Apr 18, 2024 - 3-5 minutes
Address Construction Demands With UV Acrylic PSA Technology
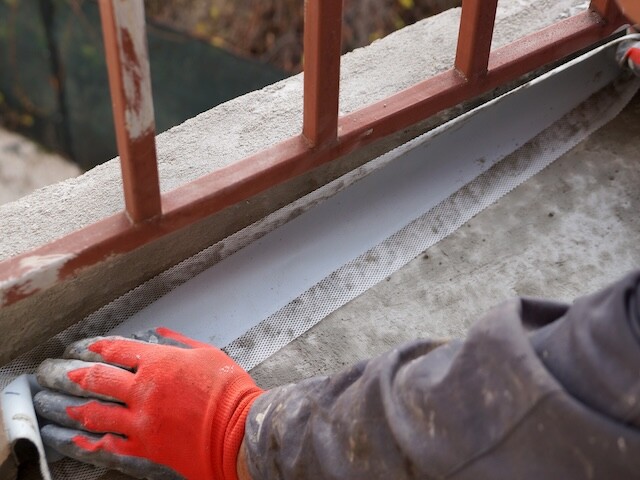
Learn why UV acrylic pressure sensitive (PSA) technology can enhance your tape and membrane materials to address energy conservation and processing demands.
As a manufacturer of adhesive-coated building envelope materials, you likely know there’s growing demand to improve energy conservation throughout homes and to build them faster than in the past. Therefore, your membranes and tapes have become reliable solutions, as they can:
- Improve air tightness: Membranes can help control the overall air permeability, and tapes do not leave air pockets. This helps increase energy efficiencies and prevent material deterioration over time.
- Decrease construction time: Membranes and tapes are also fast and easy to use across applications, helping to speed up construction processes.
However, you may not know that the type of adhesive technology chosen when manufacturing your membranes or tapes can impact how well your end-use customers are able to address these demands. Learn about the benefits UV acrylic pressure sensitive adhesive (PSA) technology can provide to lower your manufacturing costs and how it can enhance your customers’ building and construction tape and membrane materials.
UV Acrylic PSAs: What They Are, Where to Use Them & How They Differ from Solvent-Based PSAs
UV acrylic PSAs cure upon exposure to ultraviolet (UV) light. These PSAs are composed of acrylic polymers mixed with photo initiators, helping to initiate the curing process when exposed to UV light. UV acrylic PSAs can be used in the following building and construction membrane and tape applications:
Membranes
Designed to protect roofing, HVAC and siding, UV acrylic PSAs can be used in:
- Barrier membranes: UV acrylic PSAs help with moisture protection by creating a barrier from water, vapor or other moisture content, helping to provide product longevity.
- Permeable membranes: When an application does require some vapor breathability, UV acrylic PSAs can be formulated to allow moisture to move through the membrane, which can help prevent mold or other deterioration over time.
Tapes
UV acrylic PSAs are compatible with the following tape applications:
- Seaming: UV acrylic PSAs enable seaming tapes to be made cost effective at higher adhesive thicknesses compared to solvent and water-based acrylics. A thicker adhesive coating provides improved bond and gap filling on uneven surfaces to prevent air and water intrusion.
- Flashing: With the ability to coat and cure thicker adhesive films, combined with low energy surface bonding, UV acrylic PSAs can be used in flashing applications where AAMA711 specifications must be met to ensure window flashing provides high strength and waterproofing.
UV curing causes crosslinking between the polymer chains in the adhesive, which aids in increasing cohesion and shear resistance and allows UV acrylic PSAs to provide similar durability levels to that of solvent-based PSAs.
However, they differ from solvent-based in the following ways:
No Solvents
Comprised of 100% solids, UV acrylic PSAs do not utilize solvents, helping to:
- Increase safety and sustainability: UV acrylic PSAs do not require drying ovens or special ventilation or storage methods like solvent-based PSAs, helping to reduce flammability hazards in addition to overall carbon emissions.
- Reduce costs: Based on internal testing, UV acrylic PSAs can be up to 70% less expensive to ship compared to solvent-based PSAs*. With solvent-based PSAs, a portion of the supply is solvents that get burned off, resulting in less usable material; however, with UV acrylic PSAs that are 100% solids, you can use the entire supply in the drum, increases your supply yield.
- Increase productivity: Lines speeds with UV acrylic PSAs can move up to 5x faster even at high coat weights* compared to solvent-based PSAs. This is because no solvents need to evaporate.
