Jul 25, 2023 - 3-5 minutes
Why an Alternative, Bio-Based Membrane is the Right Choice
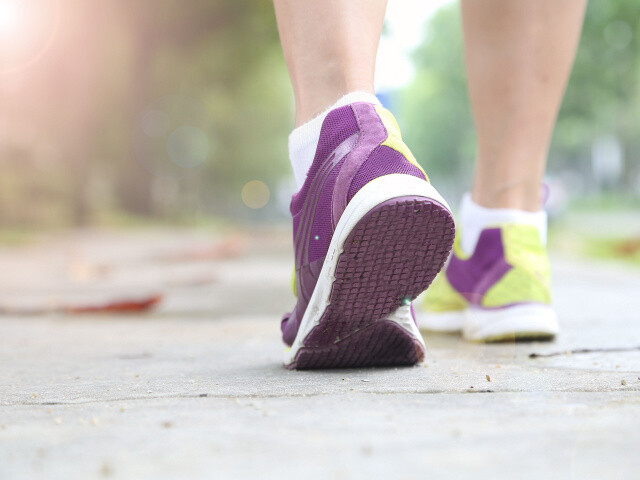
Learn why manufacturers are shifting away from traditional membranes for an alternative, bio-based film membrane that helps them overcome sustainability challenges while maintaining performance standards.
Manufacturers in the footwear, apparel, and technical textile markets know it’s crucial to improve their products’ and processes’ sustainability levels to meet industry demands and end-user concerns. To do so, many are looking to shift away from current membrane materials, such as those that are fully derived from petroleum-based sources or contain fluorinated additives, and looking for alternative, bio-based options instead.
However, it can be challenging to ensure the bio-based solution offers the same breathability, waterproof ability and flexibility performance levels as traditional options—until now.
Find out why many manufacturers are shifting away from traditional membranes and how an alternative, bio-based film membrane enables them to overcome key sustainability challenges while maintaining the necessary performance standards for their end-use applications.
However, it can be challenging to ensure the bio-based solution offers the same breathability, waterproof ability and flexibility performance levels as traditional options—until now.
Find out why many manufacturers are shifting away from traditional membranes and how an alternative, bio-based film membrane enables them to overcome key sustainability challenges while maintaining the necessary performance standards for their end-use applications.
Why Do Manufacturers Want to Replace Traditional Membranes?
Traditional membranes are designed to provide:
- Waterproofing capabilities: Current membranes are comprised of moisture-resistant polymers or additives that mitigate any dampness the consumer may feel when using the application.
- Breathability: These membranes can function as monolithic or microporous. Both allow air vapors to move through and can be formulated to still provide high-temperature stability and chemical resistance.
- Long-term durability: Current membranes offer flexibility capabilities to protect end-use textile applications against wear and tear, as well as high resistance to heat, water and chemicals.
Why is it Challenging to Find an Alternative?
While companies are increasingly interested in finding a different solution, it is challenging to find an alternative membrane that:
- Maintains performance capabilities: The membrane must offer waterproofing and breathability levels to help the end-user feel dry when wearing the end-use application. It must also include flexibility to maintain long-term wear.
- Enhances sustainability: The membrane should be comprised of materials that can reduce carbon emissions, improve end-of-life breakdown and contribute to the circular system.
- Uses similar production methods: It is much easier for manufacturers to implement sustainable solutions that do not drastically change their processes, allowing them to make quick, cost-effective improvements.
Introducing the Solution: A Bio-Based Alternative, Breathable Film Membrane Based off Arkema’s Pebax® Material
Partially bio-based out of castor oil, this membrane based off Pebax® material is free of fluorinated additives and provides durable performance in outdoor and sports technical textiles. Its elastomers possess flexibility and impact resistance, making it ideal for footwear, sports apparel and technical textile applications. It also offers:
- Waterproof protection: This monolithic membrane provides waterproof ability while also allowing water vapor to diffuse by dissipation and absorption. This enables the end-user to continue feeling dry just as they would with a traditional membrane. Even as a bio-based solution, this membrane provides a moisture vapor transition rate (MVTR) of 3000 +- 300 g/m^2/24 hours, similar to or higher compared to other petroleum-based membranes on the market.
- Permeability: This bio-based membrane allows for high breathability due to its monolithic structure while still providing high elasticity.
- Nylon recycling capabilities: This membrane can be mechanically recycled, as it is compatible with nylon recycling streams.
Why Choose Bostik
As the adhesive solutions division of Arkema, Bostik is vertically integrated to provide alternative sustainable solutions. Our film membrane derived from Arkema’s Pebax® material can help protect end-users and the environment from harsh substances that pose dangerous health risks while overcoming limitations of fully petroleum-based membranes. Additionally, our experts work with manufacturers to customize formulations to their specific application needs, which includes determining the right membrane thickness or width to ensure process parameters are met.
Want to provide safer membrane solutions for footwear, apparel, and technical textile applications? Contact a Bostik expert to learn how our film membrane made from Pebax® material can offer enhanced sustainability and key performance.
Contact an Expert
Want to provide safer membrane solutions for footwear, apparel, and technical textile applications? Contact a Bostik expert to learn how our film membrane made from Pebax® material can offer enhanced sustainability and key performance.
Contact an Expert
All information contained herein is believed to be accurate as of the date of publication, is provided “as-is” and is subject to change without notice. To review our full U.S. Legal Disclaimer, visit https://bostik.com/us/en_US/privacy-policy/legal-disclaimer
© 2023 Bostik, Inc. All Rights Reserved
© 2023 Bostik, Inc. All Rights Reserved