Sep 19, 2023 - 3-5 minutes
Bostik Spotlight Q&A: Technical Support with Specialty Hot Melt Adhesives
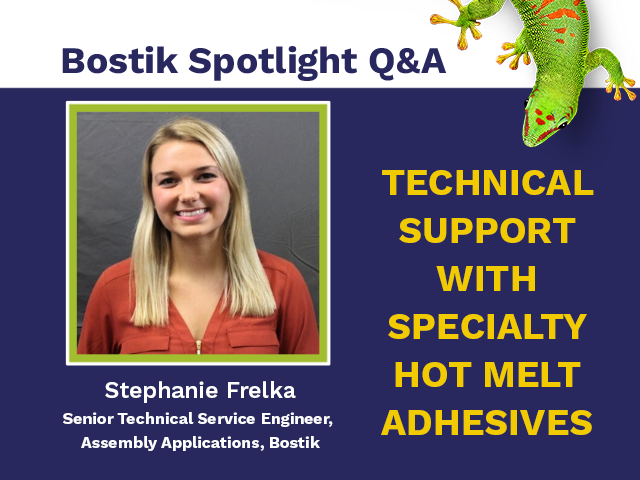
Learn how our technical support team can provide the knowledge and recommendations about specialty hot melt adhesives to enhance your production efficiencies with Bostik's Senior Technical Service Engineer for Assembly Applications, Stephanie Ploch.
With assembly and manufacturing processes continually changing to improve productivity, performance and safety, OEMs like you require adhesive solutions that allow you to evolve whenever necessary. Fortunately, Bostik’s specialty hot melt adhesives make it easy to do so. In this Spotlight Q&A, we sat down with Stephanie Frelka, Senior Technical Service Engineer for Assembly Applications, where she shared how Bostik’s expertise and support with specialty hot melt adhesives can help you address industry demands.
Q: As OEMs look to address demands in their specific markets, such as produce more products faster and reduce environmental impact, what are the main items they’re doing to accomplish those demands, and what should they be aware of with doing so?
A: Even though I work with manufacturers across many different applications and markets, it’s very common for them to ask about how changing a variable in their processing can impact the adhesive regardless of their industry. In particular, they are often trying to do the following:
- Switch adhesives to improve processing efficiencies
- Change a substrate to enhance sustainability or address supply chain needs
- Use one production line for multiple applications
In any of these situations, it’s crucial to make sure your adhesive can still bond properly and provide the performance levels for long-term use. It's also important to consider solutions that can increase worker safety.
Q: This is where technical support can become extremely important; what assistance can you provide as they work to address demands?
A: We conduct testing in a variety of ways to provide answers on adhesive performance to help the manufacturer make a clear decision. Our testing methods include:
- Assessing equipment capabilities: We can guide OEMs to the right equipment options that will be compatible with the adhesive solutions needed to address their specific requirements.
- Testing adhesive capabilities: We can test the OEM materials using with our adhesive solutions to learn about the bond performance, environmental resistance against chemicals or extreme temperatures and the amount of energy required to adhere properly. All these tests will help outline the most suitable conditions and substrates to ensure OEMs are receiving optimal performance and potential opportunities to improve their carbon footprint.
- Noting versatile adhesive solutions: If OEMs need an adhesive solution that can be used on a range of products, we will provide suggestions on which options are most compatible with all their applications, outlining whether the adhesive performs better on some substrates compared to others. This will help OEMs reduce downtime from changeouts.
Additionally, our team will record every step of our testing process and provide the documentation to OEMs. This provides a clear outline of what we did to reach the right performance levels and production efficiencies, for example, helping them repeat the same steps in their own facility to gain the same results. Providing these types of details helps them figure out how the adhesive can tailor to their specific needs.
Q: Your area of focus is specialty hot melt adhesive technology. Can you tell us what they are, and how they offer a versatile, high-performing solution for OEMs across various assembly markets?
A: Specialty hot melt (HM) adhesives are thermobonding solutions that are available in pellets, films, powders or webs, providing OEMs a range of options to easily incorporate them into current processing steps. This means that OEMs can utilize equipment they already own, avoiding an upfront investment when switching their adhesive technology. Specialty HM adhesives are available in a variety of chemistries such as EVA (ethylene vinyl acetate), polyolefin, thermoplastic polyurethane (TPU), copolyester and co-polyamide.
Along with versatile performance, specialty HM adhesives also can help OEMs improve their overall production efficiencies. With fast setup times that do not require drying or curing time, OEMs can increase their production speeds, helping them reduce energy usage. Formulations based on copolyester and copolyamide can incorporate up to 80% raw materials. Specialty HM adhesives are made of 100% solids, heightening worker safety and simplifying your production complexities by eliminating production steps to burn off solvents.
Q: How does Specialty HM adhesive versatility play a role in assessing OEM equipment needs?
A: There are two ways to decide what will be the most useful when incorporating Specialty HM adhesives into OEM processing equipment:
- Choosing Specialty HM for current equipment: Our Bostik team has developed an Adhesive and Lamination Equipment Compatibility Guide, which is a great way for OEMs to first assess what form of Specialty HM adhesives can potentially work on what they currently own for equipment. This document, of course, serves as an informational guide to go alongside discussions our technical support team has with OEMs. If they need another source of equipment, the OEMs can then decide whether it’s worth the investment.
- Considering our network: If it’s necessary to purchase new equipment, we also have a network of converters to help OEMs make those connections. It can be helpful when OEMs want to see if the equipment is useful for a specific time frame or if they know they need the equipment for a product that they’re only producing for a couple years. This can provide a more cost-effective solution to help them utilize the right processing methods for desired performance results without investing in the equipment themselves.
Q: If OEMs experience issues during production after they’ve worked with the technical support team on trialing and determining the right equipment, what can they do?
A: Our technical service team is always here to support OEMs, no matter where they’re at in their production. Even after the testing phases, we are happy to help with troubleshooting any problems during the production. Experts from our team can provide on-site assistance by observing the production to see what’s going wrong, which often involves assessing melting point temperatures, open times or line speeds. From there, our team will provide recommendations for improvement. We are proactive to help OEMs avoid potential problems, but if issues do arise, we serve them with the goal that we can help them find a solution as fast as possible and avoid delaying projects with additional downtime.
Q: In your opinion, how does Bostik’s technical support team separate Bostik from competitors?
A: Along with the technical expertise to help OEMs throughout their production, we also offer global support as the adhesives division of Arkema for new product development. This means we are vertically integrated to help OEMs on-site, no matter their region. We also work with other regional R&D teams to utilize polymers, such as polyamides, in our web adhesives; it helps us offer more customized formulations to meet our customers’ specific needs. Further, our technical support team shares insight with other global regions on solutions we’ve found work well and vice versa, which helps us find answers at a faster rate. When OEMs work with Bostik, they receive much more than just a supply of our Specialty HM adhesives; we ensure our products work effectively with their equipment options so they can make the most of our solutions.
Are you interested in learning how our team can help you utilize specialty hot melt adhesives in your assembly manufacturing? Contact a Bostik expert to learn how you can easily run an efficient production with high-performing results.
Other Relevant Content:
Specialty Hot Melts: Powders, Pellets, Films Webs
Adhesive and Lamination Equipment Compatibility Guide
Turn Up the Heat on Your Performance with Specialty Hot Melt Solutions
©2023 Bostik, Inc. All Rights Reserved
All information contained herein is believed to be accurate as of the date of publication, is provided “as-is” and is subject to change without notice. To review our full U.S. Legal Disclaimer, visit: https://bostik.com/us/en_US/privacy-policy/legal-disclaimer