Jul 19, 2024 - 3-5 minutes
Overcome Limitations with Traditional Two-Part Silicone Adhesive Sealants
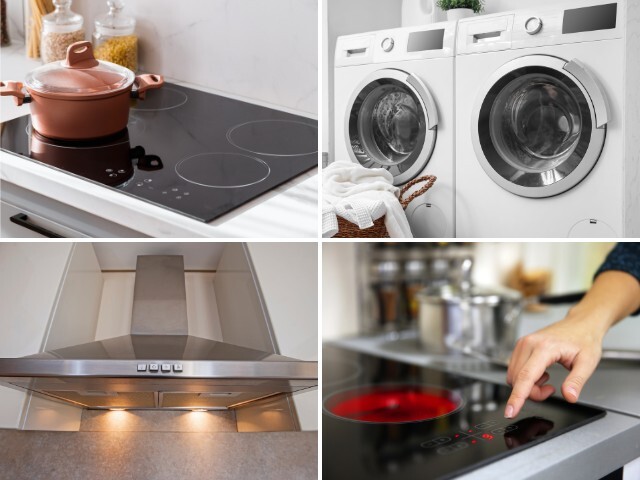
Learn how an alternative adhesive solution can overcome the limitations of traditional two-part silicone adhesive sealants in appliance assembly, enhancing processing capabilities and appliance performance.
In appliance assembly manufacturing, two-part traditional silicone adhesives sealants have been a common bonding solution for white goods applications such as electric stovetops, oven doors, overhead hoods, refrigerators, washers and dryers due to their:
- Flexibility: Two-part silicone adhesive sealants are designed to allow for more movement between bonded parts without compromising the adhesive strength.
- Substrate versatility: Compatible with metals, plastics, glass and ceramics, two-part silicone adhesive sealants allow you to utilize one technology throughout various appliance parts and end-use applications.
- Temperature resistance: Two-part silicone adhesive sealants can handle appliances that experience temperature variations during usage as well as thermal cycling without cracking or losing bond strength, helping to expand the appliance’s lifespan.
However, there are some limitations with two-part silicone adhesive sealants you may not have considered that can impact your processing capabilities and the end-use performance of the appliance. Fortunately, an alternative solution can help address these concerns.
Learn about the limitations with two-part silicone adhesives sealants and why an alternative solution can overcome those issues.
Limitation #1: Long Curing Times
Two-part silicone adhesive sealants have the potential to slow down production times due to their long cure times, especially if two components must be cured before proceeding to the next production step. Until the adhesive sealant is fully cured, the bond strength may not offer high performance to withstand movement or mechanical stress. Moving a component to the next production step before curing is complete can lead to bond failure; however, a production line of mass volume might make it difficult to wait if you’re trying to meet high demands.
How an Alternative Solution Overcomes This Limitation
An alternative adhesive sealant solution comprised of 100% silicone is specifically formulated to help you improve curing times for enhanced processing speeds. Within 15 minutes*, you can begin transitioning your bonded components down the production line due to its fast adhesive build-up. This increased end-cure bond strength is possible due to this alternative’s ability to wet out the surface better than traditional silicone adhesive sealants. With its high cure strength, this alternative solution also provides:
- Flexible strength: This alternative solution builds elastomeric strength for appliance assembly during the curing process. With more than 300% elongation, it will maintain flexibility and moisture resistance while keeping production processes moving.
- High temperature protection: The alternative solution can continually withstand temperatures up to 356°F (180°C), making it suitable for appliance applications that require high-temperature resistance such as electric stove tops and overhead hoods.
Limitation #2: High Costs
Costs can increase to achieve needed performance levels when using traditional, two-part silicone adhesive sealants due to:
- Raw materials: High-quality silicone polymers and other raw materials used in two-part silicone adhesive sealants can be expensive, which can impact the end cost of the adhesive sealant. Further, specialized formulations may only be available in another region, which can require additional costs for shipping.
- Regulatory compliance: In order to achieve desired performance requirements, such as low VOCs, certain chemicals or additives used in the formulation may require regulatory compliance, special handling or proper disposal procedures. This can add costs to your end-use solution. Additionally, you may have to consider additional testing and resources to help ensure the two-part silicone adhesive sealant meets certain standards such as REACH compliance so that you can use it across regions or UL Yellow Card certification for proven safety and performance in electrical applications.
