Mar 14, 2017 - 10 min
TIPS FOR PROPER HANDLING OF TURBO-SEAL® COLD SEAL ADHESIVES
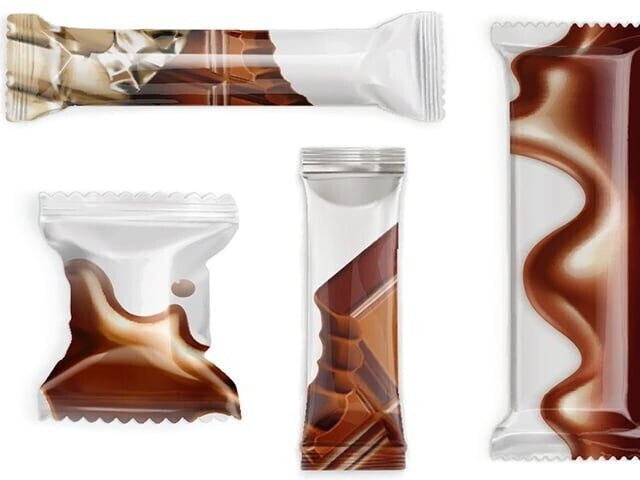
Bostik’s Turbo-Seal cold seal adhesive coatings offer high performance sealing for a variety of food and medical packaging applications. These coatings also provide customers with the following advantages:
- Improved operational efficiencies
- Increased profitability
To ensure proper handling of these adhesive coatings, please refer to the following tips:
Importance of Proper Mixing
- Vertically mount the mixer in the center of the container. Ensure that it rests 6 inches from the bottom of the container. It should take approximately 30 minutes to adequately mix in the cold seal.
- A small vortex is adequate (1-3 inches in depth and width). It is not necessary to have excessive agitation (a vortex greater than 5 inches), as it may cause foaming and formation of particle.
- For best results, maintain continuous agitation throughout the process.
- Take care to prevent foaming of the cohesive. As the level goes down in the container, it may be necessary to reduce speed.
Importance of Cleaning Up
Cold seal adhesive coatings are susceptible to bacteria growth over time, so make sure everything cold seals come into contact with is clean.
Some bacteria sources include:
- Dye cups
- Mixers
- Hoses
- Pans and sumps
Importance of Ammonia
Ammonia plays an important role in cold seal adhesives. It:
- Prevents bacteria from growing
- Aids in proper machining of the cold seal
Be sure to also cover the sump drum pan to prevent ammonia loss. Ammonia loss contributes to:
- Bacteria growth
- Lower pH
- Skinning
- Particle buildup
- Poor wiping
For more information on proper handling of cold seal adhesives, call 800-7-BOSTIK.