Apr 8, 2019 - 10 min
Avoid Flexible Packaging Film Production Problems
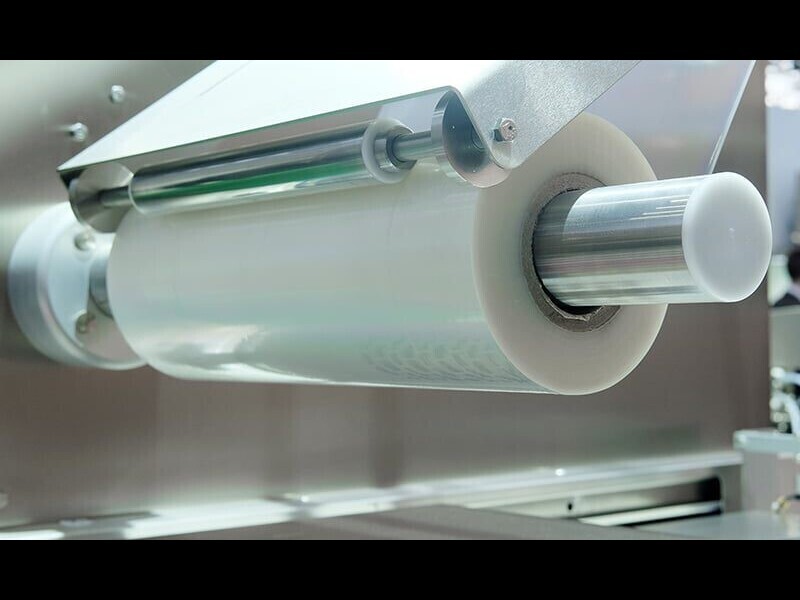
As consumers increasingly prefer healthy, on-the-go food options, demand for fresh, packaged products rises. To address these product preferences, brand owners have turned to packaging produce in trays with a film cover. However, many packaging films used in manufacturing these packages negatively impact converting processes. Find out why this is the case and how to avoid these flexible packaging film production problems.
Problem 1: Incompatible Materials
According to Freedonia, polypropylene (PP), low density polyethylene (LDPE) and linear low density polyethylene (LLDPE) are the most common film choices for all types of product packaging. However, these films are not compatible with amorphous polyester (APET), which is the go-to option for the packaging trays.
Due to this incompatibility, many converters use an additional adhesive tray coating to ensure the films will bond to the APET tray stock.
Yet even once they are successfully bonded to the tray stock, they still pose flexible packaging film production problems. This is because the dissimilarities between the adhesive, the film and the tray prevent easy consumer recycling.
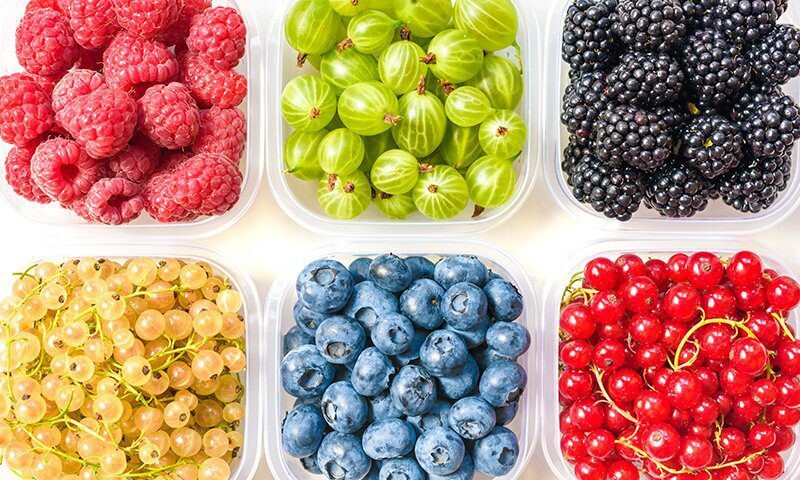
Problem 2: Poor Environmental Barriers
Additionally, these commonly-used packaging films possess poor environmental barriers for the packaged produce. In particular, these films have oxygen transmission rates greater then 1550 cc/m2/24 hours.
While oxygen may seem like an innocuous gas for fresh produce, these high transmission rates increase the foods oxidation levels. This results in reduced shelf life and decreased food quality.
To help mitigate barrier problems, some converters use multi-layer films. However, even though oxygen transmission rates may be reduced, proper recycling is disrupted or altogether prohibited as a result.
How to Avoid These Flexible Packaging Film Problems
While converters can ultimately use PP, LDPE and LLDPE films on APET trays, doing so increases manufacturing complexity, time and costs. Fortunately, a copolyester, anti-fog heat seal coating helps avoid these problems altogether, increasing operational efficiencies and decreasing costs.
Compatible with APET trays, this coating also makes recycling easy. Furthermore, converters don’t need additional films or extra processing steps to achieve both a sufficient heat seal and package clarity. This is because the coating contains both heat seal functionality and anti-fog capability in one product.
Also, as a PET-based product, it offers a significantly improved oxygen transmission barrier over other film options. This helps improve produce shelf life and extend food quality when compared to LDPE, HPDE and OPP especially.
To learn more about how this product improves your converting processes and end-use package performance overall, contact us today.
You can also view this relevant content: