Jul 3, 2024 - 3-5 minutes
Why EV Batteries Need Silicone-Free Thermally Conductive Gap Filler
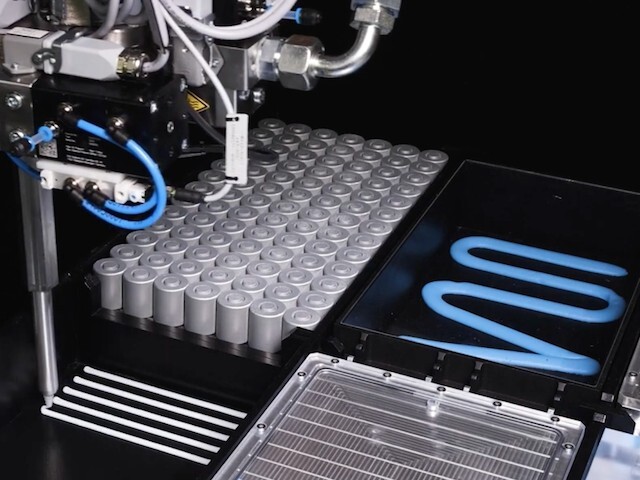
Learn how two silicone-free thermally conductive gap filler (TCGF) solutions can help you replace silicone-based adhesives in your EV battery packs and modules while achieving both high performance and improving processing methods.
While silicone adhesive technologies can be used between EV battery packs and modules, their low volatile siloxanes can cause issues with electric connectivity as the silicone settles over time. Further, silicone adhesives’ particles can deposit on surfaces and make paint and adhesion processes more difficult. As an OEM, you know there are solutions available to mitigate this issue when needed; however, you may not be aware of what may be most suitable to your specific needs. Learn about two silicone-free thermally conductive gap filler (TCGF) options that do not pose electronic connectivity issues and instead can help you achieve both high performance and improved processing methods.
What is a Thermally Conductive Gap Filler?
Thermally conductive gap filler (TCGF) helps fill air gaps and irregularities between the module and the battery pack where hot spots could otherwise take place. This contributes to reduced thermal resistance, allowing for efficient heat flow and a consistent temperature within the battery pack to prevent overheating or degradation of the cells. Additionally, TCGF is removable and repositionable, helping reduce material waste if a change to the placement is needed. Further, once an EV battery is disassembled, you can remove the gap filler to recycle the battery materials.
As a silicone-free solution in both one-component and two-component formulations, TCGF is already formulated to protect against potential damage that can stem from low volatile siloxanes in silicone-based solutions. This includes:
- Migration resistance: Unlike silicone-based materials, two-component TCGF does not migrate over time because it does not contain silicon oil that migrates in silicone-based technologies. This prevents the contamination of sensitive components like the battery cell within the module to increase the battery’s lifespan.
- Reduced degradation: TCGF can experience less degradation over time compared to silicone-based materials, helping to ensure consistent performance.
- Improved safety: TCGF is free of hazardous materials, making it safer for manufacturing and disposal.
One-component, non-reactive and two-component, silyl modified polymer (SMP) TCGF solutions are recommended for high thermal performance between the battery pack and module.
- One-component, non-reactive gap filler is a non-curing paste with an excellent ratio between thermal conductivity and density, helping to prevent hot spots. With low oil separation (~0,3%)*, it offers workability and is easy to remove or apply by automated processing or hand application.
- Two-component, SMP gap filler offers enhanced curing strength that makes it an increasingly desirable solution for ensuring the module stays in accurate position throughout vibration or vehicle shifting. It is compatible with automated bead processes with application times less than a minute.
How to Choose the Right TCGF Solution
It’s important to consider your specific application or processing needs when deciding whether to use one-component or two-component gap filler solutions. The most common priorities when filling the gaps between a module and a battery pack include:
#1: Thermal Conductivity
With TCGF, you can choose the rate at which you want heat to dissipate; this allows you to prevent thermal runaway. Since battery packs have many cells in a confined space, they have high energy density that can lead to increased heat and could cause damage or even fires in extreme conditions. TCGF helps you balance the heat dissipation and energy density, helping to extend the battery’s lifespan.
Recommended TCGF
Both one and two-component TCGF provides a thermal conductivity range between 1.5 to 3 W/K, allowing you options for increased cost effectiveness. However, if density is a main concern, you may want to utilize one-component, non-reactive gap filler as it has an excellent ratio between thermal conductivity and density. As a one-component solution, mixing is not required, allowing you to dispense straight from the packaging and use it without concerns of a mixing ratio altering the thermal conductivity.
#2: Injection Application Method
Compression forces on battery materials can become a concern when trying to ensure there are no air gaps between the module and battery pack, especially when utilizing bead application on lightweight materials that could get damaged from intense force. Using a liquid, conformable gap filler with low viscosity allows you to inject the material so you can fill microscopic gaps and imperfections that you may not be aware are present. As a result, you can also reduce or eliminate strong compression force to better protect other battery components.
Recommended TCGF
If you are concerned about potential damage to other components due to intense compression, two-component TCGF offers optimized viscosity levels that make it easily injectable to avoid creating pressure on other battery components. Its viscosity levels increase five times after 90 minutes at 95°F (35°C)*, allowing for flexibility to combine lightweight materials in the battery pack design.
#3: High Temperature Protection
As mentioned above, high temperatures between the module and battery pack typically stem from charging or overall operational usage. Using a gap filler that can withstand excessive heat can help prevent adhesive degradation that may otherwise stop the module from staying in place during vibration or other shifting.
Recommended Gap Filler TIM:
Two-component TCGF maintains performance in temperatures up to 302°F (150°C), helping the module stay in place throughout charging, discharging or operational use. This also helps reduce overall maintenance due to temperature-related issues and prolongs the battery’s lifespan.
Why Work with Bostik
As the adhesives solution segment of Arkema, Bostik is vertically integrated to help your EV battery modules and battery packs provide high performance while enabling efficient processing. With our range of silicone-free, gap-filler TIM solutions, we offer global support to deliver customized solutions that eliminate the potential risks from low volatile siloxanes in other silicone-based products. Our team of experts work directly with you so that our solutions meet your specific performance and processing requirements.
- One-Component, Non-Reactive Gap Filler: This silicone-free, non-curing solution offers high speed processing with automated bead application. Additionally, with no mixing required, it provides lowered investment costs and reduces application time.
- Two-Component, SMP Gap Filler: As a silicone-free solution, this dual-component system offers fast injection operation with low application pressure to accommodate lightweight materials and high-precision vehicle needs.
Are you trying achieve high performance between your EV modules and battery packs while utilizing efficient processing methods? Contact a Bostik expert to learn how our silicone-free gap filler TIM solutions can help you achieve your goals.
*based on internal testing
Other Relevant Content:
Why You Need to Use Thermal Interface Materials in EV Batteries
Video: Thermally Conductive Adhesives for Battery Applications
©2024 Bostik, Inc. All Rights Reserved
All information contained herein is believed to be accurate as of the date of publication, is provided “as-is” and is subject to change without notice. To review our full U.S. Legal Disclaimer, visit: https://bostik.com/us/en_US/privacy-policy/legal-disclaimer