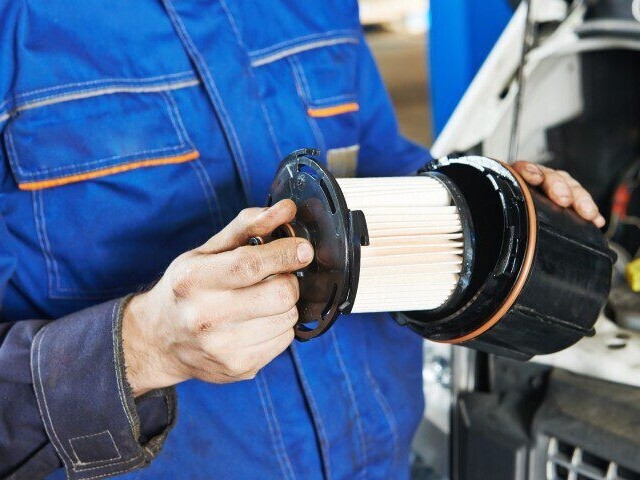
As a filter manufacturer, it’s important to ensure your end-use filters are able to meet key performance criteria, such as chemical protection and high temperature resistance – without negatively impacting production efficiencies. This can be challenging to accomplish for pleat separation and end cap bonding applications especially without the right bonding technology. For example, you may get the end results you need but not within the timeframe your customers want. Fortunately, polyamide adhesives can make it easy to address these challenges and enhance filters overall.
HOW POLYAMIDE ADHESIVES’ CHEMICAL RESISTANCE ENSURES EFFECTIVE FILTER PERFORMANCE
The Problem
While every filter is designed to separate a substance from another material, it is important none of the filter components fail in stressful environments, such as when exposed to solvents, fuel and oil. If the filter adhesives are not chemically resistant, they will degrade or debond. This limits the lifetime of the filter.
The Solution
While manufacturers may consider hot melt polyester adhesives given their chemical resistance levels, these solutions can be too brittle and show cracking after chemical soaking. Additionally, polyolefin adhesives fall short, because they lack sufficient chemical resistance and therefore disintegrate quickly.
Fortunately, polyamide adhesives offer superior resistance against chemicals, including fuel and oils. They are also less susceptible to thermal degradation due to their high softening point. Further, their viscosity and chemical nature allow them to be applied to a variety of substrates, such as aluminum and filter media. Here’s how they help for pleat separation and end cap bonding applications in particular:
How polyamides offer chemical resistance for pleat separation: Polyamide adhesive beads provide structure to pleated filter media, edge seal and pleat stabilization. These applications are crucial for maintaining a filter’s efficiency over time.
How polyamides offer chemical resistance for end cap bonding: Polyamide adhesives maintain their bonds when exposed to these common chemicals in hot liquid filters: motor, hydraulic and transmission oil, alcohol, acetone and organic solvents, plus natural gas, hydrochloric acid and hydroxide. This mitigates potential reactions and metal corrosion in a vehicular system, extending its lifespan.
HOW POLYAMIDE ADHESIVES ADDRESS HIGH TEMPERATURE NEEDS
The Problem
Elevated temperatures have the potential to reduce filtration efficiencies by putting strain on the filtration system through debonding. This can cause pressure drop, lack of protection against various substances or increase emissions. Particularly, if the filter components cannot handle high temperatures, they may contribute to these inefficiencies during the filtration process.
The Solution
While EVAs can be used in air filter applications, they lack thermal stability, threatening an adhesive’s bond strength and filter performance. Additionally, polyester adhesives can withstand high temperatures but lack needed flexibility to achieve true performance needs. Therefore, they aren’t sufficient for addressing high temperature requirements.
Polyamide adhesives, on the other hand, offer a wide range of temperature resistance. While the temperature range depends on the grade, they can typically withstand 300° F (149° C) in motor oil. Even at elevated temperatures, bond strength is maintained, allowing for acceptable filter performance. Further, they have low flammability, reducing the risk of ignition or smoke creation. Here’s how polyamide adhesives help for pleat separation and end cap bonding applications:
How polyamide adhesives address high temperatures for pleat separation: When manufacturing a filter, it’s important to create stability between the pleats for air flow. Polyamide adhesives’ high-temperature resistance protects the bond strength, which therefore prevents the pleats from collapsing and constricting air flow.
How polyamide adhesives address high temperatures for end cap bonding: High-temperature resistance helps maintain crucial bonds when exposed to harsh environments. It’s important for this application’s adhesive technology to resist temperatures ranging from 250⁰ F to 400⁰ F to maintain filter structure and integrity.
HOW POLYAMIDE ADHESIVES ADDRESS EFFICIENCY AND OUTPUT NEEDS
The Problem
Manufacturers need to assemble filtration components in a timely fashion, but they must also ensure the filter sets correctly to ensure proper end-use performance. The bonding method can greatly impact how fast they can move filtration products down the production line.
While they may consider solvent-based, plastisol options, they require oven curing before usage and decrease production speeds as a result.
The Solution
Polyamide adhesives, fortunately, offer fast setting times that can be open anywhere from two seconds to two minutes without affecting the bond strength. As a result, filter assembly can move at the desired pace. This, along with flexibility capabilities, offer easy injection molding and extrusion into cramped spaces that would otherwise be difficult to achieve. Additionally, polyamide adhesives do not require any mixing preparation, reducing downtime. Here’s how they benefit pleat separation and end cap bonding in particular:
How polyamide adhesives address output demands for pleat separation: Polyamide adhesives provide lightweight, fast set speeds to fragile substrates, including cellulous-based, non-wovens and paper filter media. Additionally, polyamide adhesives have low viscosity once applied, which eases the application process by allowing it to form throughout the filter as needed. This also eases the throughput in equipment, so the adhesives do not create thick, difficult tack to clean.
How polyamide adhesives address output demands for end cap bonding: Polyamide adhesives can set quickly and remain flexible yet strong for heavier metal substrates, such as aluminum and steel.
WHY CHOOSE BOSTIK’S POLYAMIDE ADHESIVES FOR PLEAT SEPARATION AND END CAP BONDING
As a global Arkema company, Bostik is vertically integrated in polyamide chemistry, providing more flexibility than the market space for polyamide solutions to help get you what you need where you need it. Our polyamide adhesives, based on a range of hot melt technologies, can benefit pleat separation and end cap bonding as well as other filter assembly applications, allowing for:
- Improved processes: Fast setting times enable faster manufacturing rates with smaller plant space and less complexities
- Increased performance: Chemical and high-temperature resistance capabilities enhance specific filtration end-use and efficiency needs
Additionally, we provide the technical expertise to ensure your polyamide adhesive technology suits your application needs. Through evaluation and testing, Bostik will help you find the right adhesive solution.
Interested in learning more about polyamide adhesives? Contact a Bostik representative to find out how this technology can benefit your filtration application.
You can also check out this other helpful content to understand filter adhesives and their impact on your manufacturing:
Filter Adhesive Uses, Applications and Technologies
On-Demand Webinar: Understanding Your Adhesive Needs in Filtration