Dec 7, 2023 - 3-5 minutes
How to Close the PP Circular Packaging Loop
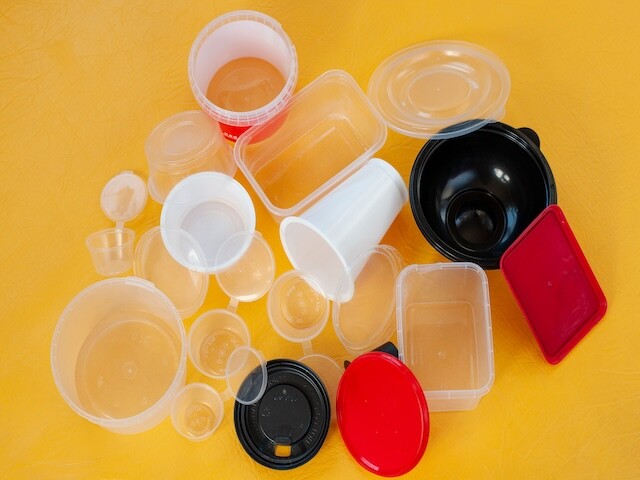
Learn about polypropylene (PP) in food-grade packaging and its potential for circular recycling. Explore how the NEXTLOOPP project is working to improve rPP purity levels and sortation methods with Bostik's contribution and innovations.
As converters like you work to find more sustainable solutions for manufacturing food-grade packaging structures, it’s important to consider how plastics, such as polypropylene (PP), can contribute to circular recycling and reduce their environmental impact. Learn more about PP and what is being done to close the loop on its circularity.
What is Polypropylene?
Polypropylene (PP) is a thermoplastic polymer that is commonly used in food-grade trays, films and bottles. PP is also used in non-food applications such as storage containers, textiles, medical devices, construction pipes and fittings and toys. The packaging industry uses about 30% of all PP, followed by electrical and equipment manufacturing, household appliances and automotive industries. PP offers several features that allow it to be a versatile plastic:
- Non-Reactive: PP does not easily react with combined with other substances, allowing it to maintain structural integrity when exposed to chemicals. Additionally, PP provides protection against many solvents, acids and bases, which allows it to be useful in a variety of environments.
- Durability: PP has a high melting point, making it suitable for food applications where heat resistance is important. It’s also hydrophobic, preventing water or moisture from penetrating the polymer and causing degradation. Further, PP exhibits good tensile strength and toughness with impact resistance.
- Processing ease: PP can also be molded or extruded easily into fibers, films and molded objects. Additionally, PP can be pigmented during manufacturing into various colors. Its smooth surface also allows for easy cleaning and minimizes the potential for chemical residues to adhere to the material.
- Recyclability: It’s becoming more common to recycle PP, and therefore more recycling facilities are starting to accept both clear and colored PP. These plastics can all be melted and reshaped multiple times without significant degradation. Clear PP can contribute to circular recycling because it is formed back into its original product design, whereas colored PP is formed into new recycled products, and does not always contribute to circular recycling.
The Need to Improve PP Circular Recycling
While virgin PP meets purity levels necessary for food-grade packaging, it contributes to carbon footprint and reduced circularity because it must be produced from scratch, requiring new material resources and energy usage every time. rPP can mitigate these environmental concerns because it is recreated from previous PP material that’s been broken down into flakes and recycled as a reusable material source. However, for rPP to still reach food compliance, it must:
- Reach needed purity levels: During the recycling process, contaminants from the original use of the PP, such as food, chemical, or other substance residues, may not be fully removed. If these contaminates are still present in the rPP, the materials can pose a safety risk in food packaging applications, rendering it unable to be used.
- Be able to be properly sorted: In recycling facilities, PP may be mixed and sorted with other types of plastics or materials. This can make it difficult to assess the safety of the final product for food contact, and therefore may prevent more rPP from being separated to eventually contribute to the circular system.
Further, without an established standard for recycling PP around the world, brand owners may not receive the messaging they need to understand rPP is a safe, sustainable solution for their packaging structures and may rely on other plastics such as HDPE instead. If there is less demand for rPP from brand owners, it may take longer to produce a higher circular yield.
What is Being Done to Improve PP Circularity
In order to improve PP circularity, organizations across the flexible packaging industry are collaborating through the NEXTLOOPP project, started by Professor Edward Kosier, founder and CEO of Nextek Ltd. Together, participants are evaluating how to improve:
- rPP Purity levels: There currently is a lack of testing research on whether rPP purity levels are equal to virgin PP. NEXTLOOPP is changing that to ensure rPP is safe for food-grade packaging. Through industry collaboration, testing includes assessing how food contamination differs in rPP from post-consumer sourcing versus post-industrial sourcing. This information will help the industry better understand the best ways to utilize rPP material in multi-generational purposes and how it can support circular recycling.
- PP sortation methods: NEXTLOOPP is working with sorting companies to integrate fluorescent lighting that can detect PP amongst other recycled content by changing its color under ultraviolet light. This technique can help simplify the complexities in finding PP for local recycling facilities, helping them save time and find more reason to include PP sorting in their processes. Additionally, NEXTLOOPP is searching for methods that can help sort PP at high speeds with commercial equipment, as this could make it easier for municipalities to add PP sorting to existing, large scale equipment rather than investing in new machinery.
Further, as more participants join NEXTLOOPP’s efforts to increase PP circular recycling, brand awareness may increase, helping brand owners know why it may be important for them to consider using rPP in their packaging when possible. Many of the companies involved in the NEXTLOOPP project work directly with brand owners or may even be representing brands themselves; therefore, they’ll be able to show how rPP has increased potential to help brands set and reach sustainable goals that can help them track their progress with non-governmental organizations.
How Bostik is Working with NEXTLOOPP
As the adhesives solutions segment of Arkema, Bostik is the 50th participant to join NEXTLOOPP. Our involvement in the project includes identifying how adhesives impact the recycling capabilities of lidding technologies with recyclable PP trays and wash-off labels prevent contamination in PP recycling streams.
Some of our previous work, including our all-temperature, wash-off label adhesive that addresses wash-off capabilities for PET recycling, is helping us use resources and expertise to formulate a similar solution that can improve PP circular recycling. Additionally, our previous research and development in formulating a high-density polyethylene (HDPE) solution is helping us better understand what is required for a PP wash-off label adhesive, as both HDPE and PP are thermoplastics with high melting points and chemical resistance. Understanding these similarities allows us to speed up the process to develop a PP wash-off label adhesive solution that will remove the label, adhesive residue and inks without contaminating the recycling stream. This helps avoid any negative impact on rPP purity levels that could prevent it from being used in food-grade packaging. Further, our knowledge and development are anticipated to help other NEXTLOOPP collaborators develop rPP packaging components to enhance circularity with the entire structure, which can increase overall brand awareness of the importance of PP circular recycling as a result.
Do you want to learn more about our work in the NEXTLOOP project and how it could also improve your own flexible packaging or label applications? Contact a Bostik expert to learn more about our involvement and how we can help you find the right sustainable solution that addresses your performance and processing needs.
Other relevant content:
Bostik Joins Nextek Ltd’s NEXTLOOPP Project
Colored vs. Natural HDPE: What You Need to Know
Why Label Converters Should Prioritize Mechanical Circularity
Address Key Challenges to Achieve Label Circularity
FAQ: Understanding the First All-Temperature, Wash-off Label Adhesive
©2023 Bostik, Inc. All Rights Reserved
All information contained herein is believed to be accurate as of the date of publication, is provided “as-is” and is subject to change without notice. To review our full U.S. Legal Disclaimer, visit: https://bostik.com/us/en_US/privacy-policy/legal-disclaimer
See also
Back to all articles- Advanced Packaging
Q&A: Bostik’s Role in NEXTLOOPP’s PP Recycling Initiative
- Advanced Packaging
The Impact Adhesives Can Have on PE Film and PET Packaging Recycling Streams and How to Address It
- Advanced Packaging