Jan 8, 2019 - 10 min
Considerations to Make Prior to Choosing an Aerospace Adhesive
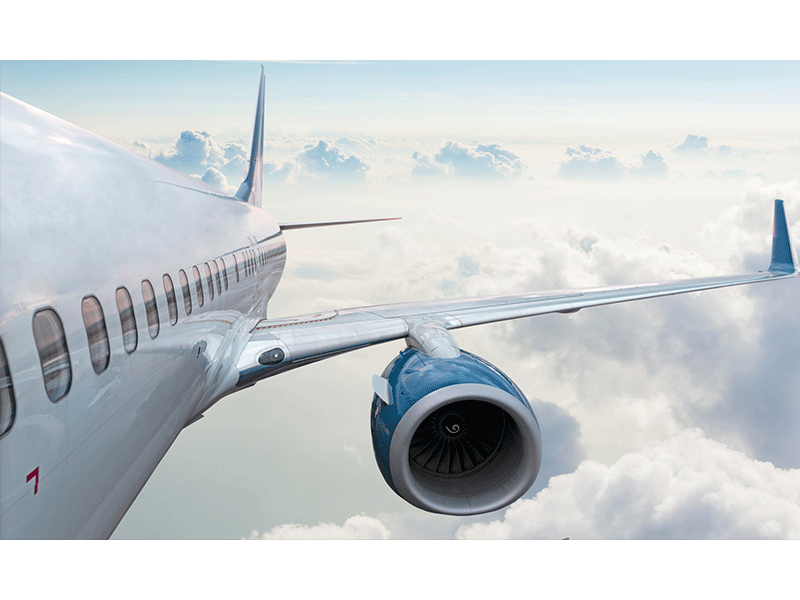
Aerospace adhesives serve an important function in aircraft assembly. In addition to providing a strong yet lightweight bond, they help enhance passenger safety and comfort. When selecting an adhesive for an aerospace application, it’s important to consider the following criteria:
Adhesive Technology
While the aircraft substrate may vary, common ones include:- Composites (such as carbon fiber)
- Plastics
- Metals (such as aluminum)
- Rubbers
Adhesive Chemical Resistance
It’s also important to consider an adhesive’s aviation chemical resistance levels. In particular, the adhesive must be able to withstand chemical types such as jet fuels and a myriad of oils. Additionally, manufacturers should determine how an adhesive performs under various chemical exposure duration and frequency levels. For example, the adhesive may be exposed to jet fuel consistently or intermittently based on the application. Either way, it’s important that the adhesive’s resistance to more than just chemical nature itself is tested.Adhesive Viscosity
An adhesive’s viscosity can impact its performance level for certain aerospace applications. Fully understanding the application will help determine if low or high viscosity is needed. For example, for narrow, gap filling applications, a low viscosity aerospace adhesive is likely to perform best. On the other hand, vertically positioned applications where restriction of flow is needed, consider a high viscosity product. -- Aerospace adhesives also must pass specific certifications prior to approval for aircraft application use. These include meeting certain low outgassing criteria and flame retardancy performance in particular. Designed to keep planes flying and passengers safe, aerospace adhesives are held to high standards. Therefore, many of today’s major companies are turning to Bostik for smart aerospace adhesives. Receiving various BMS approvals, Bostik's adhesives are designed for a range of aircraft interior applications, such as:- Decorative laminates
- Skin to core composites
- Seat cushions
- Interior panels