it can be exposed to low and high temperatures. These rolls should be stored above 25% relative humidity to protect the bond strength. If you realize these storage methods were not met properly, the right supplier can share ways to reverse the problem to recover the bond strength.
Shear reduction methods: While it’s important to include NRL in a cold seal adhesive formulation, the right supplier will know ways that you can reduce shear, which includes:
- Removing all latex-based tubing from your cold seal adhesive station
- Increasing the doctor blade angle
- Adjusting the mixing speed of the holding tank
- Cleaning the equipment of any dried cold seal
- Cleaning while the press is running
Why Bostik is the Right Cold Seal Adhesive Supplier
- Recyclability benefits: Bostik was the first cold seal adhesives supplier to regain pre-approval from How2Recycle and test via APR’s critical guidance testing for our entire Turbo-Seal®
- product line. Our cold seal adhesives are pre-qualified by HowToRecycle for store drop-off on PE film, enabling brand owners to divert packages from the landfill. Further, third party lab testing has proven our adhesives are recyclable when applied to flexible PE film.
- Technical expertise: Our Bostik technical support team will work with you directly to assist with in-person cold seal grade testing to ensure the right one is chosen for your packaging needs. We have two pilot facilities that allow us to ensure our solution offers high performance levels on your substrates, and we can determine whether your products will meet FDA or allergen requirements.
- Troubleshooting guidance: We provide in-person support at our customers’ facilities, which includes yearly line assessments to provide feedback on the handling of a cold seal adhesive solution and operator trainings whenever necessary.
©2023 Bostik, Inc. All Rights Reserved
All information contained herein is believed to be accurate as of the date of publication, is provided “as-is” and is subject to change without notice. To review our full U.S. Legal Disclaimer, visit: https://bostik.com/us/en_US/privacy-policy/legal-disclaimer