Feb 28, 2025 - 3-5 minutes
Why Polyamide Adhesives in Low Pressure Molding Are Revolutionizing Electronics Protection
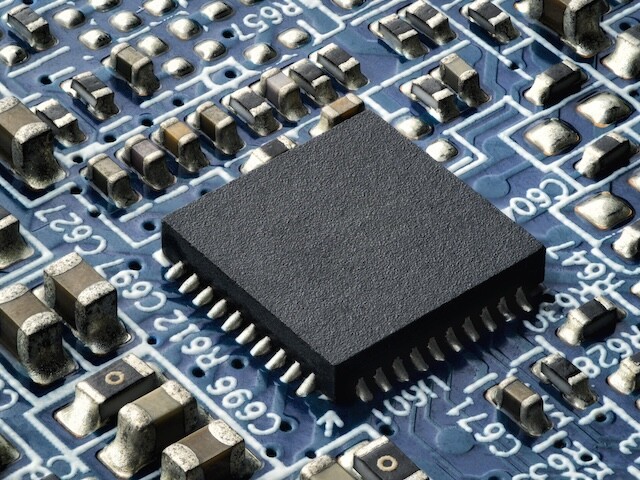
Learn how polyamide adhesives in low pressure molding enhance electronics protection with improved processes, enhanced end-use products, and increased sustainability.
Low pressure molding is rising in demand due to its ability to provide superior protection for electronic components. While all adhesives used in low pressure molding contribute to seal integrity and part protection, you may not know how polyamide adhesives can offer additional benefits. Read about the advantages polyamide adhesives can provide to your electronic component manufacturing.
Advantage #1: Improve Manufacturing Processes
Polyamide low pressure molding solutions operate at low injection pressures, requiring less equipment and reducing energy consumption. As a one-component product, they minimize cycle times and the likelihood of mixing errors, leading to easier manufacturing with less downtime. This makes them a cost-effective alternative to cheap injection molds.
Advantage #2: Enhance End-Use Products
Polyamide adhesives enhance the overall quality of end-use products. Their delicate encapsulation makes them suitable for even the most sensitive electronic components, such as overmolded printed circuit boards. These adhesives are lightweight, water-tight, and UL94 VO approved, offering resistance to:
- High temperatures
- Shocks
- Harsh environments
- Solvents
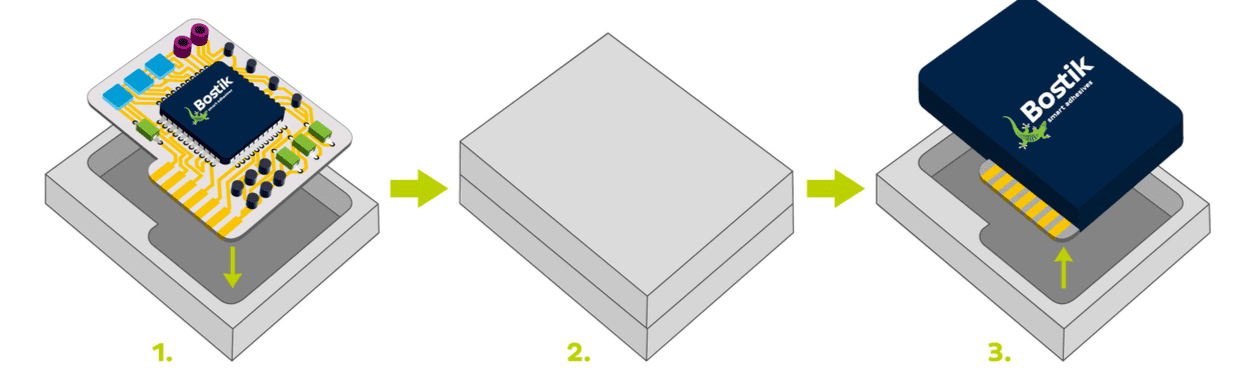
Advantage #3: Increase Sustainability
Polyamide solutions have a long shelf life and produce zero waste, as excess material is recyclable. Being solvent-free and up to 80% bio-based, these adhesives are safe for both workers and the environment. They are ideal for low pressure injection molding machines and low pressure molding systems.
How Bostik Can Help
As the adhesives solution segment of Arkema, Bostik is well integrated to provide low pressure molding solutions. Based on polyamide hot melt technology, our adhesives for low pressure molding offer:
- Easy processability at low temperatures and process pressure as well as fast cycle times of 90 seconds. This helps you increase speeds while meeting the processing needs for delicate structures or sensitive materials. Additionally, no mixing is required to reduce production steps.
- Vibration and chemical resistance, including thermal cycling, fluids, high humidity and UV exposure for improved electrical insulation and performance overall.
- Enhanced sustainability with up to 80% bio-based formulation as well as allowing recyclability of injected material for reduced waste and environmental impact.
Interested in learning how polyamide adhesives can benefit your low pressure molding for electronic components? Contact a Bostik expert to learn how our offerings can protect electronic devices from environmental elements while enhancing performance, processing efficiencies and sustainability.
Other Relevant Content:
Overcome Manufacturing Challenges with Low Pressure Molding Adhesives
Low Pressure Molding Adhesives
Meet Your Goals with the Right Low Pressure Molding (LPM) Method