Dec 11, 2023 - 3-5 minutes
Easily Overcome Mechanical Fastener & Structural Adhesive Limitations
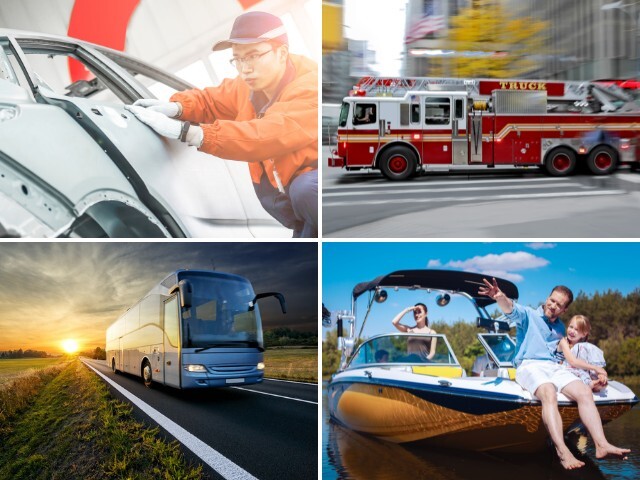
Discover how methyl methacrylate (MMA) structural adhesives overcome the limitations of mechanical fasteners and common structural adhesives, providing enhanced efficiencies in composite, metal and plastic manufacturing for industrial applications.
When manufacturing composites, metals and plastics for industrial applications, it’s critical to ensure your products have durable strength. While mechanical fasteners and many commonly-used structural adhesives have been popular solutions in the past for achieving this durability, they do pose inherent process efficiency limitations that are worth noting.
Find out what those limitations are and how methyl methacrylate (MMA) structural adhesives provide efficiencies you need without compromising performance.
Limitations with Mechanical Fasteners and Many Commonly-Used Structural Adhesives
Mechanical fasteners, such as bolts, screws and rivets, cause the following inefficiencies:
- Increased assembly time: While each mechanical fastener is generally quick to install, the assembly process can still be time-consuming, especially if a large number of fasteners are required, because they must be done one at a time. This can impact production efficiency overall, particularly in high-volume manufacturing.
- Complex surface preparation steps: Achieving high performance from mechanical fasteners often requires precise surface preparation, including drilling and tapping, which can be time consuming. It also can be difficult to fix if a fastening point is placed incorrectly and leaves behind an unnecessary hole in the substrate, as it may require additional resources to fill.
- Downtime when joining dissimilar materials: Joining dissimilar materials with mechanical fasteners can be a lengthy process, too. Unlike structural adhesives, mechanical fasteners only create rigid connections between materials and don’t always provide equal load distribution; when materials are mechanically fastened together and have different coefficients of thermal expansion, the lack of flexibility can lead to increased stress points and potential joint failure that needs to be addressed before a finished product is delivered to the end-user.
Likewise, many structural adhesives can pose process inefficiencies, too.
- Long cure times: In order to provide a durable bond, the chemical formulations of many structural adhesives typically require a long curing process to reach full strength. When running a high-volume production, long curing times can slow down the assembly process. To mitigate this issue, manufacturers may need to implement additional steps such as automated application systems, adding production lines or investing in curing equipment to accelerate the process. Any of these options increase costs and reduce efficiencies.
- Surface preparation: Achieving a strong bond with structural adhesives often requires complex surface preparation since contaminants such as oils or grease can compromise the bond strength. Proper surface cleaning and treatment are crucial but also add complexity and time to the assembly process.
How MMAs Overcome Processing Limitations with Mechanical Fasteners and Other Structural Adhesives
While MMAs are a type of structural adhesive, they overcome key limitations with both mechanical and other structural adhesives, offering:
Reduced Assembly Time
MMAs’ expansive range of substrate compatibilities, including metals, plastics, composites and glass, can save time determining what adhesive solution will be most suitable for bonding two substrates together.
