Dec 6, 2023 - 3-5 minutes
Q&A: Bostik’s Role in NEXTLOOPP’s PP Recycling Initiative
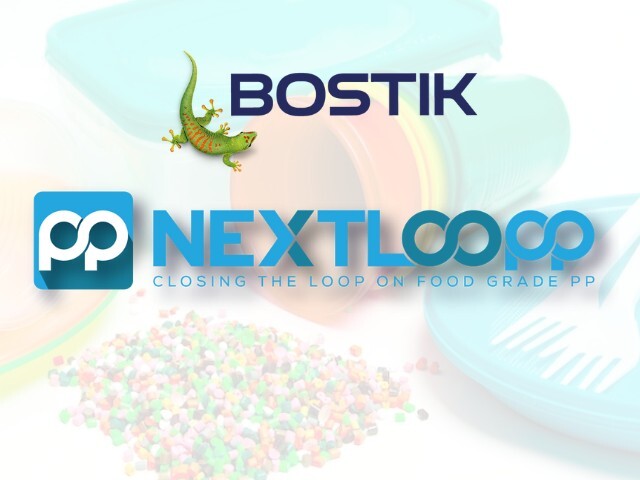
Learn how the NEXTLOOPP project, led by Nextek LTD, is revolutionizing the use of recycled polypropylene (rPP) to balance environmental concerns and food-grade purity. Find out how Bostik is playing a pivotal role in advancing circular recycling, addressing challenges, and providing innovative solutions for rPP.
To date, virgin polypropylene (PP) is typically used in food-grade packaging manufacturing. While this ensures the packaging is pure to pass regulations, virgin PP contributes to an increased carbon footprint and reduced circularity. To solve this environmental concern, rPP is preferred, though it lacks necessary food-grade purity levels due to contaminants.
This challenge is now being addressed by a variety of participating flexible packaging companies through a project Nextek LTD started called NEXTLOOPP. By using cutting-edge decontamination and sorting technology to re-evaluate PP packaging design components, such as the adhesives, NEXTLOOPP is helping the industry find a solution that addresses both purity levels and increases circular recycling.
Bostik, the adhesives segment of Arkema, is the 50th company to join the NEXTLOOPP project. We recently sat down with Eric Parois, Bostik’s Global Market Director for Label and Narrow Web Technologies,Eric Parois, Bostik’s Global Market Director for Label and Narrow Web Technologies, to learn more about this initiative and Bostik’s key objectives as a participant for adhesive solutions.
Q: Why is the flexible packaging industry being encouraged to find ways to reduce the use of virgin PP?
A: The EPA has noted PP to be a safer choice compared to many other plastics because it transmits the lowest carbon emissions, which also protects people working with it. We all know recycling is important, but there are complexities to ensuring recycled plastic, including PP, still passes food-grade packaging regulations when a manufacturer is using it for plastic packaging. It is our responsibility as the suppliers of plastic packaging components to expand the circularity yield rather than only manufacture virgin plastic; one way we can expand the circular yield is by researching ways we can safely reuse different types of plastic, such as PP.
Q: If PP is considered to already have a relatively low carbon footprint, why do we need to reduce it?
A: So far, we know virgin PP has the necessary purity levels for food-grade packaging, but it does not contribute to the circular system – rPP, however, does contribute to circularity, but lacks those needed purity levels. Therefore, Professor Edward Kosier, the founder and CEO of Nextek Ltd, is working to address this issue with industry collaborators involved with the NEXTLOOPP project. Turning PP into a new food tray is basically non-existent right now because it’s difficult to manage the sorting, recycling and the messaging to brand owners. While plastic recycling is evolving, it’s not established for PP the way it is for PET, for example.
Q: The goal for NEXTLOOPP participants is to reevaluate PP packaging design components to increase rPP for circular recycling; what does that entail?
A: Sorting is a big part of what needs to be – and is currently – getting assessed. If we don’t sort out the PP from other plastics, then we won’t have the yield to recycle it properly. NEXTLOOPP is working alongside big sorting companies to find ways we can integrate fluorescent lighting, which will help detect the PP by changing color under ultraviolet light. This technique can help solve the complexities and reduce time in finding the PP for local recycling facilities. While the sortation technique is being addressed, NEXTLOOPP is also considering whether it’s possible to sort PP at high speeds with commercial equipment; this would ensure large-scale machines could implement the sorting changes and run efficiently. As we find ways to increase PP circularity, it’s important to establish an industry standard for sorting that can be easily integrated across Europe and the U.S. We know it will be easier to accomplish this by providing a solution that can be added on to existing equipment.
Q: What does it mean for Bostik, the adhesives solutions segment of Arkema, to be part of the NEXTLOOPP project?
A: It’s just as much of an interest for Bostik to increase circular recycling as it is for the other companies collaborating in the NEXTLOOPP project. As an adhesive supplier, we can be a leader in the flexible packaging industry in finding ways to make a positive difference with this packaging component. Our involvement in the project will include discussing how adhesives impact the recycling capabilities of lidding technologies with recyclable PP trays and wash-off labels preventing contamination in PP recycling streams. We already have a wash-off label adhesive that addresses wash-off capabilities for PET recycling, so we can use what we’ve already learned in that process to formulate a similar solution for PP recycling.
Q: What has Bostik already accomplished with circular recycling that is now helping the NEXTLOOPP project?
A: We already have a prototype wash-off label adhesive for high-density polyethylene (HDPE) recycling, and this is anticipated to be very important in helping us develop a PP wash-off solution. HDPE and PP are both thermoplastics with high melting points and chemical resistance. They can be melted and reshaped multiple times without significant degradation, however, the color impacts whether it can be used for circular recycling. For example:
- Colored HDPE can be granulated, dyed black and reused, but it does not contribute to circular recycling because the shredded plastic is sold into different markets for new products.
- Natural HDPE does contribute to circularity because it is translucent to opaque white and ground up into flakes, moved through a sink float process, extruded, and recycled back into the same product, such as milk jugs.
Since we understand these key features of HDPE and how they are similar to PP characteristics, we can speed up the process to develop a PP wash-off label adhesive solution. While PP is used in the U.S., not many municipalities recycle it; when there are different trays such as monolayer or multi-layer, you must consider how the design elements play into barriers and migration to affect rPP purity levels. For instance, a PP wash-off label adhesive solution can help other NEXTLOOPP collaborators develop rPP packaging components. By knowing our solution removes the label, adhesive residue and inks without contaminating the recycling stream, they can use it in their packaging component and be assured it won’t impact rPP purity levels and prevent it from being used in food-grade packaging. Overall, we have a solid concept to continue building upon that provides a solution for an important component of the package structure.
Are you interested to learn how our work in the NEXTLOOPP project could also benefit your own flexible packaging or label applications? Contact a Bostik expert to learn more about our involvement and how we can help you find the right sustainable solution that addresses your performance and processing needs.
Other relevant content:
Bostik Joins Nextek Ltd’s NEXTLOOPP Project
Colored vs. Natural HDPE: What You Need to Know
Why Label Converters Should Prioritize Mechanical Circularity
Address Key Challenges to Achieve Label Circularity
FAQ: Understanding the First All-Temperature, Wash-off Label Adhesive
©2023 Bostik, Inc. All Rights Reserved
All information contained herein is believed to be accurate as of the date of publication, is provided “as-is” and is subject to change without notice. To review our full U.S. Legal Disclaimer, visit: https://bostik.com/us/en_US/privacy-policy/legal-disclaimer