Oct 30, 2023 - 3-5 minutes
Why You Need to Increase rPET Supply Now
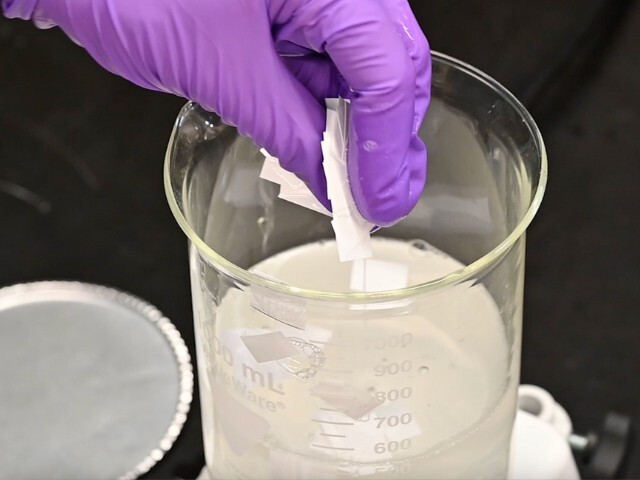
As brand owners are pledging to use recycled packaging, there's a looming concern: Will there be enough recycled polyethylene terephthalate (rPET) materials to fulfill these promises? Read why the demand for rPET is set to surpass supply by threefold in the U.S. by 2030, and explore an innovative solution that could transform the rPET material yield.
As brand owners make pledges to use recycled packaging, there is concern among brand owners and converters alike that there will not be enough recycled polyethylene terephthalate (rPET) materials available for companies to fill out their promises. In fact, if brands follow through on their pledges, a report from the global firm McKinsey & Company states demand for rPET in the U.S. will surpass its available supply by three times by 2030.
Learn why this is the case and how one innovation could provide a solution to increasing the overall rPET material yield.
Understanding rPET vs. PET
Polyethylene Terephthalate (PET) is a common, transparent plastic used for food packaging bottles and trays. When created from oil and petrochemicals, PET is considered virgin plastic because it has never been recycled for second or third generational usage. Therefore, it has not contributed to the circular system yet. Once PET has been cleaned, broken down into flakes and formed into new material, it is considered rPET. It is then reused for other packaging structures, contributing to circularity and helping brand owners show non-governmental organizations (NGOs) they are meeting sustainability goals.
The Challenge with Obtaining Sufficient rPET Supply
As more companies create sustainable goals, the demand for rPET packaging material increases.
However, rPET material can be challenging to obtain, because it can only occur if the PET recycling stream was not contaminated. Contamination can include labels or adhesive residue that remain on the virgin PET even after the wash-off process.
If there is contamination, there may not be enough cleaned, virgin PET that gets yielded to be turned into rPET. This can lead to more virgin PET being developed. Even though virgin PET is technically recyclable, brand owners often do not want to use this PET, because its creation contributes to more energy usage and carbon emissions, hindering their overall sustainability initiative. With rPET, energy usage can be kept low while also keeping plastic in the circular system for second or third generational use.
However, if virgin PET is not able to be cleanly yielded to keep up with rPET demand in the first place, then more virgin PET needs to be created.
Other Factors to Consider with Meeting rPET Supply Demands
In the report, Mckinsey & Company says more than 80 percent of PET material is not being recycled. Aside from notably low recycling rates in the U.S., a lack of set standards across local recycling programs is also playing a factor. Since recycling programs are often organized at a local level, virgin PET recycling is not always prioritized due to infrastructure or transportation costs, as well as governmental mandates. Further, there are missed opportunities to form public-private partnerships for increasing local collection rates in underfunded places or locations that do not conduct curbside recycling. Additionally, not all local recycling programs can afford investments into advanced sortation equipment to enhance rPET supply.
While these complexities are often occurring at the local level, more state legislators are passing Extended Producer Responsibility (EPR) laws for brand owners, which forces them to pay a tax that accounts for their products’ end-of-life disposal process. While the tax varies state to state, there is incentive for brand owners to use recyclable materials so they will not have to pay the tax. With more states passing this legislation, brand owners feel the pressure to utilize rPET material whenever possible, even if there are complexities with local recycling efforts or, as mentioned above, finding wash-off solutions to avoid contamination.
How Adhesives Can Help Increase rPET Supply
Adhesive formulation can affect clean separation from virgin PET material and reduce stream contamination. If the label on PET leaves behind sufficient adhesive residue, that package will be unable to contribute to circularity and be turned into rPET. This is why converters should rely on wash-off label adhesives, which are designed to specifically remove adhesive residue with clean separation from the PET material and enable circular recycling.
However, there are some limitations even with traditional, general-purpose wash-off label adhesives that will impact the ability to meet rising rPET demands:
-
Limited temperature capabilities: General-purpose wash-off label adhesives do not offer full performance on freezer-grade or cold fill applications. This leaves converters with two options; they can decide not to use it at all on cold temperature applications and prevent an entire segment of food packing from contributing to rPET circularity, or they can use it and expect low bond performance when exposed to 40°F (4.4°C) or lower, which could reduce consumer loyalty.
-
Increased processing complexities: Converters may modify to their wash-off label adhesives for capabilities such as increased tack to make sure they have the right performance levels, which could potentially lead to more production steps and impact overall speed-to-market.
-
Possibility for not passing APR protocol: Additionally, not all traditional, wash-off label adhesives are necessarily approved by the Association of Plastic Recyclers (APR) for providing proven wash-off capabilities. Therefore, without this certification, it is possible that the wash-off label adhesive may not be washing off as cleanly as intended and could be impacting rPET creation.
The Wash-Off Label Adhesive Innovation Proven to Help with rPET Supply
While a general-purpose wash-off label adhesive can help increase rPET circularity to some extent, an all-temperature, wash-off label adhesive solution overcomes limitations typically found with general-purpose options.
-
Extended temperature range: Unlike general-purpose, an all-temperature solution provides good tack and quick grab capabilities down to 0°F (-17° C). This means the adhesive will achieve full performance on freezer-grade and cold fill packaging applications, helping expand rPET creation into this segment of food packaging.
-
Simplified processing: As a coater-ready, fully-formulated solution, the all-temperature, wash-off label adhesive is compatible with water-based emulsion equipment, allowing converters to use what they already own by simply adding it to their production line. Additionally, unlike other options, it does not require pretreatment, which further streamlines production. Further, its all-temperature range capabilities enable them to rely on one adhesive solution for all food packaging, reducing downtime for changeouts.
-
APR certification: The all-temperature, wash-off label adhesive has already exceeded or met APR Critical Guidance for PET recycling, ensuring the adhesive solution will provide the capabilities for clean separation to increase rPET. By using a solution already proven to meet the APR standards, converters will save valuable time and resources that they otherwise may need to utilize for a general-purpose solution.
Bostik’s all-temperature, wash-off label adhesive, Flexcryl™ ClearCycle 1000, has been developed as a direct response to improving rPET circularity and overcomes general-purpose wash-off label adhesive limitations. This APR-approved, water-based solution can help the packaging industry increase rPET material by enhancing recyclability with thermoform, bottle and clamshell applications. Contact a Bostik expert to learn how our all-temperature, wash-off label adhesive can help expand abilities to increase rPET creation while maintaining performance and streamlined processing.
Other relevant content:
On-Demand Webinar: Understanding the Value of an All-Temperature, Wash-Off Label Adhesive
Why Label Converters Should Prioritize Mechanical Circularity
Address Key Challenges to Achieve Label Circularity
FAQ: Understanding the First All-Temperature, Wash-off Label Adhesive
©2023 Bostik, Inc. All Rights Reserved
All information contained herein is believed to be accurate as of the date of publication, is provided “as-is” and is subject to change without notice. To review our full U.S. Legal Disclaimer, visit: https://bostik.com/us/en_US/privacy-policy/legal-disclaimer
See also
Back to all articles- Advanced Packaging
- Advanced Packaging
- Advanced Packaging