Mar 4, 2020 - 10 min
Common Cold Seal Adhesive Problems, How to Address Them
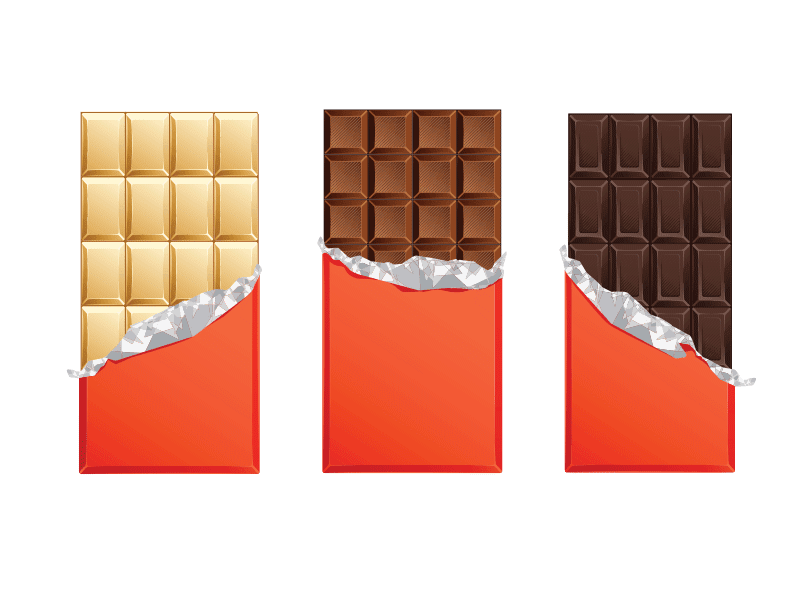
Cold seal adhesives are a popular choice for many flexible packaging applications, offering advantages such as increased line speeds and decreased waste. However, they can be subject to certain cold seal adhesive problems that impact efficiencies as well as product performance and functionality if not resolved. Gain insight into some of these common problems, their causes and how to address them. Blocking Also known as high cling or poor resistance, blocking is when the reel is difficult to separate or the cold seal may be transferring to the opposing surface during unwinding. The following issues cause blocking:
- Wrong release lacquer/film
- Too high or too low of a release lacquer coat weight
- Under-dried cold seal adhesive
- Too high of a cold seal adhesive coat weight
- Excessive winding tension
- Under-stirring of the cold seal adhesive
- Under-drying or under-stirring
- Incorrect cold seal adhesive grade for the application
- Poor adhesion to the base film