Dec 15, 2023 - 3-5 minutes
What to Know Before Selecting a Specialty Film Pressure Sensitive Adhesive
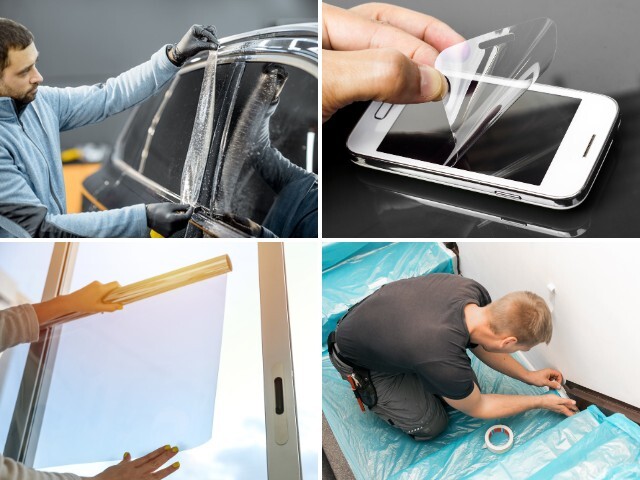
Manufacturing specialty films for diverse applications demands a deep understanding of pressure sensitive adhesives (PSAs). Delve into the crucial factors influencing performance, processability, and sustainability of your specialty film applications, and learn how PSA technologies impact your end-use product.
When manufacturing specialty films for applications including carpets, electronics, paint protection or windows, it’s important for your film to address key market demands, such as:
- Performance levels
- Processability
- End-use sustainability
However, in order to address these demands, you need to know certain attributes about pressure sensitive adhesives (PSAs) and what they mean for your finished film. Learn how PSA technologies vary from one another and how your chosen solution can impact end-use performance, processability and sustainability.
#1: PSA Performance Levels
To help meet the necessary performance levels your specialty film application requires, you need a PSA that can maintain performance depending on:
- Surface substrate plastic including (PE, PP, PET, PVC) vinyl, polyimide, acetate, metal, TPU and paper
- Environmental conditions such as chemicals, temperature changes, UV and moisture
However, because PSAs offer different performance levels, it can be challenging to determine the right PSA technology. Consider these three performance level elements to help in selection.
PSA Lifespan
PSAs provide both short and long-term durability so that your specialty film can perform for the duration of the end-use product’s lifespan. While all PSAs regardless of durability level can provide UV, moisture and chemical resistance, it’s good to know what is needed specifically for:
Short-term applications, such as indoor graphics (2-3 year film lifespan)
Choose a PSA that offers:
- Low peel to minimize damage in removing film
- Ease of installation to reduce errors, especially for large or intricate graphics
Waterborne acrylic and hot melt acrylic PSAs can offer these capabilities. Waterborne acrylic PSAs incorporate softening agents and tackifying resins that provide the flexibility needed for quick, clean removal. Hot melt acrylic PSAs can be formulated with lower molecular weight polymers that also contribute to increased flexibility to remove easily.
Long-term applications, such as paint protective or window films (5-7 year film lifespan)
Choose a PSA that offers:
- Cohesive strength to provide cold flow prevention to avoid film distortion from temperature changes over time
- Shrink and plasticizer resistance to enhance film’s overall appearance over time
Specialty solution acrylic and UV acrylic PSAs can offer these capabilities. Specialty solution acrylic PSAs form a strong bond that resists aging from chemicals, UV or temperatures; UV acrylic PSAs form strong crosslinked bonds to protect against the same factors.
PSA Removability and Repositioning Levels
For short-term applications, such as carpet, electronics as well as appliance masking, consider a PSA that allows you to both cleanly remove and reposition the film while offering a high bond strength across different surface types without damaging the overall appearance upon removal. Specifically, the following PSA technologies work well for these needs:
- Hot melt PSAs have adjustable tack levels to help enhance performance for your specific application requirements. They can also adhere to difficult substrates in cold and humid conditions while still being easy to remove and reposition.
- Waterborne acrylic PSAs provide both low and high peel levels, allowing you to choose the peel strength needed to protect your product while still ensuring the film will remove cleanly without residue and be repositionable.
For long-term applications, such as paint protection or solar window films, you may need to be able to cleanly remove the film, which you can; however, you cannot reposition it regardless of technology. PSAs for these applications are usually designed to provide long-term durability and maintain performance when exposed to environmental elements such as moisture or chemicals. As mentioned above, cold flow protection features can be formulated into permanent PSA solutions, too. Consider the following PSA technologies for long-term applications:
- Specialty solution acrylic PSAs are designed to offer high solids content with durable bond strength for an extended product life.
- UV acrylic PSAs are formulated to provide similar durability to specialty solution, but they are comprised of 100% solids to reduce overall solvents.
PSA Aesthetics
With specific applications that require clear bonding such as paint protection and electronics films, it can be especially difficult to choose the right PSA technology that ensures optical clarity. These complexities with aesthetics can increase when you must ensure your PSA technology provides both clear bonding and prevents yellowing or aging in applications such as window films. This is why it’s important to understand how different PSA technologies may or may not provide the right level of aesthetic appeal:
- Acrylic PSA technology is formulated to prevent cold flow interaction with film material that would otherwise cause the film to age or turn yellow over time. Specialty solution, UV and waterborne acrylic technologies are all designed to provide optically clear bonding, making them suitable for water-based coatings and varnishes, window and paint protective films that must maintain a clean appearance.
- Hot melt PSA technology is formulated in both transparent and colored formations; however, even transparent formulations can have a slight color or haze, which may not help you meet the necessary levels of optical clarity for your application. If clear bonding is not a concern in your application’s performance requirements, hot melt PSA technology’s ability to adhere to difficult substrates may be the right solution.
#2: PSA Processability
While you likely know your chosen PSA needs to be compatible with your equipment, you may not know your selection should also take into consideration whether or not your equipment is compatible with solvents.
Coating Equipment That Can Handle Solvents
If your equipment is compatible for solvents, you likely are already using a solvent-based PSA. However, solvent-based PSAs may require extended downtime due to burning off solvents, which also requires more supply yield to make up for the material that is burned off. You may also be experiencing increased production costs since solvent-based equipment requires drying ovens, thermal oxidizers and ventilation systems.
While solvent-based PSAs provide extended durability for long-term, permanent film applications, these processing requirements might make you consider whether another PSA technology, such as UV acrylic, can provide an improved ease of processing.
Coating Equipment That Does Not Handle Solvents
Hot melt, waterborne acrylic and UV acrylic PSA technologies are applicable options for equipment that cannot handle solvents. If you are producing films that are for short-term, indoor or removable and repositionable applications, solventless machinery may be all you need.
- Waterborne acrylic PSAs offer high processing speeds in addition to being solventless. You do not have to worry about thermal oxidizer capacity or take additional steps to burn off solvents, which can be beneficial for both large or small production output. Due to low coating temperature, the water evaporation process for waterborne acrylic PSAs is much shorter than the time required for a high-temperature curing process, helping complete production at an increased rate. Waterborne acrylic PSAs can also be formulated for a range of viscosities, allowing you to rely on one technology for wide application use and reduce changeouts.
- Hot melt PSAs are comprised of 100% solids, helping to enhance safety in your facility while increasing process speeds. Hot melt PSAs have fast setup times and melt upon heat activation, allowing for reusability if necessary.
Since UV acrylic PSA technology can provide similar durability levels to solvent-based PSA technology, it may be a suitable, solventless solution for an application that will have a long-term lifespan.
How UV Acrylic PSAs Provide an Alternative PSA Option to Use on Equipment That Can and Cannot Handle Solvents
UV acrylic PSAs are worth considering as an alternative when selecting PSAs, because they provide similar durability strength as solvent-based PSAs but are comprised of 100% solids like hot melt PSAs, reducing overall environmental impact.
Because UV acrylics and solvent-based are based on the same chemistry, you can change PSAs and still use the same equipment line with minimal investment. The same goes for UV acrylic PSAs and hot melt PSAs; even though they’re based on different chemistries, they require similar equipment since they are both comprised of 100% solids. With UV acrylic PSAs, you can:
- Refine yield supply: With no solvents to burn off, you’ll get more use out of a single yield and improve cost supply in the long run.
- Increase speed-to-market: UV acrylic PSAs offer fast production speeds, even with thick coat weights, because there is no need to complete multiple passes or wait for evaporation to occur. This helps you deliver products at a faster rate than with solvent equipment.
- Improve long-term oxidative stability: UV acrylic PSA technology does not contain rubber polymers like hot melt PSAs and therefore do not pose rheological limitations in formulated styrene block copolymer adhesives. This ensures your end-use film will not become brittle and lose adhesion after going through UV lights for curing.
- Enhanced facility usage: UV acrylic PSAs do not require drying ovens, thermal oxidizers and ventilation systems, enabling more facility space for cost effectiveness, along with reduced health risks for workers.
If you currently have equipment that can handle solvents and want to switch to UV acrylic to reduce solvent use, you’ll need to invest in a hot melt coating light with UV lights. This machinery will provide the coating capabilities needed for UV acrylic PSAs, and the UV lights will help cure them. It’s important with this upfront investment to note that hot melt PSA coaters are less expensive than solvent-coating equipment in the long run. Without accounting for burning off solvents, you can reduce your overall energy usage by approximately 85%**, reducing your monthly energy expenses. You’ll also be able to run coat weights five times faster or more depending on the adhesive deposition and number of UV lights**.
If you are currently using equipment that cannot handle solvents and considering switching to UV acrylic PSAs to expand your versatility and durability offering, you only need to incorporate UV lights with a drum unloader, buffer tank, feed lines and (if desired) slot-die coating head. You can continue to run rubber-based hot melt PSAs on your coating line as well as long as you keep these items in mind.
#3: PSA End-Use Application Sustainability
End-use applications, such as vehicles or windows, include multiple components that can impact overall sustainability levels. As one part of the application, it’s important that your PSA technology follows necessary guidelines to help allow the product to achieve sustainable goals. This will further prove to brand owners that you are serious about helping them supply products that aid in reducing environmental footprint.
How to Determine the Right Sustainability Features for Your Film
Before choosing your PSA technology, it’s important to outline your specific film sustainability goals. Sustainability can mean different things for different end-use applications, so understanding what’s most important to accomplish in reducing your environmental footprint can guide you to a suitable PSA solution.
- Reduced energy consumption: If you want to reduce your overall energy usage, then hot melt, waterborne acrylic, specialty solution acrylic and UV acrylic PSAs can all contribute in various ways. By not utilizing solvents, hot melt, UV acrylic and waterborne acrylic PSAs reduce processing steps that would otherwise require more energy to complete manufacturing. As previously mentioned, specialty solution acrylic PSA technology also reduces the time required to dry off solvents due to its high solids content, helping reduce energy usage as well.
- Decreased carbon emissions: When looking for ways to reduce your carbon footprint, hot melt PSAs can minimize fossil fuels, because they are compatible with bio-based raw materials, allowing you to incorporate renewable bio-mass into formulations.
- Reduced material replacement needs: By providing the necessary durability for long-term or permanent specialty films, specialty solution acrylic and UV acrylic PSAs help extend the overall product life, reducing material replacement frequency compared to other technologies.
- Enhanced safety: Both facility and worker protection can improve by using PSA technologies that are solventless or made of 100% solids, because you’ll reduce VOCs in your formulations. Further, you’ll reduce the risk for fires since additional precautions for storing and shipping that are required for solvents will not be needed.
Bostik’s Recommended PSA Technologies for Specialty Films
As the adhesives solutions segment of Arkema, Bostik offers the most complete and integrated portfolio of PSA offerings on the market. Our range of PSA technologies allows you to choose an option that is compatible with equipment you already own, saving you costs and downtime while also achieving high performance and sustainability improvements. Our product families for specialty film PSAs include:
- Aroset® acrylic emulsion PSAs are formulated for the most stringent requirements on film, vinyl and paper substrates to ensure you achieve the desired levels of durability needed.
- Encor® waterborne acrylic PSAs provide coater-ready solutions for both permanent and removable specialty films, helping you address environmental concerns and aesthetics.
- Flexcryl® acrylic emulsion solutions offer stringent performance to specialty films, including clear film labels that require increased durability while also providing clean removability.
Along with our solutions, you’ll have access to our technical support experts who can provide recommendations on customized formulations and processing techniques to ensure your manufacturing runs smoothly.
Are you ready to make a decision on the PSA technology most suitable for your specialty film applications? Contact a Bostik expert to learn how we can ensure your choice is providing high performance with production efficiencies and improved sustainability.
**based on internal testing
©2023 Bostik, Inc. All Rights Reserved
All information contained herein is believed to be accurate as of the date of publication, is provided “as-is” and is subject to change without notice. To review our full U.S. Legal Disclaimer, visit: https://bostik.com/us/en_US/privacy-policy/legal-disclaimer
See also
Back to all articles- Advanced Packaging
3 Essential Performance Capabilities for Tape Adhesives in Evolving Construction Applications
- Advanced Packaging
How Formulation and Coating Method Impact UV HMPSAs
- Advanced Packaging