Nov 3, 2021 - 10 min
What to Consider When Choosing an Electrically Conductive Adhesive
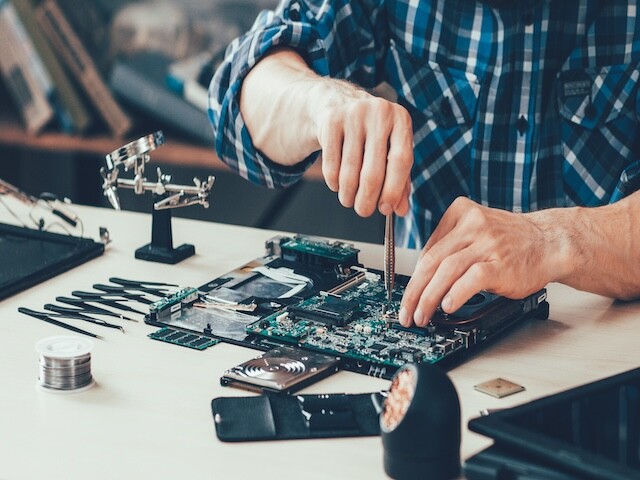
According to a report by Markets and Markets, the demand for electronic adhesives is expected to see a 6.7% CAGR increase by 2025, resulting in a $4.9 billion market. With this increase, electrically conductive adhesives are estimated to become the largest component for the electronic adhesives market, replacing the method of tin-lead soldering.
Electrically conductive adhesives assist in holding electronic parts in place so an electrical current can run through. They can be helpful in applications involving temperature sensitive substrates including LCD displays, touch panels, RFID chips and LED mounting. More manufacturers are turning to electrically conductive adhesives for their simple applications, efficiency and cost effectiveness. However, there are a number of factors to consider when choosing the right electrically conductive adhesive. These include the following:
Isotropic vs. anisotropic: Electrically conductive adhesives fall into one of these two categories. Isotropic conductive adhesives can conduct electricity in all directions, whereas anisotropic can conduct it in one direction. Isotropic are typically used for die bonding, and attaching chips or SMDs. Anisotropic are often used for sensitive products like LEDs, LCDs, and RFIDs.
Electric flux: An electrically conductive adhesive’s ability to store a charge depends on temperature. The higher the glass transition temperature (Tg), the longer the charge will hold at higher temperatures.
Adhesive composition: The base of an electrically conductive adhesive is usually a two-part epoxy, however acrylate and polyester are often used as well. The composition can greatly impact the cost due to the materials used. For example, electrically conductive adhesives with iron are inexpensive, and the most expensive include silver or copper. This can also impact the adhesive’s viscosity, mechanical strength, thermal expansion, shelf life and curing speed.
Electrically conductive adhesives continue to take over the traditional method of soldering for a number of reasons:
Temperature-sensitivity: Electrically conductive adhesives allow electrical parts to be held in place that are sensitive to high temperatures, providing an easier and safer process with strong bonding. For example, conductive adhesives are most notably used for printed circuit boards (PCBs), which involve temperature-sensitive components. RFID tags, LCD displays and touch panels and LEDs will also be warped if exposed to high temperatures, and therefore conductive adhesives serve as a safer solution.
Electromagnetic Protection: electrically conductive adhesives can help create a container to isolate the components inside from electromagnetic signals. This is especially useful for protecting measuring devices that have strong sensitivity to electromagnetic noise or interference.
Application Processes of Electrically Conductive Adhesives
Potting: The process of potting can protect sensitive electronics against environmental dangers. It involves filling an electronic with a hot melt adhesive such as epoxy, silicone or urethane. Here are some of the benefits and drawbacks of those adhesives:
- Epoxy: strength, versatility, high chemical and temperature resistance
- Silicone: chemical resistance, good flexibility, more expensive
- Urethane: more flexible than epoxies, less resistance to chemical and high temperatures
When you select the hot melt adhesive that best suits your needs, you’ll find it will help against harmful risks including chemical spills, changes in air pressure, thermal or physical shock. Potting will also help reduce vibration and moisture. This method is useful to protect printed sensors, power supplies, switches and connectors, circuit boards and power electronics.
It is important to note the importance of air reduction during the application, drying and curing of potting. If air gets trapped inside the potting component, air bubbles can cause performance issues in the finished product.
Encapsulation: This process is an extension of potting. Once the resin has hardened, the electronic is removed from the pot and placed in assembly. Encapsulation helps hold internal components together throughout the production of the electronic device. It can be extremely useful for mass production of chips.
Masking: This process involves mounting an electronic component to another surface, often with tapes or resins. This happens before a coating process film that protects against corrosion, moisture, chemicals and vibration. By using masking adhesives, the component can attach to the surface while not interrupting the main function of the electronic. Masking can be a good option to protect the electronic in high temperatures. It is important to pick a masking adhesive with properties that will correlate with the coating, which can be acrylic, polyurethane, water-based or UV-cure chemistries. Masking is applied to printed circuit boards, which are sensitive to a range of environmental factors.
How Bostik Can Help
Bostik offers a range of adhesives catering to the electronic market including:
- Thermogrip hot melt glue sticks
- 7500 series epoxies
- Thermelt low pressure molding
Contact a Bostik Representative to find out how we can help you with electronic adhesive solutions. Other content relevant to this topic:
Three Ways Smart Low Pressure Molding Adhesives Benefit Your Company
Adhesives in the Electronics Assembly Market
How Adhesives Solve Problems in Electronic Device Manufacturing