How an Alternative Solution Overcomes This Limitation
Keeping cost-effectiveness in mind, this low-VOC, solvent-free alternative solution is designed to help curve increased expenses by providing:
- Localized supply chain and multi-sourcing capabilities: As a fully-formulated product, this alternative solution eases complexities to help ensure the necessary components are available to meet your desired supply needs. If there is a shortage occurring with a needed raw material, the alternative solution can be formulated with substitute materials in your local region to both address necessary performance levels and mitigate extensive shipping costs.
- Regulatory compliance: This alternative solution’s formulation is already tested and proven to be REACH compatible; this allows you to simplify logistics and use it across regions such as Europe, Asia and the Americas without concerns about meeting various chemical compliance regulations. It has also received UL yellow card certification, proving its bond strength, heat resistance and substrate compatibility in electrical applications meets UL746C safety and performance protocol. Both certifications save you time and resources that would impact your daily operations for testing, which helps reduce production costs.
- Wide application usage: This alternative solution provides strong bonding between substrates such as stainless steel, aluminum and galvanized painted steel, plastics and ceramics. With these compatibilities, you can utilize this alternative solution on a range of appliance applications from electric stove tops and oven doors to refrigerator, washer and dryer glass door assemblies as well as LED lamps. In addition to the appliance market, this alternative solution is also compatible with chrome clad rim wheel replacement in the mobility market as well as on-demand flexible gasket for battery pack on electric vehicles, offering you new manufacturing opportunities to expand your portfolio offerings.
Limitation #3: Undesired Application Results
Traditional, two-part silicone adhesive sealants can sometimes exhibit issues during application, particularly in vertical or overhead applications. Contributing factors can include:
- Viscosity: Two-part silicone adhesive sealants formulated with lower viscosity are more prone to sagging because they are more fluid compared to a higher viscosity formulation. However, a high-viscosity option can also be challenging to ensure a smooth, even application. Additionally, high temperatures can reduce viscosity and increase the risk of sagging, while increased humidity can accelerate curing and potentially reduce sagging. Both factors can result in undesired bonding performance levels.
- Substrate Preparation: As previously mentioned, incorrect mixing ratios or contaminated surfaces can reduce adhesion, which can cause the silicone adhesive sealant to flow more easily and increase sagging. Further, if the right priming or surface preparation steps are not taken for your substrate, poor bonding results can also lead to potential sagging.
How an Alternative Solution Overcomes This Limitation
With the ability to develop fast adhesive strength buildup, this alternative solution is formulated to:
- Protect against sagging: This alternative solution has balanced viscosity while maintaining flexibility and moisture resistance, which helps prevent sagging on demanding applications.
- Keep production processes moving: With fast fixture time, this alternative solution helps streamline processing without compromising the bonding quality and performance of the final assembly.
How Bostik’s Alternative Solution Can Help You
Bostik’s Born2Bond™ SIL-9605 is a two-component, silicone adhesive and sealant alternative that rapidly builds adhesive and elastomeric strength. With its rapid cure for increased production throughput, it provides high-temperature performance to address demanding white goods application needs. SIL-9605 is a solventless solution certified under UL746C, proving it meets industry standards for safety and performance in electrical applications. It also meets REACH compliance.
Additionally, when you work with Bostik, you’ll receive:
- Customized solutions: We are vertically integrated as the adhesives solution segment of Arkema to provide a secure supply chain, helping us achieve your desired performance needs so you can deliver end-use products on time.
- Technical support: Our team of Bostik experts is here to connect with you whenever needed, helping you assess ways to increase end-use performance with equipment you already own. We will also visit your facility to help address troubleshooting when needed.
Are you ready to learn how Bostik’s Born2Bond™ SIL-9605 alternative solution can help you overcome limitations with traditional, two-part silicone adhesive sealants? Contact a Bostik expert to learn how we can improve performance and production for your appliance assembly applications.
*based on Bostik internal testing
Other Relevant Content:
How to Manufacture Appliances Faster Without Sacrificing Performance
Bostik’s Appliance Assembly Applications Receives UL Yellow Card Certification
©2024 Bostik, Inc. All Rights Reserved
All information contained herein is believed to be accurate as of the date of publication, is provided “as-is” and is subject to change without notice. To review our full U.S. Legal Disclaimer, visit: https://bostik.com/us/en_US/privacy-policy/legal-disclaimer