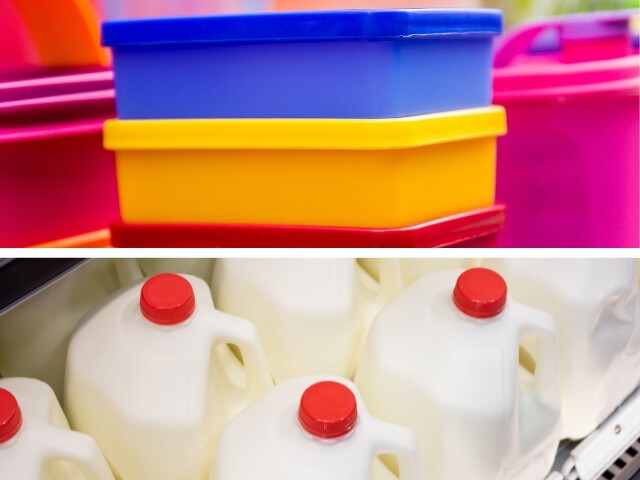
Learn about the various HDPE (high-density polyethylene) types, recycling considerations, and how label adhesives impact both colored HDPE and natural HDPE. Find out how label adhesives play in a role in enabling HDPE to increase recycling for durable packaging applications.
Learn about HDPE, how it differs from other common plastics and what to consider with the different types when choosing a label adhesive.
What is HDPE?
- High environmental exposure resistance: HDPE is resistant to chemicals, UV radiation and moisture, making it suitable for packaging that requires barrier properties or is being used in outdoor applications.
- Versatility: From rigid to flexible grades that are approved for food contact, HDPE can be used for a combination of food and consumer goods packaging such as bottles, containers, medical trays, personal care and cleaning products.
- Temperature resistance: HDPE is compatible for both low and high-temperature applications, which allows it to be used outside of packaging such as automotive or industrial applications.
How HDPE Compares to PET and PP
- Density: HDPE’s high density gives more rigid strength compared to PP, which is why HDPE is used for rigid bottles, containers and pipes over PP. PET has even higher density than HDPE, plus it offers transparency properties that makes PET a popular option for clear plastic packaging. If that transparency is not necessary, HDPE can be more suitable for rigid packaging.
- Recycling capabilities: Both PET and some HDPE can be used to either remake the same products or create new products from their resins or fibers by breaking down their plastics into flakes for extrusion. This decreases the demand for virgin plastic production by keeping current plastic in the circular system and reducing overall energy usage. While PP can be reused for new applications, too, its recycling rates can vary based on market demand and local recycling facility abilities, because it is commonly recycled into products such as battery cases and plastic lumber.
- Ease of Processing: HDPE is relatively easy to process for applications that need structural stability due to its high melt flow characteristics that help simplify extrusion and injection molding. On the other hand, PP has a lower melting point and processing temperature requirement for enhanced energy efficiencies. However, PP will not be able to produce the same level of structural stability as HDPE. Further, PET needs higher temperatures than HDPE, which will require more energy usage during production.
How Different Types of HDPE Impact Label Manufacturing
A label’s construction can be designed specifically for an HDPE packaging application and its specific recycling recommendations. When a label’s construction is designed for an HDPE package, it’s important for you as the label converter to decide what types of HDPE will allow your label to address the application performance needs and recycling requirements. This is because the HDPE type can impact how the label’s adhesive formulation will be able to provide the necessary durability, versatility and temperature resistance.
Types of HDPE to Consider
Even though recycling occurs further into the value chain, you as the converter can impact how your end-use label assists an HDPE package in entering the recycling stream. Further, the application itself can determine what label adhesive will be most effective, which involves understanding the two types of HDPE and how they are recycled.
How Label Adhesives Play a Role in Colored HDPE and Natural HDPE
Knowing whether the package is made of colored HDPE or natural HDPE will help you determine whether your label adhesive needs to provide wash-off capabilities for enhanced circular recycling.
If your end-use label is adhering to a colored HDPE package, it will not need wash-off performance, because it will be ground up during the recycling process with the package and made into another product for a different market. However, your adhesive should provide strong adhesion and recyclable compatibilities; since it will be granulated and reused, it still needs the bonding strength to adhere long-term. The facestock within your label should also be compatible with the HDPE substrate.
A label for natural HDPE does require wash-off capabilities, since the package must be free of any residue before entering the recycling stream. This means your label adhesive must adhere well to the HDPE substrate so it lasts for the lifespan of the application; however, it also has to remove easily with a hot caustic wash from the HDPE package. Since a wash-off label adhesive will be used while it’s recycled as natural HDPE, the label will never enter the colored HDPE recycling stream even when the discolored natural HDPE is moved into that stream.
The right label adhesive solution will offer formulations specifically designed to ensure your label adheres to the HDPE type and can be recycled accordingly:
Colored HDPE: Formulations based on hot melt adhesive technology or tackified, waterborne acrylic adhesive technology provide the necessary adhesion levels to ensure the label will stick to the HDPE substrate during their lifespan and throughout the granulated recycling process. These two options can also allow you to base your decision on your current equipment.
- Hot melt adhesive technology is comprised of 100% solids. After melting upon heat activation, hot melt adhesives form a bond while cooling. This process can occur numerous times, allowing hot melt adhesives to be reusable, which makes them useful for colored HPDE recycling as an individual, recyclable component.
- Waterborne acrylic adhesives offer strong bonding and adhesion with a low environmental impact. This makes them especially useful in applications with environmental concerns, including colored HDPE recycling. Waterborne acrylic adhesives, however, do not require extremely high temperatures like traditional hot melt adhesives, enabling fast processing speeds.
Natural HDPE: Hot melt pressure sensitive adhesives (PSAs) work well for natural HDPE, because they can be formulated to match the specific needs for circular, natural HDPE recycling processes. In particular, they adhere to cold-fill substrates such as dairy products. Further, since dairy products like milk jugs are processed at a fast rate to fulfill consumer demands, hot melt PSAs offer the low-cost, fast adhesion levels to keep up with speedy production and output to end users.
How Bostik Plays a Role in Helping Label Manufacturing for HDPE
Are you ready to expand your label’s recycling capabilities for HDPE packaging? Contact a Bostik expert to learn how our label adhesives can make it easy to provide sustainable integrity across the value chain with your end-use labels.
©2023 Bostik, Inc. All Rights Reserved
All information contained herein is believed to be accurate as of the date of publication, is provided “as-is” and is subject to change without notice. To review our full U.S. Legal Disclaimer, visit: https://bostik.com/us/en_US/privacy-policy/legal-disclaimer