Find Our Products
Our latest news
Stay aware of our latest news, innovation, and sponsoring actions.
Jun
18
2025
Bostik Announces Regional Polyamide Adhesive Alternatives to UNI-REZ® Products
Bostik, the adhesive solutions segment of Arkema, announced that manufacturers who have relied on ...
Read more
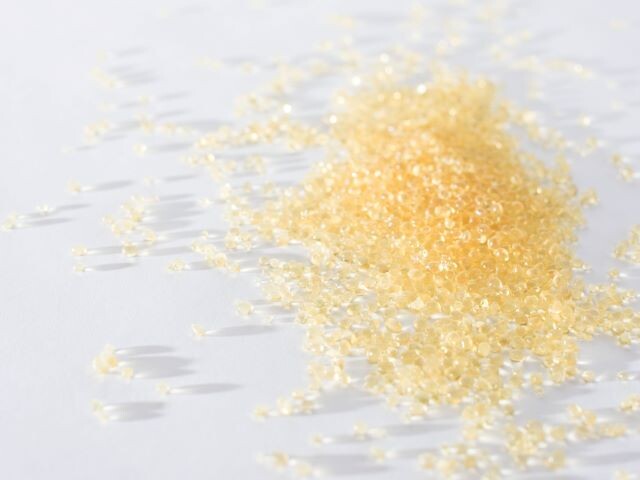
May
19
2025
Bostik Invests in Middleton, Mass. Manufacturing Plant to Increase Capacity and Ability to Support Customer Sustainability Goals
Bostik, the adhesive solutions segment of Arkema, is undergoing a $27 million investment in its ...
Read more
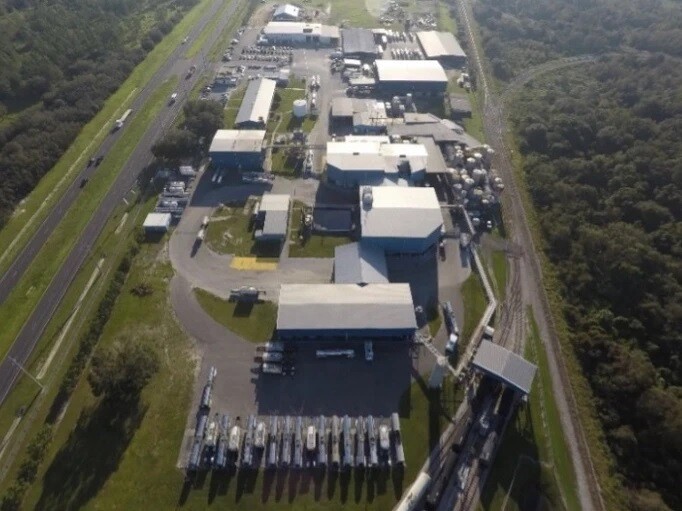
Apr
14
2025
Bostik to Showcase Tailgate-Themed Booth and Innovative Flooring Solutions at NWFA Expo 2025
Bostik is excited to announce its participation in the National Wood Flooring Association (NWFA) ...
Read more
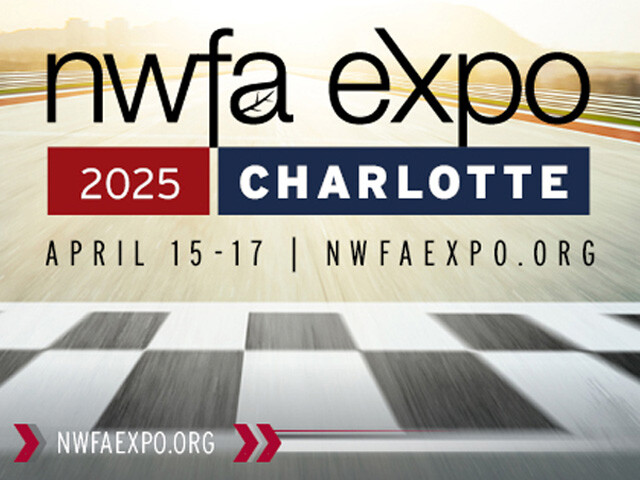
Dec
16
2024
Bostik and Brückner Maschinenbau Partner to Deliver Full-Service Approach to Produce Peelable BOPET Lidding Films
Bostik, the adhesive solutions segment of Arkema, and Brückner Maschinenbau ...
Read more
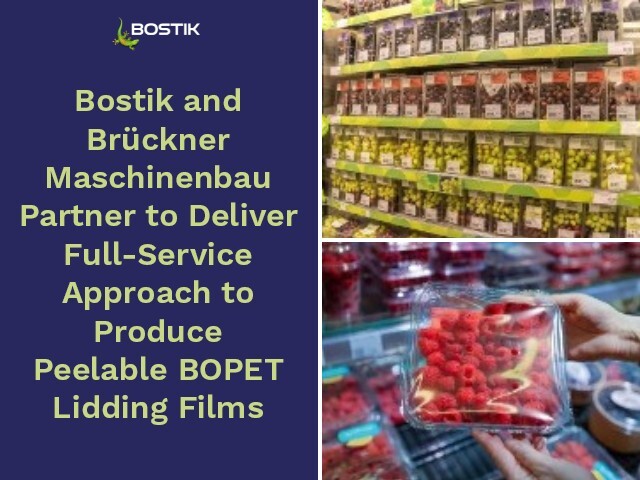