Mar 27, 2024 - 3-5 minutes
The Impact Adhesives Can Have on PE Film and PET Packaging Recycling Streams and How to Address It
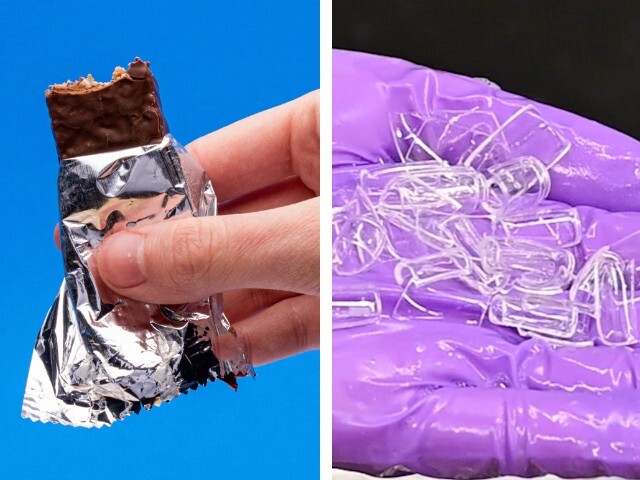
Learn how properly designed cold-seal and wash-off adhesives improve packaging recyclability levels and reduce stream contamination.
In accordance with the Ellen MacArthur signatory commitment, many brands have pledged that 100% of their packaging will soon be recyclable, reusable, or compostable. For North America flexible-film converters utilizing polyethylene (PE) films and label manufacturers creating labels for polyester (PET) packaging, the pledge means they should focus on using materials that help brands improve their package recyclability. This article will highlight key elements in recycling stream effectiveness and how those elements can make more recyclable packaging.
Flexible PE Film Recycling Streams
In 2022, How2Recycle®, an entity that standardizes disposal instructions via packaging’s labels for the public and annually publishes recycling guidelines for packaging using flexible polyethylene (PE), determined that the extent to which cold-seal adhesive coatings influenced PE recycling streams was unclear. It was possible, though not proven, that coatings could in fact be hindering stream effectiveness at least to some extent. If so, this could make the recycled PE film unusable in second- or third-generational packaging. For example, coatings could:
Cause Gels to Form
Cold seal can cause gels, and therefore holes, to form when blowing recycled PE resins into recycled film. If this happens, then it could have a negative impact on the PCR-containing film’s appearance and functionality.
Impact Film Elongation
Cold seal can cause newly recycled flexible PE to lose its rigidity, which can render it unusable for certain end-use applications that require specific film tension.
Decrease Recycled PE Film Properties
Cold seal can decrease recycled PE film properties, including tensile, tear strength, and film thickness. All of these can cause the recycled film to not be fit for its intended end-use application.
Therefore, How2Recycle stated that PE film packaging that uses cold seal needs to get tested via the Association of Plastic Recyclers’ (APR) Critical Guidance Testing for PE Film and Plastic Packaging. If it isn’t tested, or it fails to pass the test within 12 months of the announcement, then:
- All of the brand owner’s existing PE cold seal packaging that once received Store Drop-off recycling status is nullified;
- Store Drop-off labels are removed from existing packaging utilizing cold seal; and
- Brand owners are unable to obtain Store Drop-off certification for any new PE cold seal packaging until testing is completed.
While many in the industry want to get cold seals approved and have been trying to do so since the announcement, not everyone knows how to nor has been able to do so successfully. In particular, the APR requires that all coatings must be converted into coated film to be able to go through the Critical Guidance Testing process. This is because the test measures how PE film structures, including coated PE, perform once turned back into PE resin and later, recycled PE film. Therefore, the entire package structure itself needs to be subjected to and pass the standards – not just the cold seal.
