Oct 30, 2023 - 3-5 minutes
How to Ensure PE Cold Seal Film Does Not Harm Recycling Streams
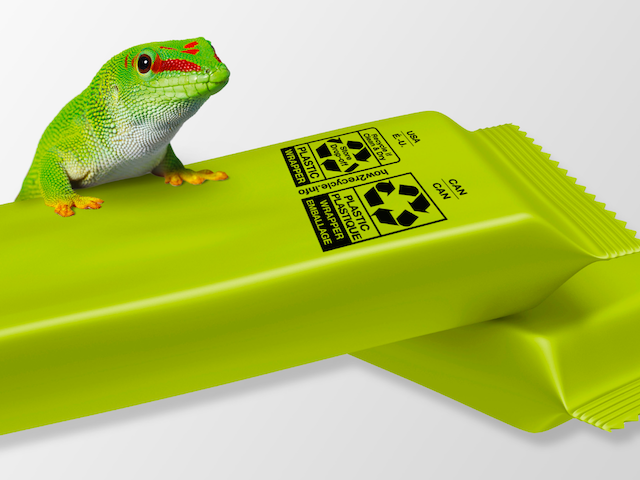
Discover the potential impact of cold seal adhesive coatings on PE film recycling and learn how to design a recyclable PE film structure that complies with How2Recycle's Store Drop-off requirements. Explore the testing process, tips for creating a successful package structure, and how Bostik's cold seal adhesives can assist in achieving recyclability and revenue growth for brand owners.
As a flexible film converter, you may be utilizing polyethylene (PE) films to help your brand owners improve package recyclability, as PE films offer versatility in packaging structures and are compatible for many recycling facilities.
However, ever since How2Recycle® announced it was possible, though not yet proven, that cold seal coatings used in PE film packaging could potentially have a negative impact on PE recycling streams, many converters like you have taken note. Therefore, per How2Recycle, in order for PE film packaging to keep using these coatings and for brand owner packaging to be eligible for How2Recycle’s Store Drop-off labels, the coatings must pass Association of Plastic Recyclers (APR) protocol via third party testing to prove they cause no harm.
Gain insight into cold seal coatings could impact the recycling stream; plus, learn how you can design a cold seal PE film structure that does not harm it and complies with Store Drop-off requirements.
How Cold Seal Adhesive Coatings Could Negatively Impact PE Recycling
While not proven, the following elements about cold seal adhesive coatings could cause impact the PE recyclability for the overall package structure:
-
Gel formation: When blowing recycled PE resins into recycled film, cold seals can possibly cause gels, which form into holes. If gels form, than the resins may not be able to create the film properly with the correct appearance and function capabilities, and the film may not be recyclable anymore.
-
Film elongation: Since cold seal adhesives have more flexibility than PE resin, it’s possible for cold seals to cause newly-recycled, flexible PE film to lose rigidity, making it unusable for applications that require film tension. Therefore, this could limit the options where a brand owner can use the recycled PE film in their package structure.
-
PE film qualities: Cold seals can potentially impact tensile, tear strength and thickness in PE film, which can make it unfit for the intended end-use application.
Therefore, it’s important to ensure your cold seal adhesive coatings do not harm the package structure’s recycling capabilities and for them to be tested.
How to Ensure Your Cold Seal Adhesive Coatings Do Not Harm PE Recycling Streams
How2Recycle® stated that PE film packaging with cold seal adhesives must now be tested through the APR’s Critical Guidance Testing for PET Film and Plastic Packaging. The APR requires all cold seal adhesive coatings to be converted into coated film for the testing process to ensure it performs once turned back into PE resin, and later, recycled PE film. This also means the entire package structure must be tested and pass the standards, ensuring every package element meets the requirements to effectively move through the PE recycling stream and provide multi-generational usage.
To determine if cold seal is compatible with PE recycling streams, the testing requires collaboration along the entire value chain. You also must work with adhesive suppliers and film manufacturers to build a packaging structure that can endure these testing phases:
-
Test film will be densified
-
Control material will be blended with test material at provided blends
-
Blends will be extruded to a pellet
-
Materials will be tested for melt flow rate, density, DSC, ash, volatiles, color and extrusion pressure
-
Films will be produced from blends previously extruded
-
Film materials will be tested for thickness, tear strength (TD/MD), tensile strength (TD/MD), elongation (TD/MD), dart impact, specks and gels and surface appearance
How You Can Create a PE Package Structure That Passes the Test
Through collaboration with your adhesive supplier and film manufacturers, you can build a package structure that passes the test. To do so, consider:
-
Choosing a film grade: Consider testing film with white pigment instead of clear PE to ensure confidence that the cold seal will pass on both clear and pigmented films. Further, pigmented films are common in the market, so it is worthwhile for you to know it passes testing.
-
Choosing a cold seal adhesive grade: Similarly, the cold seal adhesive grade that gets chosen should be one that intentionally will have a hard time passing the test; for example, it could have a high likelihood to gel. This is because if it has an increased risk of forming a gel and still passes the test, then other grades that are less likely to gel will potentially pass more easily, too.
-
Determining the cold seal coat weight: To further increase the difficulty to pass the APR test, consider submitting a structure with a heavy coat weight. This will make it easier to gain a full understanding of the cold seal adhesive’s impact, since there will be more coating on the film. If there’s less coat weight, the test may be easier to pass; however, you will not know the full extent of the coat weight’s impact.
-
Determining the coat seal deposition percentage: It’s also recommended to consider how a pattern may influence the package structure’s testing results. Similar to a heavy coat weight, a pattern that offers a high level of film coverage will ensure lower coverage applications will likely be covered as well. On the other hand, choosing a pattern with low coverage involves less coat weight and will minimize the cold seal adhesive’s impact on the film’s recyclability.
Following these tips have enabled one cold seal PE film structure to pass the test and can help yours do so as well. In particular, the cold seal adhesive was proven not to be detrimental to the PE recycling process, which meant that brand owners’ packaging could be eligible for Store Drop-off recycling. Additionally, the tested cold seal PE film showed higher performance results than other comparative structures in some instances.
How Bostik’s Cold Seal Adhesives Can Help
Bostik’s technical service team has already tested our Turbo-Seal® cold seal adhesives against the APR’s Critical Guidance testing protocol for PE film, successfully passing How2Recyle’s prequalification eligibility requirements for Store Drop-off. With our cold seal adhesives in your PE film package design, along with other approved packaging materials, brand owners can utilize the Store Drop-off label, which increases potential brand owner revenue in addition to recyclability levels.
Our pre-qualified cold seal adhesives also make it easier for you and the rest of the value chain to increase recyclable PE packaging for multi-generational use. While it’s possible our adhesives may be subjected to additional testing in the future as the recycling stream’s impact is studied further, working with a reliable adhesive supplier now can help you save valuable resources to address any potential changes.
Want to learn more about ways to ensure your cold seal adhesives are providing recyclability for PE packaging? Contact a Bostik expert to learn how our solutions can help you choose the right solution.
Other relevant content:
Improve Flexible Packaging Sustainability
On-Demand Webinar: Understanding Expanded Cold Seal Uses and Processing
How the Right Cold Seal Adhesive Supplier Gives You a Competitive Advantage
©2023 Bostik, Inc. All Rights Reserved
All information contained herein is believed to be accurate as of the date of publication, is provided “as-is” and is subject to change without notice. To review our full U.S. Legal Disclaimer, visit: https://bostik.com/us/en_US/privacy-policy/legal-disclaimer