Thicker Cure
Additionally, compared to solvent-based, UV acrylic PSAs offer a thicker cure (7.5 mils vs 5 mils). This capability improves wet out on uneven surfaces which, in turn, leads to stronger bond strength.
Cost Efficiencies
UV acrylic PSAs do not require as much supply yield to achieve a thick coat weight compared to solvent-based PSAs, which lowers costs overall and increases efficiencies for both supply orders and shipping. This is because they are 100% solids. Additionally, based on internal testing*, UV acrylic PSA production speeds result in reduced costs when compared to solvent-based PSAs, including:
- 82% less hours to produce MSI/year (at coat weight)
- $65,000 savings/year based on adhesive cost
This can be beneficial when manufacturing membranes or tapes at high volumes, allowing you to quickly move large modular components through your production line at a fast rate.
It is also important to note that you will have to consider investment costs for incorporating UV acrylic PSAs into your production. The costs, however, can vary depending on whether you’re currently using solvent-based PSA equipment or hot melt PSA equipment. You can learn more about what to expect with incorporating UV acrylic PSA equipment here.
Why Use UV Acrylic PSAs in Your Building and Construction Membranes and Tapes
Both membranes and tapes within building envelope applications can utilize UV acrylic PSAs. UV acrylic PSAs offer the following benefits for building and construction tape applications specifically:
Increased Energy Efficiencies
Based on internal testing*, UV acrylic PSAs can enable a reduction of up to 700 tons in carbon emissions, as they are made of 100% solvents and enable high processing speeds. Additionally, UV acrylic PSAs allow a membrane or tape to completely adhere and provide full protection – they do not puncture holes into building envelope like mechanical fasteners, which allows vapor or hot and cold temperatures to move through and impact the overall energy efficiencies of the home. However, if necessary, UV acrylics can be formulated to allow for moisture permeability.
Faster Manufacturing and Installing Speeds
Because UV acrylic PSAs are 100% solids, no solvents need to first evaporate. This means they can be applied in thick coat weights more efficiently than solvent-based while still offering the high peel and gap filling capabilities necessary to protect roofing, windows and doors.
Also during installation, adhesive coated materials that use UV acrylic PSAs enable increased construction speeds because they reduce installation complexities. Compared to uncoated materials that are stapled, UV acrylic PSAs do not require two installers to attach the material and are accommodating to labor shortages. Further, UV acrylic PSAs eliminate additional time required for re-stapling, which happens often with uncoated materials.
How Bostik Can Help
Benefits of a Total Systems Approach
Our UV acrylic PSA technology can be used in both membranes and tapes; in other words, the same product SKUs work for both application categories. As a result, this provides:
- Improved assurance that the overall warranty of the adhesive products will be consistent with one another throughout the home, preventing numerous maintenance updates or repairs at different times during the home’s lifespan.
- Consistent product quality while knowing the products are all from the same supplier, allowing them direct access to the right product experts if they experience issues or have questions.
Why Purchasing UV Acrylic PSAs for Membranes and Tapes from the Same Supplier is Helpful
Bostik manufactures high-performing UV acrylic PSAs for building and construction applications, including membranes and tapes. This helps you provide a total systems approach to your customers while allowing you to replace solvent-based PSAs and provide improvements in energy efficiencies. Based on internal testing*, when compared to solvent-based PSAs, our UV acrylic PSA formulations help enable:
- 63% less pounds in adhesive volume per year
- 48,000-lb annual reduction in solvent consumption
We also understand you may have questions about what’s involved in making the switch to UV acrylic PSAs. That’s why we provide:
- Technical support: We’ll work with you directly to provide suggestions on customized adhesive formulations for your specific needs. Our pilot coating capabilities help you continue regular production while testing UV acrylic PSA technology on membranes or tapes.
- Troubleshooting: We’ll help you address issues on-site to ensure you have a seamless transition if switching equipment from solvent-based PSA equipment or adding UV lights to hot melt PSA equipment.
Are you ready to find improved energy-efficient solutions to address trends for building and construction applications? Contact a Bostik expert to learn how UV acrylic PSAs can help you remove solvents from your production while enabling high performance in membranes and tapes.
*internal testing statistics based on a 100% solids UV curable acrylic adhesive
©2024 Bostik, Inc. All Rights Reserved
All information contained herein is believed to be accurate as of the date of publication, is provided “as-is” and is subject to change without notice. To review our full U.S. Legal Disclaimer, visit: https://bostik.com/us/en_US/privacy-policy/legal-disclaimer
See also
Back to all articles- Advanced Packaging
- Advanced Packaging
- Advanced Packaging