- Compared to mechanical fasteners, MMAs offer easy, continuous application from the same adhesive supply. It takes time to set each mechanical fastener in place accurately before drilling.
- Compared to other structural adhesives, MMAs allow you to utilize one solution on multiple components of an end-use application and reduce changeouts. Further, MMAs help you reduce cycle time due to their fast strength buildup.
Decreased Processing Complexities
Typically offering a 2-5 hour curing time at room temperature with open times of two minutes to 1.5 hours, MMAs provide high green strength with a fast cure. This allows you to move forward in assembly knowing your materials are structurally secure. It also helps reduce overall energy usage because you do not have to spend additional time waiting for a full cure.
- Compared to mechanical fasteners that need to be replaced due to damage, MMAs can decrease downtime and facility energy costs with automated, precise application. Mechanical fasteners also may require surface preparation steps to avoid corrosion that are not required with MMAs, which can help decrease error likelihood.
- Compared to other structural adhesives, MMAs can provide a fast cure to save downtime and decrease facility energy costs that may occur if you’re using additional product lines or curing equipment to move assembly faster with long curing solutions. Further, MMAs offer little to no surface preparation and can reduce process steps that may be necessary with other structural adhesives.
In addition to providing efficiency advantages over mechanical fasteners and other structural adhesives, they also help improve performance. MMAs can provide durable, structural bonding to a wide range of mobility applications because they are compatible with composites, as well as a variety of metals and plastics. They are designed to bond to:
- Metals: aluminum, steel, stainless or galvanized steel
- Plastics: ABS, PMMA, PVC, PC and Elium® composite resin
When compared to mechanical fasteners, MMAs provide high strength and improved fatigue resistance to the final part being bonded as a load-bearing solution for composites, metals, plastics and other substrates. Unlike mechanical fasteners, MMAs have a wide temperature range (-40°F to 302°F (-40°C to 150°C)) and high elasticity to support thermal expansion that could otherwise cause cracks and impact aesthetics, allowing it to bond dissimilar substrates without placing stress on the material.
When compared to other structural adhesives, thixotropic agents that are added to the MMA formulation help control flow properties. This cross-linking builds structural integrity by creating a high thixotropy you may not have with other structural adhesives. This enables MMAs’ rheology to provide fast, precise dispensing that fills vertical gaps and avoids sagging, helping reduce downtime required to fix problems after curing. MMAs’ high cross-linking density also corresponds to improved mechanical properties for chemical stability, temperature resistance and low water absorption.
How Bostik’s MMA Solutions Can Offer Further Advantages
Designed with patented methacrylate technology, Bostik’s SAF and FIT structural adhesive solutions can provide unmatched flexibility, thixotropy and durability while easing complexities in your production steps for industrial applications. With primerless solutions or low surface preparation, SAF and FIT products help reduce overall weight in your dissimilar substrates to improve your environmental footprint. From a flexible range (400% elongation) to being hyper-structural (30% elongation), our solutions show open times from one minute to 90 minutes to fit your specific needs.
Additional Features of Bostik’s MMA Solutions
- Long shelf life: Our MMA solutions range from 12 months (cartridges) to 24 months (drums or pails), helping reduce overall product waste.
- Streamlined resourcing: As the adhesive solutions segment of Arkema, Bostik offers you MMA adhesive solutions that are manufactured in North America, helping you mitigate supply chain concerns. We are also vertically integrated to provide the resources that will help custom formulate solutions to your specific needs.
Are you interested in finding ways to improve processing efficiencies? Contact a Bostik expert to learn how our range of MMA adhesive solutions with our SAF and FIT product line can help you reduce complexities.
©2023 Bostik, Inc. All Rights Reserved
All information contained herein is believed to be accurate as of the date of publication, is provided “as-is” and is subject to change without notice. To review our full U.S. Legal Disclaimer, visit: https://bostik.com/us/en_US/privacy-policy/legal-disclaimer