Dec 11, 2020 - 10 min
Should You Consider an Alternative to Your Aerospace Epoxy Film?
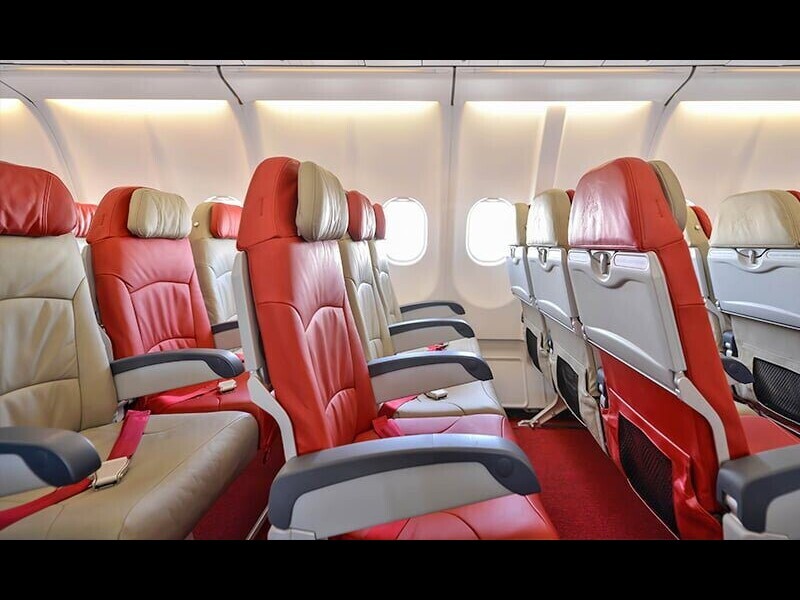
While epoxy films are commonly used and serve as a strong bonding method, they can be over engineered for certain aircraft interior applications. In these cases, an epoxy may give more strength than necessary and cause the following issues:
- Substrate failure
- Inefficient processing conditions
Property | Polyurethane | Epoxy |
Storage Temperature | Room temperature, up to 90-100°F | Below 40°F |
Shelf Life | 1 year or more | 1-6 months, depending on storage conditions |
Cure Time | 10 minutes in 340°F, or 20 minutes in 310°F | 60 minutes in 360°F |
Surface Preparation | No primer needed | Primer needed in most cases |
Advantages of Switching to a Polyurethane Film
No Autoclave Needed
Polyurethane films do not require the use of an autoclave. These pressure chambers, which are necessary for epoxies to cure, add significant cost to production. This is because autoclaves cost millions of dollars and are almost always the bottleneck for manufacturing plants. By eliminating autoclaves, companies are able to save time and money.Potential for Increased Throughput
In addition to being “out of autoclave”, polyurethane films require less processing time than epoxies. This further improves their potential for increased throughput. For example, a typical epoxy film requires at least 60 minutes at 350°F to cure. Polyurethane films will achieve maximum cure in 10-20 minutes at 330°F.Better Wet Out of Honeycomb
The primary failure mode of sandwich structures is delamination at the honeycomb/pre-preg interface, which is an issue in the industry. However, adding a thermoplastic film to improve wet out allows for greater flow of adhesive, which helps in obtaining a uniform bond line at this interface and avoid delamination.Flexibility
Polyurethane films can be thermoplastic at low temperatures and thermoset at high temperatures. This is important because at low temperatures, the resin is able to flow and create an even bond line at the honeycomb/pre-preg interface. As it reaches a certain higher temperature and becomes thermoset, however, it irreversibly cross-links, creating a strong, permanent bond. As a result, polyurethane films can be rigid, like epoxies, but also maintain flexibility. They also can be thermoformed, which means these films can cure and hold their shape with the same heat used to form aircraft interior panels. This makes manufacturing processes easier than having to first form the part and then cure it in an autoclave, as with epoxies.Smart Thermoplastic and Thermoset Polyurethane Films
Bostik manufactures smart thermoplastic and thermoset polyurethane films that can replace epoxies in certain aircraft interior applications. In particular, they offer the following benefits:- Ease of handling and application
- No VOCs in their formulation
- Room temperature storage conditions
- Flame retardancy