Apr 20, 2023 - 3-5 minutes
How Your Wash-Off Labels May Not be as Good as You Think
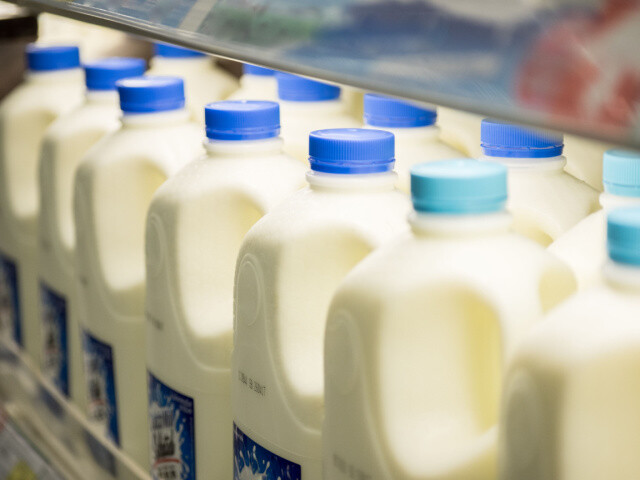
Learn why traditional general-purpose acrylic adhesives can fall short in performance, processing and sustainability. Find out how Association of Plastic Recyclers (APR) approved wash-off label adhesives enable you to manufacture more sustainable wash-off labels with high performance and production efficiencies.
As a label converter, you want to manufacture labels that meet end-use performance criteria and address sustainability needs. Therefore, you may have turned to using wash-off labels, especially given their ability to adhere to increasingly popular PET packaging materials, which enhance design options and support sustainability initiatives. However, your wash-off labels are likely manufactured using traditional, general purpose acrylic adhesives. These adhesives impact your ability to label all PET applications, decrease your production efficiencies and increase your energy usage. In short, wash-off labels using these adhesives may not be as good as you think. Gain insight into why that is the case and how an Association of Plastic Recyclers (APR)-approved adhesive innovation enables you to manufacture sustainable wash-off labels, increasing revenue potential and reducing costs overall.
1. Traditional Acrylic Wash-Off Label Adhesives Impact Ability to Label Applications at Low Temperatures
Traditional acrylic wash-off label adhesives are designed to be applied in 40*F+ conditions. If the temperature is lower than that, the adhesives may have difficulty adhering. In addition to making the application process more constrained, this limits your ability to meet brand owner needs with sustainable labels for all of their PET packaging label applications.
For example, by using traditional acrylic adhesives, you cannot manufacture wash-off labels for any freezer grade or cold-filling product packaging applications. As a result, brand owners are unable to meet sustainability goals for packaged products in those categories. While their product may be in a sustainable packaging format, such as PET, they’ll need to use non-wash-off labels that can be applied in temperatures less than 40*F. These non-wash-off labels will then cause contamination and reduce the amount of PET that can be yielded from the recycling stream.
For example, by using traditional acrylic adhesives, you cannot manufacture wash-off labels for any freezer grade or cold-filling product packaging applications. As a result, brand owners are unable to meet sustainability goals for packaged products in those categories. While their product may be in a sustainable packaging format, such as PET, they’ll need to use non-wash-off labels that can be applied in temperatures less than 40*F. These non-wash-off labels will then cause contamination and reduce the amount of PET that can be yielded from the recycling stream.
2. Traditional Acrylic Wash-Off Label Adhesives Decrease Production Efficiencies
Additionally, you, like many converters manufacturing wash-off labels, may be formulating the adhesives independently due to limited supplier availability; this is because the market lacks a fully-formulated product. This can require significant time and resources to develop, especially given that it means you must conduct critical APR guidance testing on your own accord and ensure the labels aren’t adversely affecting sustainability levels. While you may be able to successfully do this, it likely makes it more challenging for you to focus on other label manufacturing needs and slows down your production efficiencies. As a result, your plant is unable to run as effectively as it should be, which can contribute to added costs and environmental impact.
3. How Traditional Acrylic Wash-Off Label Adhesives Increase Energy Usage
Further, traditional acrylic wash-off label adhesives require pre-treatment in order to adhere to commonly-used, biaxially-oriented polypropylene (BOPP) label facestock. This is because they lack sufficient surface energy on their own accord, and pre-treatment increases their surface energy. Without pre-treatment, the adhesives would cause the labels to gravitate toward the PET instead of the BOPP. In doing so, the labels would remain on the PET during the recycling process, negatively harming it. While this pre-treatment is regarded as the norm in order to be able to use wash-off labels and reduce environmental impact, it actually increases energy usage at the production level and adds to complexity. This added usage translates to a greater carbon footprint, hindering you from fully achieving sustainability goals and efficient processes.
How an Alternative Acrylic Wash-Off Label Adhesive Overcomes These Issues
Bostik’s Flexcryl™ ClearCycle 1000 is a water-based, all-temperature, acrylic wash-off label adhesive. It has APR approval recognition for meeting PET-CG-02 critical guidance criteria, which means that it yields minimal impact on color even after the PET has been cycled through the recycling process twice. It also offers the following advantages:
Ready to see the wash-off label difference with ClearCycle 1000? Contact a Bostik expert today!
Contact an Expert
Unmatched Application Capabilities
ClearCycle 1000 is the only wash-off label adhesive on the market to offer all-temperature application performance. This means that unlike traditional wash-off acrylic adhesives, it can adhere in temperatures lower than 40*F and works well on freezer grade and cold-filling product packaging, such as PET trays. In addition to helping brand owners use more sustainable labels for those applications, it allows you to expand your wash-off label revenue.Increased Production Efficiencies
ClearCycle 1000 also makes it much easier for converters to manufacture wash-off labels compared to traditional acrylic adhesives. As a fully-formulated adhesive option, it eliminates the need to formulate yourself and ensures the adhesive will pass the testing process if used with the recommended conditions. This saves you time and resources, enabling you to address other label production needs in addition to decreasing costs overall.Decreased Energy Usage
Additionally, ClearCycle 1000 does not require the substrate to receive surface treatment. It offers intrinsically sufficient surface energy levels as-is; it easily adheres directly to the BOPP facestock without any treatment needed, such as corona treatment. In addition to reducing energy usage, this allows it to simplify production steps and reduce error likelihood, further saving you time and expenses.Ready to see the wash-off label difference with ClearCycle 1000? Contact a Bostik expert today!
Contact an Expert
©2023 Bostik, Inc. All Rights Reserved
All information contained herein is believed to be accurate as of the date of publication, is provided “as-is” and is subject to change without notice. To review our full U.S. Legal Disclaimer, visit: https://bostik.com/us/en_US/privacy-policy/legal-disclaimer
All information contained herein is believed to be accurate as of the date of publication, is provided “as-is” and is subject to change without notice. To review our full U.S. Legal Disclaimer, visit: https://bostik.com/us/en_US/privacy-policy/legal-disclaimer