Two-component Polyurethane Adhesives
Bostik is a global leader in two-component Polyurethane adhesives, often called 2KPU or 2KPUR. Two-component polyurethanes are well-known for their excellent adhesion, high mechanical properties, and good chemical resistance.
Find out what two-component polyurethane adhesives are and how this technology can serve various industrial markets such as building and construction, general transportation, flexible packaging, and assembly.
What are two-component Polyurethane Adhesives?
Polyurethanes (PURs) were invented in the 1930s and have found multiple industrial applications. Polyurethane has been used in adhesives since the 1950s. They are classified as one- or two-component polyurethane adhesives, and each category contains several different types of adhesives.
Two-component polyurethane adhesives include polyols and poly-isocyanates or urethane prepolymers mixed just before application. The two components are the resin and the hardener, which contain isocyanate functions. Ratios of component A (resin) and component B (hardener) can vary. The proper mix ratio and complete mixing are vital to reaching suitable properties for a specific application through a chemical reaction. Compared to 1KPU, 2KPU are able to cure more quickly and are not dependent on moisture or heat to cure.
What are the advantages of 2-component polyurethane adhesives?
When considering an adhesive technology, it’s important to know the advantages two-component polyurethane adhesives bring to manufacturing processes:
- Strong bonding to heighten durability.
- Better chemical resistance compared to one-component polyurethane adhesive.
- Automatic dispensing capabilities and quick cure speed to improve production efficiencies.
- Ability to cure quickly and in a definite time for an application adapted to your lean manufacturing needs.
- High versatility and optimization of mechanical properties for enhanced performance.
- Multi-substrates adhesion to increase design options for highly versatile design and applications.
- Environmental compatibility with recyclable or partially bio-based adhesives.
What are Bostik's innovations about 2-component Polyurethanes Adhesives?
Our extensive technology portfolio includes the following sustainable innovations:
- Improved Recyclability Levels
We develop adhesives that promote the recyclability of packaging. For example, our innovative SF10M (A+B), dedicated to mono-material PE packaging and has Recyclass approval.
- Reduced Harmful Substances
HERBERTS LF 225 / HARDENER 300M is a general performance solvent free two-component polyurethane-cross-linking adhesive system which can be processed at 45~50°C.
FEATURED PRODUCT: HERBERTS LF 225 / HARDENER 300M
PURBINDER MP830 / MP730 is a general performance solvent free two-component polyurethane-cross-linking adhesive system which can be processed at 40°C.
FEATURED PRODUCT: PURBINDER MP830 / MP730
HERBERTS LF475 / HARDENER 297 is a general to medium performance solvent free two-component polyurethane-cross-linking adhesive system, which can be processed at 40~45°C.
For which applications two-component Polyurethane Adhesives are designed?
Flexible Packaging
PU2K is commonly used in flexible packaging. For this application, very fluid products must be laminated to film rollers. They are applied in thin layers in minimal quantities and are heated to increase their viscosity. Mixing ratios are often offset for flexible packaging applications.
Herberts 2K-LF 520 with Hardener 107 is a two-component, solvent-free adhesive used in the flexible packaging market. It is designed for medium-performance applications with high bond on aluminium foil and metallised films.
Building & Construction
We also use PU2K for panels in buildings Materials. There are many formulations of polyurethane foam to optimize the density for insulation, structural sandwich panels, or architectural components. In building materials, PU2K is appreciated for its low viscosity, no solvent, and fire-retardant properties.
Marocol 61132A is a 2-component polyurethane adhesive without solvent, specially designed to bond the different constitutive substrates of sandwich panels.
General Transportation
PU2K is widely used in general transportation and is generally mixed with a static mixer in a ratio of 1:1 (as many -OH functions as -NCO). 2KPU is often used in sandwich panels as well as mounting adhesive. In marine, they are used for the deck to hull bonding. They are appreciated for their very well-defined reactivity and their very high mechanical properties.
Marocol 18576A + Hardener 4300B is a two-component, polyurethane adhesive without solvents used as an adhesive in sandwich panel production and to assemble panels in the caravan and trailer industry.
