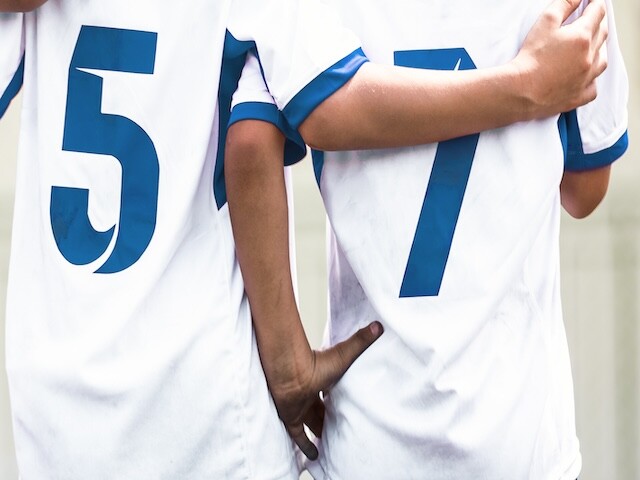
Gain an understanding to the latest trends in custom transfer printing, including enhancing print quality, increasing sustainability, and expanding material compatibility. Learn how hot melt powder adhesive technologies can help you achieve high-quality, durable prints for apparel and promotional products.
In custom transfer printing, it’s important to address market trends that involve
- Enhancing print quality
- Increasing sustainable practices
- Expanding material compatibility
However, it can be difficult to meet these trends while also creating high-quality, long-lasting prints for apparel and promotional products.
Fortunately, your chosen adhesives, such as hot melt powders, can make it easy due to their performance characteristics. Gain insight into these trends and why hot melt powder adhesives can be the right choice for your application needs.
Trend #1: Enhanced Print Quality
Enhanced print quality is a critical trend in custom transfer printing because your ability to provide sharper and more vibrant, detailed prints helps your products catch consumers’ eyes for apparel and promotional products. Further, high-quality prints also can contribute to heightened brand reputation and customer satisfaction.
However, enhanced print quality can be difficult to achieve if the adhesive:
- Enables dyes to migrate: Dye migration can be particularly problematic with dark or vibrant textiles, allowing the dye to turn light prints into unwanted shades. The adhesive needs to create a barrier to block dyes from migrating into the print, enabling the desired colors.
- Allows halo effects: When ink spreads beyond the intended design area, the edges of the print can appear blurry or unprofessional. It's important for an adhesive to be formulated to prevent unwanted, fuzzy edges.
For example, traditional plastisol or water-based adhesives are popular options due to their cost and ease of use, but they often lack the necessary barrier properties to prevent dye migration. Further, they can be problematic for detailed or intricate designs where precision is crucial, allowing ink to spread beyond the design area for a halo effect.
How Hot Melt Powder Adhesives Enhance Print Quality
Hot melt powder adhesives play an important role in enhancing print quality. Their high tack provides strong adhesion, which allows the print to remain intact and vibrant over time. Additionally, these adhesives offer:
- Anti-dye migration to prevent colors from bleeding into each other, which is necessary for maintaining the integrity of multi-colored designs. Hot melt powder adhesives create a physical barrier that helps prevent the dyes from moving into the adhesive layer. Without anti-dye migration, colors can mix and create a blurred or muddy appearance, affecting the overall quality of the print. By preventing this issue, hot melt powder adhesives help ensure each color is distinct for a clear, vibrant print.
- Non-halo effects for clean edges and precise details in the printed design. The formulation of hot melt powder adhesives offers controlled viscosity to help ensure it does not flow excessively, allowing it to maintain clean, sharp edges around the design. This is especially important for intricate designs and text, where precision is necessary for a high-quality appearance.
When these features from hot melt powder adhesives are combined, they provide high-quality, long-lasting prints to meet customer expectations.
Trend #2: More Sustainable Practices
Reducing environmental impact is important across all industries as consumers and companies seek products that contribute to reducing carbon emissions. In custom transfer print, it’s important to incorporate more sustainable materials when possible – however, this can be difficult to achieve if the adhesive does not offer:
- Compatibility with silicone inks: Silicone inks are often utilized in custom transfer print because they are:
- Free of harmful chemicals, which reduces VOC emissions
- High in elasticity, which enables the product to be stretched multiple times without the design cracking, making consumers less likely to discard the end-use product as quickly.
If the adhesive is not compatible with silicone inks, you may have to use other options that are less sustainable and may even lack other performance requirements. For example:
- Plastisol inks perform well with traditional clothing materials but lack flexibility for more elastic materials.
- Second-generation water and solvent-based inks offer flexibility, but not high elasticity for stretching, which does not make them suitable for addressing increased elasticity requirements.
How Hot Melt Powder Adhesives Address More Sustainable Practices
Hot melt powder adhesives contribute to more sustainable practices by being compatible with silicone inks, which are known for their environmental benefits as noted above. Hot melt powder adhesives can be compatible with silicone inks because certain formulations, such as copolyester or thermoplastic polyurethane (TPU) polymers, are designed to have good adhesion to silicone-based materials. This allows them to bond silicone ink to textiles without compromising the ink's flexibility or durability.
Additionally, hot melt powder adhesives are comprised of 100% solids, which means they have no VOCs; this allows them to contribute to reduced carbon emissions in the end-use product. Further, tackifiers help hot melt powder adhesives remain flexible by modifying the polymer's properties, so that it can stretch and bend without breaking.
By using hot melt powder adhesives, manufacturers can produce high-quality prints while following more sustainable practices.
Trend #3: Expanded Material Compatibility
Expanded material compatibility is a significant trend in custom transfer printing due to the need to print on a range of materials including fibers, blends, cotton, lycra and more. This versatility allows businesses the ability to offer more customized products; however, it means all other materials used must be compatible.
Material compatibility is particularly important in custom transfer print, including direct-to-film (DTF) and direct-to-garment (DTG) printing, as it helps ensure the elements used in manufacturing the designs maintain their integrity across different textiles. However, it may not be easy to achieve if the adhesive lacks:
- Softness: A soft adhesive helps ensure the print feels comfortable on the textile regardless of type; a rigid adhesive may prevent this, causing stiffness.
- Flexibility: An adhesive with flexibility helps adapt to the stretch and movement of various textiles. Without flexibility, the adhesive could crack or peel on stretchy materials such as lycra.
While traditional plastisol or water-based adhesives can provide expanded material compatibility, they can lack adequate softness or flexibility. These adhesives can be rigid, leading to stiffness on garments like t-shirts or activewear that require a soft hand feel. They also may not provide enough flexibility to accommodate stretch or movement, resulting in cracking and peeling.
How Hot Melt Powder Adhesives Support Expanded Material Compatibility
Hot melt powder adhesives provide softness and flexibility to enhance material compatibility, which enables long-term durability when printing on different textiles.
Hot melt powders often have a low melting point, allowing them to bond at lower temperatures. This reduces risk of stiffening the fabric to maintain the material's natural softness. Further, with a formulation designed with excellent elasticity, hot melt powder adhesives can stretch and move with the textile, providing a soft feel while preventing cracking. This results in consistent, high-quality direct-to-film (DTF) and direct-to-garment (DTG) printing, making it easier for businesses to expand their product options.
Hot Melt Powder Adhesive Technologies To Consider
When choosing the right hot melt powder adhesive technology, it’s important to think about how you prioritize the trends listed above; the trends you feel are the most important to your custom transfer print needs will help you identify your desired performance needs to determine which hot melt powder adhesive technology may be most applicable.
Copolyester Powder Adhesives
Copolyester powder adhesives are known for their excellent adhesion properties and resistance to dye migration. They allow colors to remain vibrant and do not bleed into each other, maintaining the clarity and sharpness of the print. Additionally, these adhesives provide a non-halo effect, resulting in clean edges and precise details for intricate designs and text. Copolyester powder adhesives also provide:
- Good plasticizer and washing resistance to mitigate cracking and help ensure a flexible, soft touch transfer that will outlast the garment.
- Fast set processing speeds to streamline operational efficiencies, making them suitable for high-volume production.
Thermoplastic Polyurethane (TPU) Powder Adhesives
TPU adhesives are formulated for strong adhesion and high stretch while maintaining the softness and flexibility of the material, resulting in long-lasting comfort. Out of the noted technologies, it has the widest range of compatibility with fibers, blends, cotton, lycra and more, and works well for both direct-to-film and direct-to-garment printing applications, reducing production changeouts and costs. TPU adhesives are also compatible with silicone inks to help support sustainable practices. Further, TPU adhesives fuse at low and medium temperatures, keeping energy usage to a minimum.
Copolyamide Powder Adhesives
Copolyamide powder adhesives are versatile and provide strong adhesion to various fabrics, including cotton, polyester, nylon, and blends. This adhesive technology contributes softness and flexibility to the material, enhancing the overall feel and comfort of the printed product. They offer high wash resistance and excellent plasticizer resistance, allowing the material to withstand the most challenging heat transfer applications, including low surface energy textiles. Further, copolyamide powder adhesives enable quick bonding, easy cutting and low melting points for improved productivity.
Customized Blends
Customized blends of hot melt powder adhesives are tailored to meet specific application requirements, addressing unique challenges in custom transfer printing. These blends can combine the benefits of different adhesive chemistries, such as anti-dye migration, non-halo effect, softness, flexibility, and silicone ink compatibility. By using customized blends, you can achieve optimal performance and quality for specific applications.
Bostik’s Fixatti Powder Adhesives For Custom Transfer Print
As the adhesives solution segment of Arkema, Bostik is a leader in transfer print powder adhesives since acquiring Fixatti. We offer a complete range of hot melt powder chemistries that address key trends for your custom transfer print needs. This includes:
- Certified product portfolio: Our products are Oeko-Tex® certified, helping you save time finding solutions that meet textile industry standards.
Additionally, when you work with Bostik, you’ll also receive:
- Technical support: Our team of R&D experts is here to address your specific application requirements with specialized and custom formulations. With state-of-the-art labs, pilot plants and analytical equipment to test solutions with your substrates on your behalf, our experts allow you to maintain streamlined day-to-day operations.
- Troubleshooting: Our technical sales and service team are here to assist you with any bonding and production concerns.
Are you looking to address key trends in custom transfer printing? Contact a Bostik expert to learn how our portfolio of hot melt powder adhesives can address your transfer print needs.
Relevant Content:
What to Consider with Hot Melts for Heat Transfer Textile Printing
©2025 Bostik, Inc. All Rights Reserved
All information contained herein is believed to be accurate as of the date of publication, is provided “as-is” and is subject to change without notice. To review our full U.S. Legal Disclaimer, visit: https://bostik.com/us/en_US/privacy-policy/legal-disclaimer