Oct 30, 2020 - 10 min
Reduce Your Automotive Production Costs with Foam-In-Place Adhesives
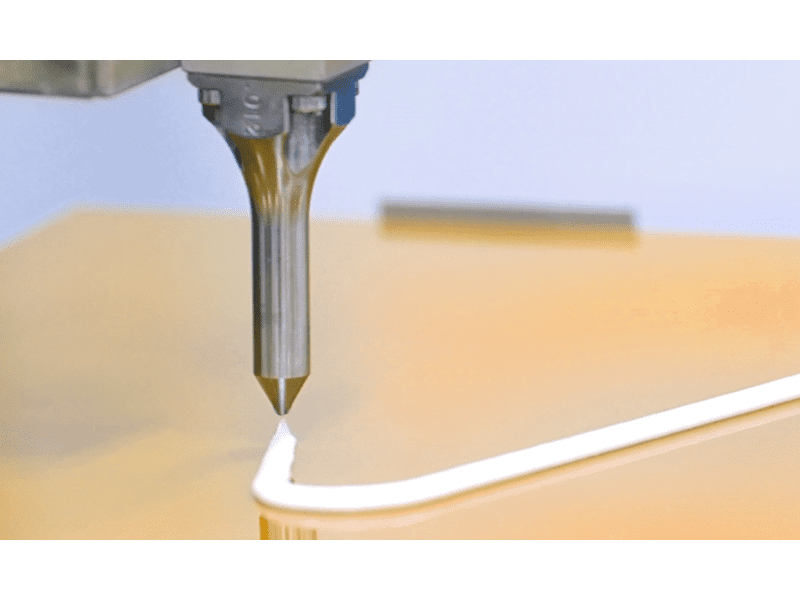
Automotive manufacturers often need to bond two surfaces together with a strong seal to prevent leakage between components. Traditionally, the common automotive adhesives for these applications have included hot melt materials like ethylene vinyl acetate (EVA), polyurethane (PUR) and pressure sensitive products. However, these technologies may increase production costs in certain applications. Many manufacturers have resolved this issue by switching to foam-in-place (FIP) adhesives. FIP adhesives can be used in several automotive applications, including door handles, display panels and filters. Learn how FIP adhesives can reduce your production costs by reducing material use, automating production and improving efficiencies.
BENEFIT #1: Reduced Material Use
Non-foamed hot melt adhesives are excellent for many different applications. However, they may require increased material quantities to achieve a bond strong enough to prevent leakage between certain automotive components. The need for additional materials can create increased production costs for you.
Alternatively, FIP adhesives offer reduced material use without impacting bond strength, which can reduce your overall costs. They also enable:
- Increased material volume: FIP adhesives are formed when hot melt adhesives are mixed with inert gas, producing a homogeneous mixture. As the material is dispensed, it becomes a closed-cell foam. This means that the adhesive increases in volume without increasing the amount of adhesive material needing to be applied. Therefore, you achieve greater bond surface area coverage with the same amount of adhesive material. This can help stretch your supply quantities and reduce material costs.
BENEFIT #2: Automated Production
Some automotive components, like door handles and display panels, have complex shapes. Manually applying the traditional hot melt adhesives to these types of components requires increased production time and attention to detail to ensure a reliable bond. Additionally, some operators may use more adhesive than others, creating inconsistent performance in the end product. These complexities increase error likelihood during adhesive application, which can lead to higher production costs.
FIP adhesives, however, can be incorporated into an automated production line to create a consistent application for complex automotive components and alleviate unnecessary costs. They also offer:
- Enhanced design opportunities: An FIP dispensing system can be programmed to your product’s specifications, so you can customize the bead size and density of your adhesive. These devices ensure consistent application every time, which helps reduce costs by eliminating error likelihood and reducing material waste.
- Increased output: Additionally, automated production can lead to a higher output in a shorter amount of time than manual application. The ability to produce products more quickly will also help improve cost-effectiveness.
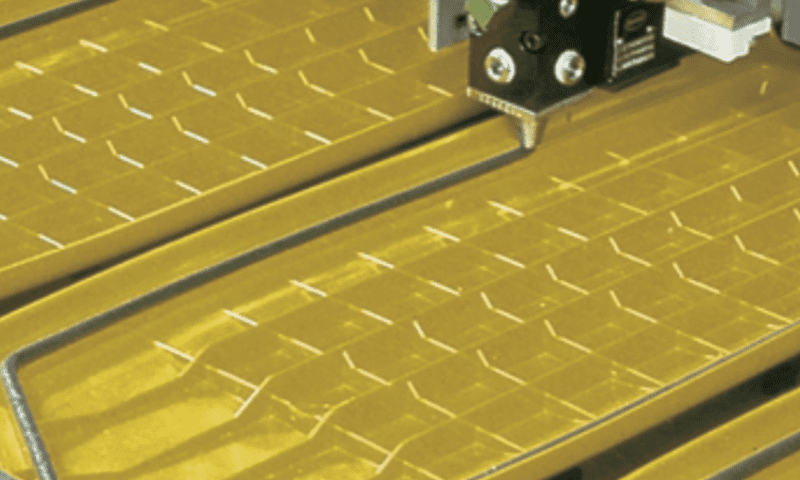
BENEFIT #3: Improved efficiency
Additionally, the low viscosity of a traditional, non-foaming hot melt adhesive can increase sagging or runniness when applied to a substrate in certain automotive assembly applications. This can cause there to be adhesive in incorrect areas. Sagging can also create a thinner line of adhesive, which may require additional adhesive material to fix. Further, non-foamed adhesives may not be able to penetrate porous materials, resulting in a weakened bond between certain substrates.
FIP adhesives have characteristics that will mitigate these performance issues while also reducing costs overall. In particular, they possess:
- Increased viscosity: Foamed adhesives have a higher viscosity than non-foamed alternatives. This property helps reduce sagging and runniness, so the adhesive will stay in place once applied, helping to avoid errors and unnecessary costs.
- Improved gap-filling abilities: Upon assembly, the FIP adhesive will spread between flanges and into surface imperfections. Therefore, the adhesive can achieve total contact between porous surfaces. Rest assured that you won’t need to seek smoother materials to achieve a strong bond between your components.
- Expanded range of technologies: FIP adhesives can be made with several different adhesive technologies, including:
- Hot melt thermoplastic sealers
- Single-component polyurethanes
- Silyl-modified polymers
This range of choices ensures that you’ll find a solution that’s most compatible you’re your materials, so you won’t experience increased costs with trial and error of various adhesive technologies.
Bostik offers a variety of FIP solutions designed to work with your automotive production needs.Our products are ideal for common FIP gasketing and sealing systems, such as Nordson’s industry-leading equipment, so you can easily integrate them into your production lines.
Contact a Bostik representative to learn more about FIP adhesives and how they may help you reduce production costs.
You can also check out this other relevant content: