- Industrial
- Aerospace
- Assembly
- Automotive
- Flexible Packaging
- General Transportation
- Rigid Packaging
- Tape & Label
Sep 25, 2018 - 10 min
5 Adhesives to Help Enhance Sustainability
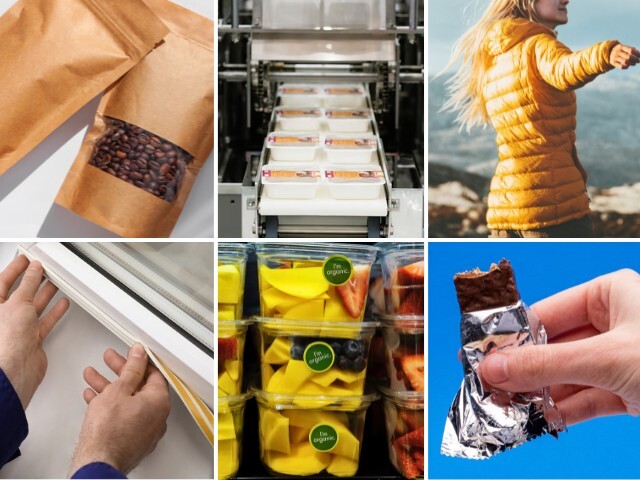
Learn how recyclable, bio-based, compostable, and solvent-free adhesives can reduce carbon emissions, minimize waste, and improve recycling processes while maintaining performance. Find out how Bostik's innovative solutions can help your products comply with regulations and enhance environmental sustainability.
As the global adhesives market continues to grow, manufacturers like you are looking for more sustainable bonding options to address increasing governmental regulations as well as brand owner and consumer environmental concerns. For example, they may be looking for adhesives that are formulated to help reduce carbon emissions or mitigate recycling stream contamination. However, you may be concerned these adhesives won’t maintain the performance and processing efficiencies desired. Fortunately, there are five types of sustainable solutions that prove it’s possible, helping alleviate concerns throughout the value chain while meeting governmental regulations.
Solution #1: Recyclable Adhesives
When designing a product that prioritizes recycling capabilities, it’s crucial that all components and materials offer some form of recyclability or can be easily removed so as not to impact recycling stream effectiveness. Recyclable adhesives help:
- Reduce material waste: Recyclable adhesives are designed to either be easily removed without leaving behind residue or dissolve from the end-use product during the recycling process. This helps ensure the purity of recycling materials so they can be fully reused rather than thrown away due to contamination. As a result, recyclable adhesives contribute to reducing the amount of material waste that ends up in landfills.
- Increase circularity: By cleanly separating from recyclable materials without leaving behind residue, recyclable adhesives enable substrates such as plastic, paper and metals to be processed through recycling streams multiple times for second or third generational usage. This helps manufacturers utilize materials from one overall circular yield versus continuously creating new virgin materials that contribute to increased carbon emissions or potentially create more product waste.
Additionally, manufacturers who use recyclable adhesives can help companies comply with Extended Producer Responsibility (EPR), which holds brand accountable for the end-of-life breakdown of their products. Recyclable adhesives can help those companies demonstrate their products contribute to recyclability to meet regulatory requirements.
Where Bostik’s Recyclable Adhesives Are Used
Packaging
- Cold Seal: Designed with water-based adhesive technology, our cold seal coatings are designed for food and non-food packaging applications including confectionary, protective films and medical. They have passed the Association of Plastic Recyclers’ guidance protocol for PE film, which means when used with PE film, your cold seal meets How2Recycle® Store Drop-off label requirements. This certification makes it easier for consumers to improve the environment and increase purchase likelihood.
- Wash-off: Our adhesives help improve the circular yield of reused plastic material by offering clean label separation from bottle and tray applications, leaving no residue behind so that the plastic material can be reused without contamination. This capability also allows recyclers to use low wash temperatures and caustic solutions, helping to reduce energy usage and increase the quantity of PET packaging moving through recycling streams with enhanced processing efficiencies.
Solution #2: Bio-Based Adhesives
Derived from renewable materials, such as castor oil or other renewable biomass, bio-based hot melt adhesives have no petroleum derivatives in their formulations and include more bio-based carbon molecules than fossil-based. Compared to traditional, fossil-based adhesives’ raw materials, such as gas oils, bio-based adhesives yield less carbon emissions and have reduced environmental impact. Unlike compostable or recyclable adhesives, bio-based adhesives do not need to meet a specific set of guidelines to reach the full potential of sustainable solution offerings; they can simply enhance the end-use product’s environmental footprint through what it offers within its formulation compared to fossil-based solutions.
Where Bostik’s Bio-Based Adhesives Are Used
Packaging
Hot melt, bio-based label adhesives: Like fossil-based adhesives commonly used in ecommerce, weigh scale, health, cosmetics, food and beverage applications, our bio-based label adhesives offer adjustable tack levels that adhere to plastic and corrugate packaging substrates. They are also compatible with the same equipment used for fossil-based hot melt solutions, allowing you to use what you already own to reduce equipment investment.
Assembly
- Bio-based specialty hot melt adhesives: Based on copolyester and copolyamide resins, our thermoplastic, specialty hot melt are available as pellets, powders, webs and films to easily adapt to your equipment needs to enable efficient production. They also well for electronics, footwear, filter media, automotive interior and technical textile applications and quickly set to offer a strong bond.
- Monolithic breathable membrane: Designed to provide breathability to outdoor apparel, footwear and technical textile applications, our membrane offers an alternative solution to traditional membranes while maintaining durable, environmental protection. Partially bio-based out of castor oil, it is produced without fluorinated additives. As a result, it reduces environmental impact while still providing waterproof protection and high breathability for increased comfort. Further, this membrane can be applied via gravure lamination, allowing use of your current equipment.
Solution #3: Compostable Adhesives
Compostable adhesives are formulated with organic materials that break down into natural elements within a certain time frame, having no adverse effect on soil health. Designed to work in existing waste remediation systems, compostable adhesives leave no harmful residue or waste behind once fully composted. The resulting compost will then be used to improve and fertilize the soil. For companies to market a product as 100% compostable, every component must offer compostability; compostable adhesives help companies become one step closer to providing an entirely compostable product.
Where Bostik’s Compostable Adhesives Are Used
Packaging
- Compostable cold seal: We offer the market’s first compostable cold seal certified by the Biodegradable Products Institute (BPI). It provides similar bond strength and performance capabilities to traditional cold seals; however, it is comprised of compostable raw materials. When used with other compostable materials for food and non-food flexible packaging applications, this product enables packaging to be 100% compostable, reducing environmental impact and allowing companies to move one step closer to providing a 100% compostable package.
- Compostable hot melt adhesive: We also developed the market’s first compostable hot melt adhesive. Designed for paper and fiberboard packaging, this BPI-certified adhesive passes compostable ASTM 6400-12 standards, making it compatible with industrial composting facilities. This helps expand compostability to a larger scale beyond the consumer level to reduce environmental footprint. This compostable hot melt technology also offers a broad temperature range of 0 to 180°F (-18 to 82°C) with aggressive tack to help ensure strong bonding to dense board stock and corrugate.
Solution #4: 100% Solid and Solvent-Free Adhesives
Removing solvents from manufacturing materials and processes is a key way to improve your environmental footprint. Adhesives that are comprised of 100% solids or entirely solvent-free can help:
- Decrease carbon footprint: 100% solid and solvent-free adhesives reduce VOC emissions, leading to improved air quality. In manufacturing, using a 100% solid or solvent-free adhesive solution means you do not have to burn off solvents during production that would otherwise contribute to increased carbon emissions. Further, the same amount of 100% solid and solvent-free adhesive supply is lighter in weight compared solvent-based adhesives, making it easier to transport with less fuel consumption.
- Reduce energy usage: You do not need drying ovens, thermal oxidizers or specialized ventilation methods for 100% solid or solvent-free adhesives, which leads to less overall facility energy usage. This also simplifies your production steps, allowing you to process end-use products at a faster rate and complete more in one pass compared to using solvent-based adhesives.
- Improve safety: Eliminating solvents in your production by using 100% solid or solvent-free adhesives means specialized ventilation or storage procedures are not required to protect workers. Flammability risks also decrease to further protect workers and the facility.
Where Bostik’s 100% Solid and Solvent-Free Adhesives Are Used
Packaging:
- UV hot melt pressure sensitive adhesives (UV HMPSAs): Providing an alternative to solvent-based PSAs, our UV HMPSAs are comprised of 100% solids with similar durability levels for tape, graphic and specialty film applications. When compared to solvent-based PSAs, they enable a 48,000-lb annual reduction in solvent consumption according to internal testing**. They also offer fast line speeds that can move up to 5x faster even at high coat weights* compared to solvent-based PSAs since there are no solvents to evaporate.
- Solvent-free laminating adhesives: Used in packaging applications for outdoor, food and personal care items, our solvent-free laminating adhesives are two-component systems based on 100% solids, aromatic urethane chemistry. They offer chemical and UV resistance to increase packaging longevity when stored outside, as well as adhesion to low surface energy substrates such as PSA and cellophane. For food applications, these adhesives have ultra-low aromatic-amine migration with levels less than 0.6 parts per billion in two days* to increase safety. Further, they can be formulated with bio-based raw materials to further enhance sustainability.
- Solvent-free reseal adhesives: Based on water-based technology for flexible packaging applications, our solvent-free reseal adhesives have increased solids percentage compared to other technology, which increases drying efficiencies and reduces energy usage. They also offer adjustable coat weights that enable customization, including the ability to provide narrow peel strength performance. Further, solvent-free reseal adhesives are compatible with pattern application to reduce overall material waste.
Mobility:
- Water-based adhesives: Designed for automotive spraying applications, our one-component solutions are primarily used for bonding to unprimed polyolefin, ABS, ABS/PC blends and fiber board. They are also isocyanate-free to further enhance its sustainability and safety for workers.
- Solvent-free adhesives: Specifically designed for steel-to-steel and lightweight material bonding, our solvent-free adhesives are formulated for body-in-white automotive applications. They also are compatible with lightweight materials such as thin sheet metal to further reduce fuel consumption in the end-use product.
Why Choose Bostik To Help With Sustainable Adhesive Solutions
As the adhesive solutions segment of Arkema, Bostik is vertically integrated to help you find the right sustainable adhesive solution according to your market needs. With our solutions, you can improve your environmental footprint at a level that goes beyond what consumers can achieve on their own, all while helping companies achieve brand trust and meet governmental regulations. When you work with Bostik to choose the right sustainable adhesive solution, you’ll receive:
- Certified solutions: We are continually testing our adhesives with groups such as the Association of Plastic Recyclers (APR) or BPI to achieve important certifications that will help you save valuable time and resources in ensuring your adhesives are meeting sustainable standards.
- Customized formulations: We test customized formulations to help ensure your adhesive is providing your desired performance levels while ensuring it will also help improve your environmental footprint.
- Technical support: Our team is here to provide expertise and help you with throughout trialing processes, as well as troubleshooting during production. We’ll test your substrates with our recommended adhesive offerings utilizing our pilot coating capabilities that can help you continue regular operations while testing new products.
Are you ready to find a suitable sustainable adhesive solution for your manufacturing needs? Contact a Bostik expert to learn how our range of sustainable adhesives can help you improve your environmental footprint while maintaining performance and processing efficiencies.
*based on internal testing
**internal testing statistics based on a 100% solids UV curable acrylic adhesive
Other Relevant Content:
Bostik: We Are Sustainability Enablers
Understanding the Differences Between Compostable and Recyclable Adhesives
©2024 Bostik, Inc. All Rights Reserved
All information contained herein is believed to be accurate as of the date of publication, is provided “as-is” and is subject to change without notice. To review our full U.S. Legal Disclaimer, visit: https://bostik.com/us/en_US/privacy-policy/legal-disclaimer
See also
Back to all articles- Advanced Packaging
- Advanced Packaging
- Advanced Packaging