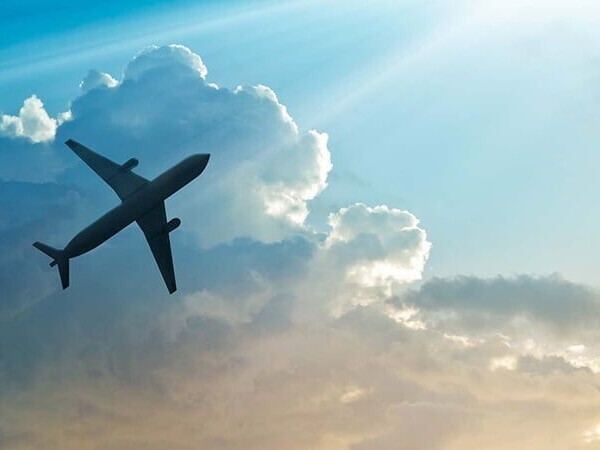
As you likely know, adhesives play a large role in aircraft interior manufacturing. Slated to be worth $1,008 million by 2023, they’re used in many applications, from decorative laminates to acoustic insulation, making aircraft more fuel efficient and safer for passengers. But do you know the types of aircraft interior adhesive technology, and which one is right for you?
SOLVENT-BORNE
While the market share for water-borne isn’t as large as solvent-borne, adhesives manufactured using this technology offer:
- Excellent shear strength
- Good appearance
- Superior adhesion, flexibility and durability
Additionally, water-borne adhesives are expected to experience increasing popularity as their properties continue to improve.
HOT MELT PRESSURE SENSITIVE
A unique class of bonding materials, hot melt pressure sensitive adhesive technology offers:
- Flame retardancy
- Lack of VOC emissions
- Varying degrees of tackiness
As a result, these aircraft interior adhesives are able to decrease set up times over other technologies. This, coupled with the fact that hot melt pressure sensitive adhesives exceed aerospace regulations, is why hot melt pressure sensitive technology is expected to grow rapidly until 2021.
—
Bostik manufactures smart aircraft interior adhesive solutions. In working directly with airplane manufacturers, we develop custom formulations that lower costs and improve manufacturing efficiencies. Additionally, we can manufacture adhesives with flame retardancy, enhancing airplane passenger safety.
For more information on our aircraft interior adhesive options and which ones are right for you, contact a Bostik representative today. You can also view this other relevant content: