Mar 22, 2023 - 3-5 minutes
How Your Paint Protective Adhesive May be Holding You Back
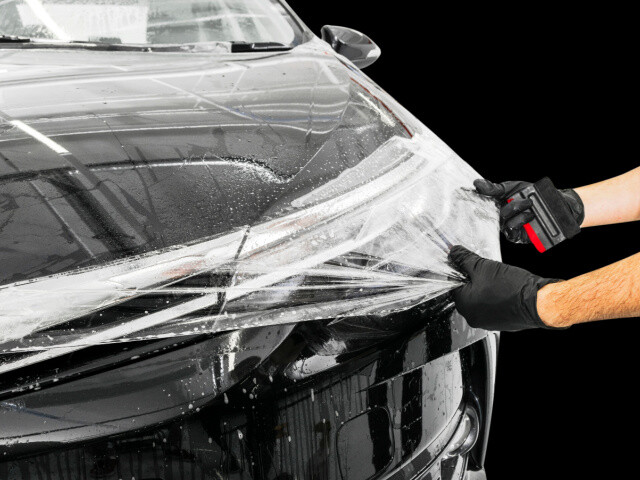
Find out how the right paint protective adhesive easily addresses evolving end-use application needs.
Like many TPU, paint protective film (PPF) manufacturers and installers, it’s important to ensure the film products you’re using address evolving end-use application needs without negatively impacting process efficiencies. However, traditional adhesives can make it challenging to accomplish this as wear times extend, performance requirements rise and pressures for process efficiencies increase. Find out how the right adhesive mitigates those challenges, changing the game in this market and enabling you to easily meet your needs.
Extending Product Wear Times
For PPFs in particular, the market has introduced more durable films that offer extended product wear times of 10-12 years. This is in an effort to better address consumer demand for protection longevity. In the past, films would be able to protect vehicles for up to five years; now, as consumers want to get more value for their investment and keep their purchases looking new for longer, durable films provide a simple way to do that.
Yet traditional adhesives struggle to maintain bond performance for that long. This is because they lack sufficient cohesive strength needed to withstand exposure to the elements after a certain time period. As a result, the durable films end up being removed prematurely. This causes the vehicle to not have protection for as long as intended, because the films only are as long-lasting as the adhesives used to bond them to the vehicle. As a result, traditional adhesives make it challenging for manufacturers to address market demands for extended product wear times.
Yet traditional adhesives struggle to maintain bond performance for that long. This is because they lack sufficient cohesive strength needed to withstand exposure to the elements after a certain time period. As a result, the durable films end up being removed prematurely. This causes the vehicle to not have protection for as long as intended, because the films only are as long-lasting as the adhesives used to bond them to the vehicle. As a result, traditional adhesives make it challenging for manufacturers to address market demands for extended product wear times.
Rising End-Use Performance Needs
Additionally, many PPF manufacturers want to expand their offering into new, high-value applications, such as fast-speed trains and wind turbines. Films in these applications can provide differentiated advantages over historically-used coatings. For example, coatings require more maintenance than films, which increases cost and downtime. Coatings also lack consistent thickness, which impacts aerodynamics and overall energy efficiency.
However, traditional adhesives lack the cohesive strength needed for films to be successful; they are unable to bond to these surfaces and perform under the stringent conditions these applications entail. This has made it essentially impossible for these manufacturers to enter the space and, ultimately, improve the applications’ performance and reduce costs overall.
However, traditional adhesives lack the cohesive strength needed for films to be successful; they are unable to bond to these surfaces and perform under the stringent conditions these applications entail. This has made it essentially impossible for these manufacturers to enter the space and, ultimately, improve the applications’ performance and reduce costs overall.
Increasing Process Efficiencies
Further, as a PPF installer, it’s important to keep processes moving efficiently. However, this has become increasingly difficult as more solid-colored films are introduced to the market. Colored films offer more aesthetically-pleasing options than traditionally clear films, but they are thicker and harder to stretch. This can make installation more time consuming, which can pose problems because the films need to be installed wet. Additionally, installers need to be careful not to over stretch the films, especially on curved surfaces, such as wheel wells and vehicle bumpers. Over stretching can cause the film to get a color crease, creating an inconsistent finish in the results.
When used with traditional adhesives, colored films can be even harder to install. This is because these adhesives possess insufficient tack for wet-applied films, such as PPF. When the tack isn’t high enough, the film may detach over a vehicle’s curved surface.
When used with traditional adhesives, colored films can be even harder to install. This is because these adhesives possess insufficient tack for wet-applied films, such as PPF. When the tack isn’t high enough, the film may detach over a vehicle’s curved surface.
How the Right Solvent-Based Adhesive Addresses These Shortcomings
Aroset® 2100, a self-crosslinking, specialty solution acrylic adhesive, offers the following capabilities that overcome the challenges associated with traditional adhesives:
Ready to get started with a better film adhesive? Contact Bostik today to request a sample of either Aroset itself or a TPU film with the adhesive already applied.
- High cohesive strength for extended wear time and increased performance in stringent applications
- High tack on wet films for improved installation efficiencies
Ready to get started with a better film adhesive? Contact Bostik today to request a sample of either Aroset itself or a TPU film with the adhesive already applied.
©2023 Bostik, Inc. All Rights Reserved
All information contained herein is believed to be accurate as of the date of publication, is provided “as-is” and is subject to change without notice. To review our full U.S. Legal Disclaimer, visit: https://bostik.com/us/en_US/privacy-policy/legal-disclaimer
All information contained herein is believed to be accurate as of the date of publication, is provided “as-is” and is subject to change without notice. To review our full U.S. Legal Disclaimer, visit: https://bostik.com/us/en_US/privacy-policy/legal-disclaimer