Jan 11, 2018 - 10 min
COMMON COLD SEAL ADHESIVE PROBLEMS: PART II
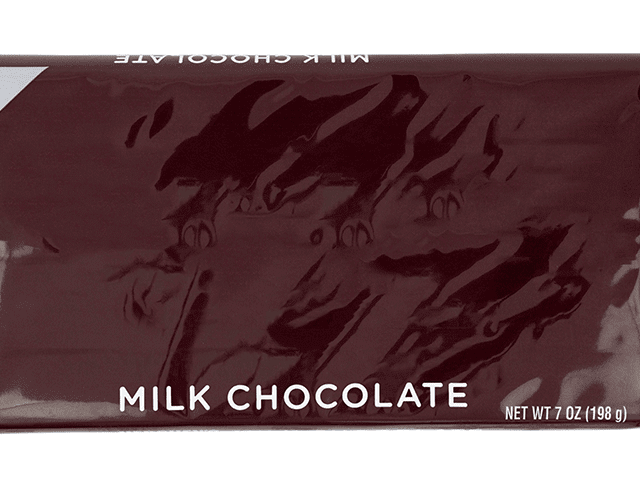
In a recent blog post, we looked at three common cold seal adhesive problems and their causes. Now, take a look at other likely issues and how to address them in part two.
Phasing
Also referred to as separation, phasing is when the polymer and latex within the adhesive move during storage. This causes an increase in latex at the top of the container and an increase of the polymer at its bottom.
In addition to being accelerated by improper storage conditions, using an older cold seal adhesive can also cause phasing.
Foaming
Foaming is when air bubbles are trapped in the cold seal adhesive’s surface, which cause the adhesive to increase in volume. The following causes can trigger foaming:
- Use of a high shear cold seal pump
- A recirculation system that allows air into the cold seal
- Use of a low speed cold seal at too high of a speed
Oxidation
Oxidation, or degradation, results in loss of an adhesive seal’s internal stress. This is caused by:
- Copper contaminating the cold seal adhesive either during the printing process or in the finished reel
- Exposure to high temperatures or direct sunlight right after conversion
- Excessive conversion age
Addressing Common Cold Seal Adhesive Problems
Fortunately, phasing, foaming and oxidation are easily avoidable problems with preventive measures. For example, Bostik conducts thorough testing on the materials and production line prior to implementation to ensure our cold seal adhesive exceeds performance needs.
If you’re having any of these cold seal adhesive problems, contact us today.