These standards are intentionally designed to be challenging to pass. For example, they entail:
- Test film will be densified;
- Control material will be blended with the test material at blends provided;
- Blends will be extruded to a pellet;
- Materials will be tested for melt flow rate, density, DSC, ash, volatiles, color, and extrusion pressure;
- Films will be produced per the blends previously extruded;
- Film materials will be tested for thickness, tear strength (TD/MD), tensile strength (TD/MD), elongation (TD/MD) and dart impact, specks and gels, and surface appearance.
In order to pass, collaboration along the entire value chain is key; adhesive suppliers, film manufacturers, and film converters need to work together to build a structure and avoid testing delays.
The following information provides an overview as to how an adhesive supplier, a film manufacturer, and film converter created the package structure for testing and its results.
1. Film Grade
When selecting a film grade, the companies chose a film type that contains additives. These additives included white pigment, as it is a common choice in the market. The group theorized that if this film grade passed the test, it would also help eliminate some film additives from the potential list of components that could cause recycling efficiency issues. Additionally, if the structure could pass on a challenging film, then the companies felt comfortable it would pass when using a non-pigmented film.
2. Cold-Seal Grade
Likewise, the companies chose a cold-seal grade that compositionally could have a hard time passing the test, theorizing that if a grade that has a higher risk to gel can pass, then other grades less likely to gel perhaps will pass as well.
3. Cold-Seal Coat Deposition
The companies submitted a structure with a heavy coat weight, so that more coating was on the film. This would make it easier to truly gain an understanding of cold seal’s impact and increase the difficulty in passing the APR’s test. If using a low coat weight, the amount of coating is less, thereby making any impact be less as well and the test easier to pass.
In addition to coat weight, the companies considered how a pattern could influence the structure’s testing results. By opting for a pattern with a high level of film coverage, all lower coverage applications would likely be covered as well. Similar to coat weight, lower coverage applications contain less coating and minimize the effect of cold seal on the film’s recyclability.
As a result of this collaboration, the companies were able to quickly submit a control and an innovative film structure with cold seal to test. Fortunately, the results showed that the cold seal structure was not detrimental to the recycling process per the APR’s test protocol. Additionally, the innovative film often had better performance than the control.
Moving forward, this means that any PE film using the tested cold seal can be recycled in Store Drop-off streams; the cold seal can continue to be used in cold-seal coated PE structures, and it supports efforts to improve recycling stream effectiveness.
PET Recycling Streams
Like PE film recycling streams, PET recycling streams also have been flagged as at risk of contamination. According to Positively PET, PET is the most commonly used (and therefore recycled) plastic in the world due to “virtually limitless life cycle.” However, when the materials used in PET packaging are not all designed for recyclability, they can impact the PET’s overall life cycle. In particular, the APR, an entity that sets forth guidelines on how to improve recycling effectiveness, cites that labels and their adhesives can negatively impact PET’s recyclability if they are not able to be easily and fully removed from PET packaging during the wash-off process at the recycling facility. In particular, the APR cites that the labels and adhesives in the PET recycling stream can increase PET haze percentage or yellow-color properties
If the PET possesses haze or yellowness, it means the label or adhesive did not remove cleanly and has been reincorporated back into the PET. According to the APR’s Critical Guidance, the haze percentage must be less than 10% from the control material, and the yellow level must be less than 1.5 degrees from the control material both when measured from injection molded plaques that have had heat treatments. If the haze percentage or yellow color level exceed the limits, each can negatively impact the PET’s circularity levels in the following ways:
- Reduced PET clarity can make it difficult to sort and identify the material for the recycling facilities’ FTIR scanners after the PET flake has been processed through the recycling stream. This is because the scanners look for color when sorting, which can include clear; if the PET quality is no longer sufficiently clear, the PET will be rejected from the stream.
- Haze- and color-impacted PET itself cannot be recycled. While it can still be turned into other recycled items, such as fibers for clothes or carpets, it can no longer be used to make PET packaging.
- The PET can degrade faster and with impact to its overall strength and structure. In particular, hazy or yellow PET means there are stresses or irregularities in the material, which weaken it. The PET also may have reduced crystallinity levels, which makes it inherently less stable over time, more susceptible to moisture absorption, and can cause physical properties to degrade.
Therefore, it is important to use a label adhesive that offers wash-off capabilities to cleanly remove the label from the PET packaging during the recycling stream wash-off process and leave little to no residue behind. The label and adhesive are then able to be skimmed off the wash solution’s surface and removed from the PET stream. The remaining PET packaging is able to be melted, extruded, and turned into new PET packaging without issue.
In order to assess how effective the label adhesive washes off, it’s important to subject it to the APR’s Critical Guidance Testing. This testing entails the following steps:
- Granulate the PET (turn the bottle into PET flakes);
- Wash the PET flakes;
- Separate the PET flakes from the label adhesives;
- Extrude the PET flakes to make plaques; and
- Test the plaques for haze and color properties.
However, even though a wash-off label adhesive may pass the APR’s Critical Guidance criteria, typical formulations are only able to offer ideal performance levels in applications exposed to temperatures of 40 °F (4.4 °C) or higher. This is because they lack sufficient capabilities to adhere in colder environments. Their glass transition temperature is high, a common property for general-purpose adhesives, and the polymer is not soft enough to allow for sufficient adhesion and wet out at low temperatures as a result. This means that brand owners have opted to either:
- Still use wash-off label adhesives on cold applications (but experience performance failure); or
- Use non-wash-off label adhesives on cold applications (but impact recycling stream effectiveness).
Fortunately, one adhesive supplier has developed the market’s first, APR-approved, all-temperature, wash-off label adhesive to address this market gap.
The following information provides an overview on the value this innovation brings to converters and brand owners alike.
1. Expanded Wash-Off Application Use
Because this adhesive polymer has a low glass transition temperature, it is able to maintain performance even in freezer-grade temperatures lower than 40 °F (4.4 °C). This means that brand owners can use wash-off labels across PET applications without sacrificing performance. Additionally, because it passes APR’s Critical Guidance Testing criteria (CG-PET-02), they do not have to worry about it negatively impacting recycling stream effectiveness. This can aid in increased revenue potential as well, as it helps brand owners’ packaging reduce environmental impact and resonate with consumer sustainability preferences.
2. Simplified Converting Steps
Unlike other wash-off label adhesives, this adhesive possesses intrinsic adhesion properties to commonly used BOPP facestock. No surface pretreatment is needed prior to application. Additionally, this adhesive:
- Can be coated at a low coat weight to reduce material use and costs, and
- Uses materials and equipment converters are already familiar with when manufacturing labels to streamline processing.
Further, as a fully formulated solution, converters do not need to spend the time trying to develop and test an adhesive themselves. This adhesive has also already passed APR’s Critical Guidance Testing; it does not negatively impact PET circularity.
Overall, there are many elements to consider when improving package recyclability, including raw materials, product construction, and the final package structure when used in conjunction with plastic. For both flexible and rigid plastic recycling, additives such as adhesives can play a role in the recycling stream effectiveness. With better testing schematics, protocols, and advancements in adhesive technologies, flexible film converters utilizing polyethylene (PE) films and label manufacturers creating labels for PET packaging are able to use materials that aid in recycling, developing a more sustainable package and providing consumers with responsible packaging for the future.
This paper was originally written by the technical experts at Bostik for Adhesives & Sealants Industry Magazine. If you have any questions about how adhesives can help you utilize polyethylene (PE) films and labels for PET packaging, contact an expert today.
Other Relevant Content:
How to Ensure PE Cold Seal Film Does Not Harm Recycling Streams
©2024 Bostik, Inc. All Rights Reserved
All information contained herein is believed to be accurate as of the date of publication, is provided “as-is” and is subject to change without notice. To review our full U.S. Legal Disclaimer, visit: https://bostik.com/us/en_US/privacy-policy/legal-disclaimer