Jun 11, 2014 - 3-5 min
Running the Bostik Gauntlet: Rheological Modeling
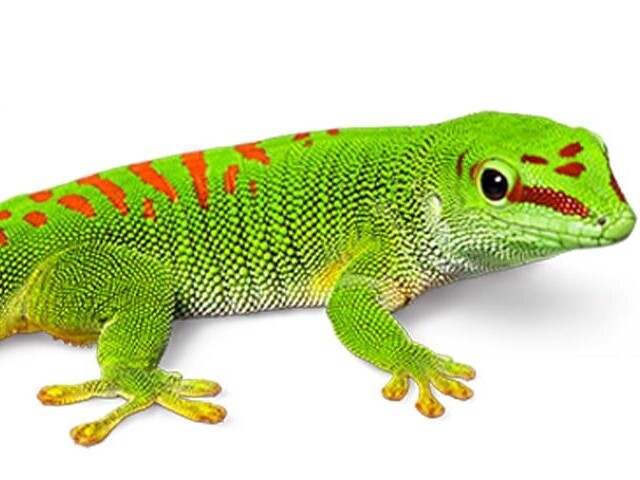
Customers want the best from the products they are buying, whether it is software, a car, food, or the adhesives we offer here at Bostik. Everything that people spend their money on is expected to be the best. As many companies are continually pushing out new versions of their materials, the testing phase of these companies is growing shorter than it should be. A product will be pushed out with glitches or bugs that will be corrected before the next release. This business model, though very commonly used, leaves a bad impression on the customer, which makes a bad impact on the quality impression of that company. The scorned customer will remember the bad quality of a product and seek their future products elsewhere.
This is why the testing phase of all Bostik products is so important to us. This stage in development of our adhesives is essential to creating the best versions of our products – to know exactly what our adhesives will be facing and how they will stand up to the world in general use. Many companies do go through the testing phase to ensure the ultimate versions of their materials exist. We at Bostik are no different, though our process is more than simple testing. We put all our adhesives through a rigorous run of rheological modeling.
Rheology is the science of matter and energy and their interactions with the forces around them. It is the study of the deformation and flow of that matter. Rheological modeling is a way for us at Bostik to observe an adhesive after breaking it completely down to its elemental parts and basic principles. We run our adhesives through a gauntlet of tests; we strain and stress them so that once that adhesive is out there in the field in the hands of our customers, we know exactly how it will react. We’ve used our modeling system to thoroughly prepare our products for anything that they will go through.
By using our rheological modeling process, we have been able to develop superior products with specific adhesion to very difficult objects varying from stone and masonry used in construction, ceramic and porcelain tiles, material used in the bottom of an aquariums, labeling on soda cans, and high speed rail systems. We have been able to use rheological modeling to understand exactly how our adhesives behave when they’re sprayed or applied. We already know how our products are going to perform after they have bonded to the materials they are applied to.
This intensive development stage using rheological modeling keeps all of Bostik adhesives the highest of caliber available.