Automotive
The main attractive features of two-component polyurethane adhesives for automotive are that they give the assembly high resistance to impacts and vibrations. They are also a great solution to bond dissimilar substrates and assemble various materials, notably metals, glass, and many thermoplastic materials and composites.
Bostik XPU 18512 AM/B is a 2-component polyurethane based, solvent-free highly elastic adhesive for the automotive industry.
Assembly
Polyurethane bi-component adhesives are mainly used for liquefied natural gas tankers. These adhesives are used for insulation layers. Their outstanding versatility and easy adjustment of mechanical properties make them ideal for this application. They are resistant to cryogenic temperatures of -170°C.
XPU 18045 An/B is a flexible two component polyurethane adhesive which can cure at ambient temperature or with heating. It is particularly adapted as solution regarding technical requirements of structural bonding supporting cryogenic conditions.
Frequently Asked Questions about two-component Polyurethane Adhesives
Why use PU3K instead of PU2K in sandwich panels?
PU3K consists of 3-components with different reactivity: 2 components A (two resins with different reactivities), and one component B (hardener). An automatic system ensures ideal proportions when mixing these three components, so the reactivity of the adhesive can be regulated. PU3K is widely used for sandwich panels. It solves problems of open time control, which PU2K cannot solve. Indeed, the issue of PU2K for buildings is the dependence on panel temperature, shed temperature, humidity, etc.
PU3K adhesive is ideal for complex panels, which require multiple layers. As the layers are added, the reactivity of the adhesive can be modified. For example, you can start with the slow formula and enrich your mix with the fast formula over time. This process give you enough time to apply all the layers, guarantees a homogeneous and simultaneous crosslinking at pressing, and prevents the adhesive from crosslinking before the panel is pressed.
What are the differences in terms of applications of solvent-based 2KPU compared to solvent-free 2KPU in flexible lamination?
- For the PU2K solvent range, we use an engraved cylinder to apply the adhesive on the first substrate. This cylinder rotates in a solvent glue bath at room temperature. The filling of the engravings is done by capillarity. Then it is heated in an oven to evaporate the solvent before laminating the second substrate.
- For the PU2K solvent-free range, the adhesive is heated (from 40°C to 60°C) and applied between two rubber rollers. The adhesive is applied by transfer on the first substrate, the second substrate is applied directly (no oven required).
What are the advantages of 2-component polyurethane adhesive compared to epoxy for Liquefied Natural Gas (LNG)?
PU2Ks are less brittle than epoxy adhesives, have easily adjustable structures and mechanical properties, and have good resistance to very low temperatures.
Featured Products: Two-component Polyurethane Adhesives
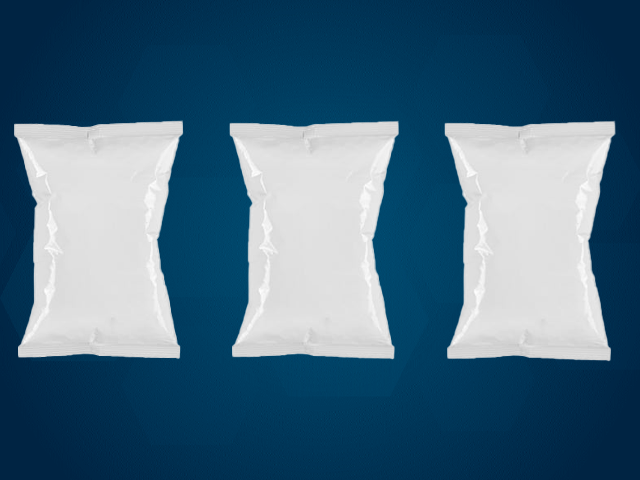
HERBERTS LF 225 / HARDENER 300M
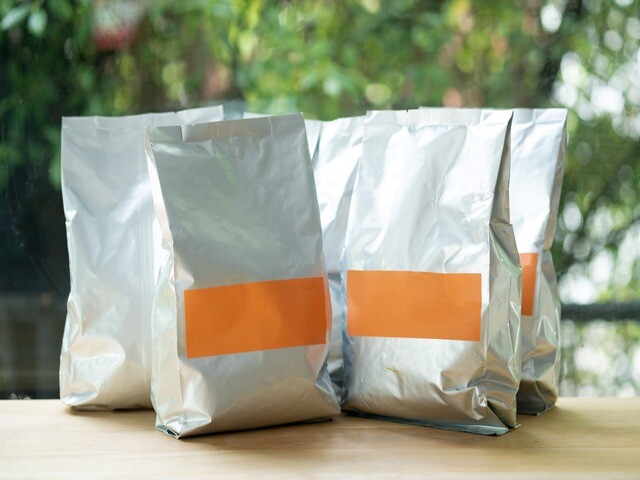
HERBERTS LF 475 / HARDENER 297
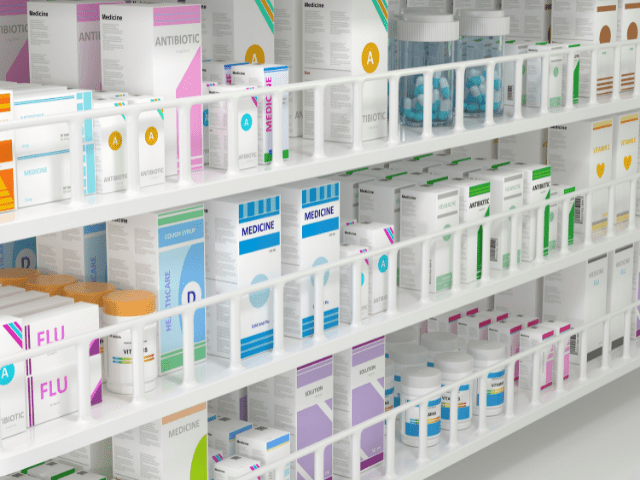
PURBINDER MP830 / MP730
SF10M A+B
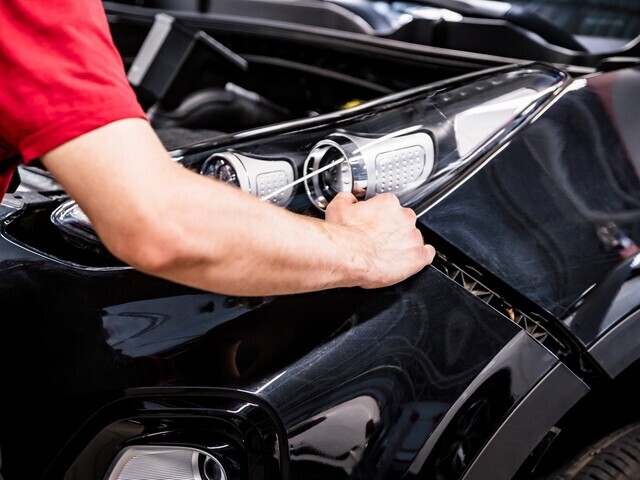
XPU 20102
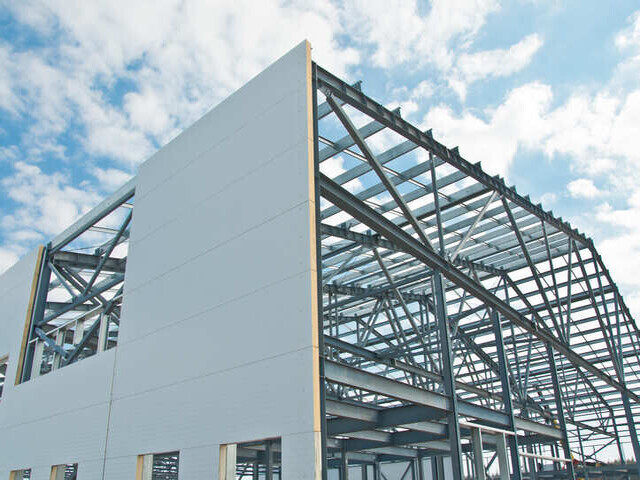
MAROCOL 61132A + Hardener 4600B
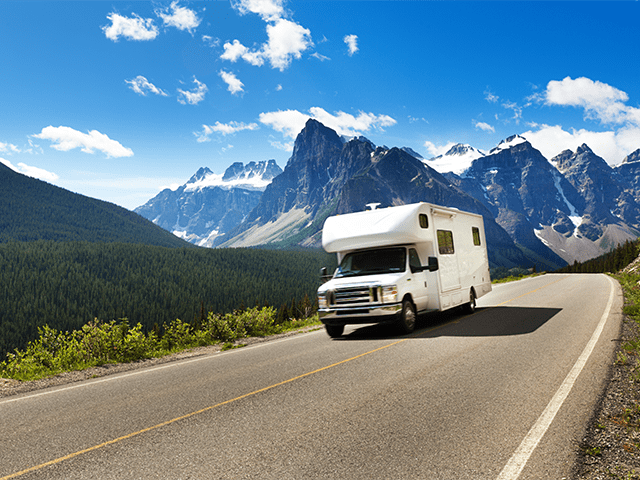
MAROCOL 18576A + HARDENER 4300B
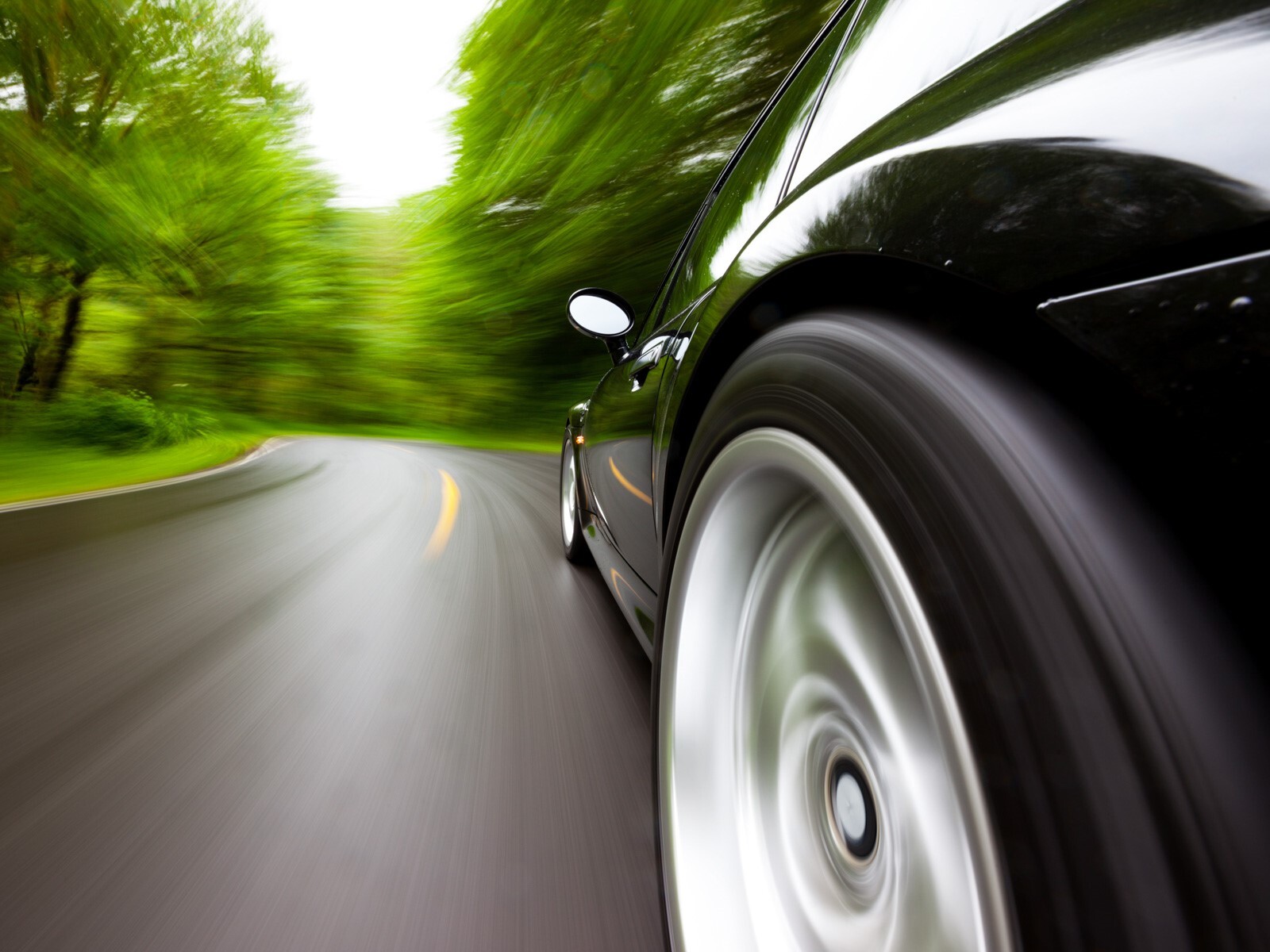
XPU 18512 AM/B
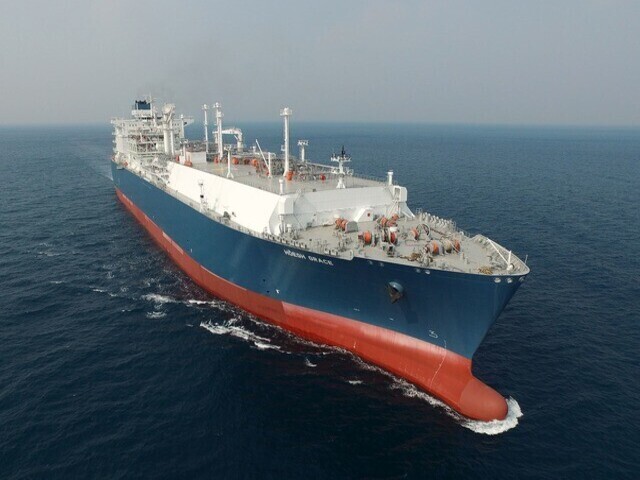
XPU 18045 An/B
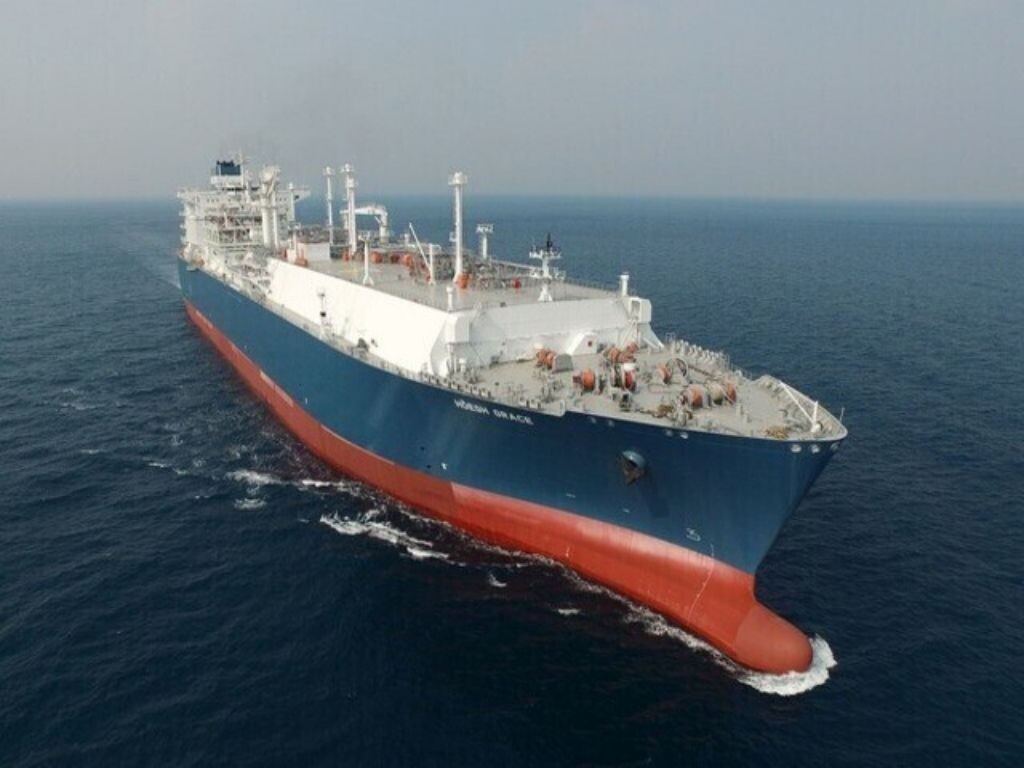