- Industrial
- Aerospace
- Assembly
- Automotive
- Flexible Packaging
- General Transportation
- Rigid Packaging
- Tape & Label
Dec 1, 2019 - 10 min
5 Tips for Hot Melt Drum Unloader Preventive Maintenance
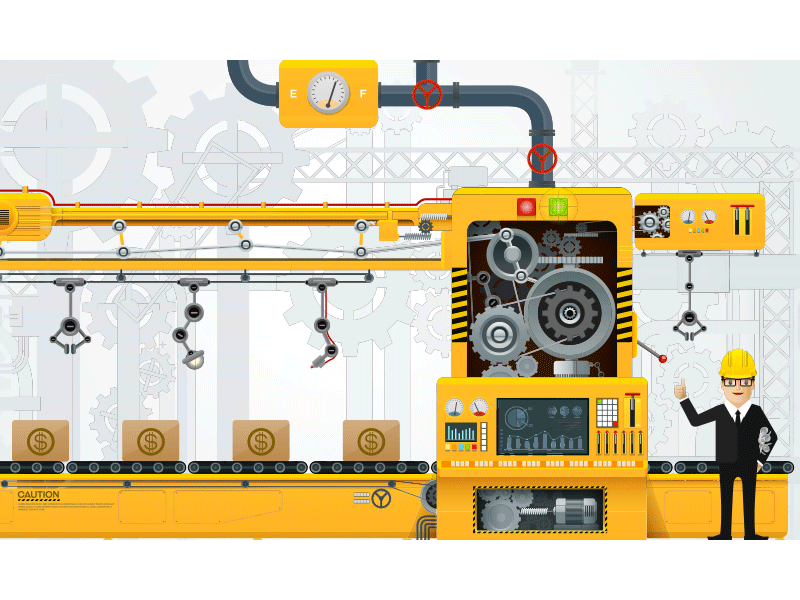
In a recent blog post, we discussed certain preventive maintenance tips for keeping hot melt adhesive tanks operating smoothly. Now, take a look at the following hot melt drum unloader tips to further enhance your operational efficiencies.