Jul 19, 2024 - 3-5 minutes
Increase Processing Speeds for Smart Card Applications
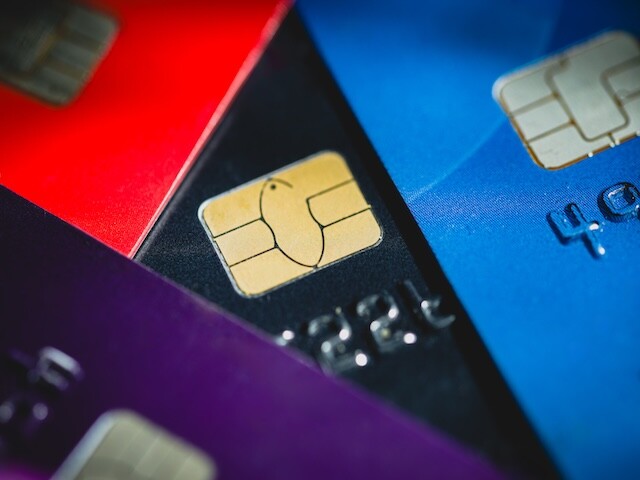
Learn why UV epoxy adhesives offer improvements over traditional epoxies for microchip components to achieve high-speed processing and reduce costs.
When manufacturing smart card microchip components such as dam & fill and glob top encapsulation, it’s important to achieve precise structural bonding while maintaining production efficiencies and keeping costs to a minimum.
While traditional epoxy adhesives historically have been used in these applications, they tend to lack the capabilities to provide high-speed processing methods and can hinder efficiencies.
However, an alternative solution is changing that.
Learn why UV epoxy adhesives offer improvements over traditional epoxies for microchip components, helping manufacturers achieve efficient, high-speed processing and reduce overall costs.
Traditional Epoxy Limitation #1: Cure Requirements
Traditional epoxy adhesives require ovens or other heating equipment for curing; not only does this involve increased energy usage and costs, but it may require various thermal management curing stages. Depending on the formulation and necessary temperature application, this curing process can take minutes to hours to complete as it involves a chemical reaction between a resin and a hardener. This chemical reaction can create complexities in maintaining consistent temperature control if multiple productions are taking place at once, which can make it hard to ensure reliable bonding performance in the end-use application.
How UV Epoxy Adhesives Overcome This Limitation
UV epoxy adhesives cure through a photopolymerization process with UV light exposure, which helps to bond sensitive microchip components that could be compromised by heat due to inconsistencies in thermal management curing stages. Compared to other epoxy adhesives, they offer:
- Faster curing times: Rather than waiting minutes to hours with heat curing processes, UV curing times often only take seconds to complete, as the high energy from the UV light quickly triggers necessary chemical reactions to allow for fast adhesion. This allows for more products to be processed in the same or even less time compared to epoxy adhesives.
- Reduced heat usage: UV curing is usually completed at room temperature, eliminating the need for ovens or other heating equipment. This can help speed up production times as well as reduce energy consumption and overall costs.
- Higher throughput: UV curing for UV epoxy adhesives can be incorporated into automated assembly, which tends to be difficult with epoxy adhesives that need to endure various thermal management curing stages.
- Increased end-use performance: UV epoxy adhesives are designed to be thermally stable and resistant to high temperatures after curing; this is crucial for microchips components as they may be exposed to various thermal cycles during their use.
Traditional Epoxy Limitation #2: Dispensing Requirements
Traditional epoxy adhesives offer a range of viscosities; however, those ranges can change over time. This is because they are thixotropic, which means the viscosity can decrease during mixing or application and increase when at rest. While this helps keep the adhesive in place, it can create complexities in the dispensing process if there are inconsistencies in the rheological properties. For example, if the viscosity level is high, the epoxy may require additional equipment to dispense or apply evenly; if it’s low, the epoxy may spread too much causing uneven coverage. These inconsistencies could result in added production time and costs to correct any issues.
How UV Epoxy Adhesives Overcome This Limitation
UV epoxy adhesives are formulated with specific viscosity and thixotropic properties to address delicate materials, including dam & fill and glob top encapsulation applications in smart cards. In particular, the viscosity level is designed to flow consistently and wet surfaces evenly to avoid blistering; in combination with thixotropic properties, this rheology helps ensure the adhesives do not spread beyond the area they need to cover and instead provide a consistent coverage.
Additionally, UV epoxy adhesives are a one-component system, helping to reduce complexities with optimized dispensing because they do not require any mixing. Packaged with a wide-open cylindrical bottle, UV epoxy adhesives help control the adhesive placement on to the microchip components so the amount used is kept to a minimum while still providing stable adhesion. Overall, with rheological properties specifically formulated for microchip components in smart cards, UV epoxies can achieve precise adhesive dispensing for reliable, consistent bonding.
Why Choose Bostik’s UV Epoxies for Smart Card Microchip Components
As the adhesives solution segment of Arkema, Bostik helps you address numerous microchip application needs for smart cards, including dam & fill and glob top encapsulation.
Our Born2Bond UV epoxy adhesives provide high-precision cationic epoxy solutions that cure on exposure to UV light. This allows you to cure dam & fill and glob top encapsulation applications without risk of compromising end-use performance from high temperatures. With UV curing processes, these adhesives speed up your production while reducing energy consumption to improve your environmental footprint and overall costs.
Additionally, through our acquisition with Polytec PT, Bostik also offers chip antenna solutions for solder joint replacement using electrically conductive epoxy paste.
Our team of experts will guide you step by step to provide customized formulations, helping to ensure our products work effectively with your end-use applications while also giving you a full understanding of how to utilize the UV curing process in your manufacturing.
Are you ready to increase your processing speeds for microchip components in smart cards? Contact a Bostik expert to learn how we can help you improve your production while maintaining high performance for sensitive electronic applications.
Other relevant content: