Aug 20, 2020 - 10 min
Quick Guide to Successful Flexible Packaging Adhesive Trials
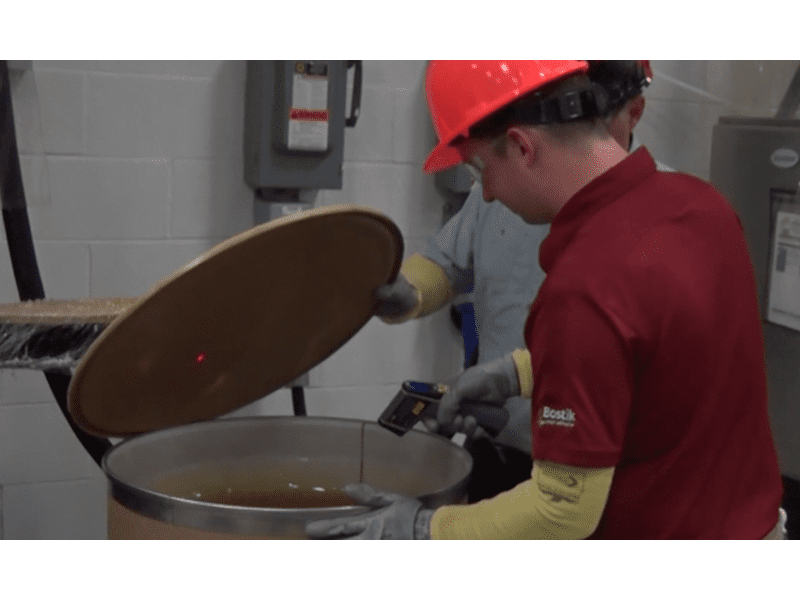
In today’s fast-paced manufacturing environment, you’re likely tasked with keeping production lines moving and output volume high. This can be challenging, especially when you need to trial a new raw material or package design. Follow the simple tips in this flexible packaging adhesive trial guide to help you prepare and optimize your next trial for success.
BEFORE THE TRIAL:
Tip #1: Conduct a Pre-Trial Meeting
Prior to any trial, it’s important for your team to meet with your supplier’s technical team of engineers and R&D chemists. Individuals from your team should include anyone who will be there during the trial, such as operations managers and lead operators.
During this time, be sure to discuss:
- Trial goals
- What end-use performance level do you want to achieve?
- How long would you like the trial to run?
- Application needs
- How does the adhesive need to be applied?
- What is the current adhesive technology and its application method?
- Does the adhesive have any storage or pre-mixing requirements?
- Equipment specifications
- What type of equipment do you have, and how does it impact the adhesive?
- What are your operations temperatures, cylinder sizes and line speeds?
- Required substrates
- What substrates do you need to bond together?
- What challenges do they present, if any?
- Communication plan
- Establish a communication plan and how you’d like to maintain contact with your adhesive supplier to ensure all questions are addressed and needs will be met. This communication will help shorten the trial length, keep your downtime to a minimum and increase likelihood of success.
Tip #2: Understand Any Hurdles Upfront
In addition to assessing trial needs, think about what hurdles might arise ahead of time, and discuss them with your adhesive supplier.
Common hurdles include:
- Not accounting for a different processing window
- A new material will likely run differently than the existing material, especially when switching technologies.. For example, different technologies can require different coating methods, such as gravure, slot die and flexo printing. Likewise, different adhesive grades – even of the same technology – may require different oven temperatures, adhesive mixing speeds and/or recirculation equipment. It’s important to be prepared for how differences may impact the necessary equipment settings and trial results.
- Having the incorrect equipment set up, such as the improper cylinder size, which dictates the coat weight of the adhesive
- An improperly sized cylinder cannot be easily changed during the trial and will impact the adhesive coat weight and the overall performance. Be sure to have the correct cylinder set up ahead of time based on your specific production line needs.
- Not properly setting the ovens
- While adjusting the oven temperature is easy to fix during a trial, it’s still a good idea to assess oven effectiveness ahead of time and set proper temperature levels for an efficient trial. Determine the maximum temperature your substrates can handle. This will be the upper limit to set for the oven.
Tip #3: Know the Recommended Processing Parameters
Prior to conducting a trial, consider these recommended processing parameters for your adhesive technology:
Application Method | Gravure coating |
Coat Weight | 3-4 lb. ream |
Line Speed | 600 – 1,200 ft/min. |
Common Substrates | OPP, PET, Paper |
The image below depicts suggested processing setup.
DURING THE TRIAL:
Tip #1: Have the Supplier Onsite
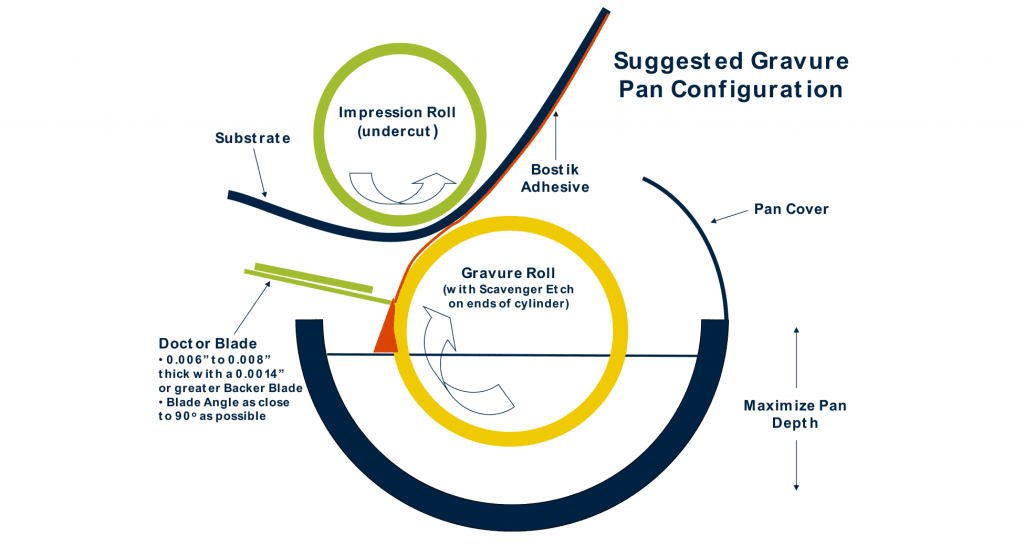
When running a trial, it’s a good idea to have your supplier’s technical team there onsite. If any issues or troubleshooting needs arise, they will be able to easily and quickly address them, giving you peace of mind.
Tip #2: Get More Hands on Deck
Consider having more line operators and engineers during a trial than you would on a typical production run. The increased level of assistance will help you monitor all areas, which is especially important when trialing a new raw material or package design. In particular, you’ll want to assess:
- Adhesive coat weight
- Adhesive dryness before winding the roll
- Clean coating with no streaks
Tip #3: Assess Quality Control and Process
Throughout the length of the trial, consistently check the adhesive coat weights and product seal strengths to ensure you and your customers’ quality needs are met. Additionally, verify that the adhesive is being properly applied and the equipment is working correctly.
AFTER THE TRIAL:
Following the tips above will help set you up for a successful trial. Once the trial has been completed, discuss with your supplier the timeline and next steps for further trials or commercialization. This timeline may be based on you or your customers’ needs. Some suppliers also can assist in qualification protocols, such as film aging or blocking/storage condition testing.
If the trial did not go as well as planned, conduct a post-trial review with your supplier’s technical team to identify:
- What went wrong
- How it can be avoided in the future
- A revised plan for the next trial based on your or your customer’s timeline
For example, you may want to consider a different gravure pan setup, oven temperature or mixing speed.
HOW BOSTIK MAKES YOUR FLEXIBLE PACKAGING ADHESIVE TRIALS EASY
- Thorough Communication
Bostik’s technical team maintains constant communication with you from the first trial through the full qualification process. You’ll be assigned a dedicated technical expert to provide you with trial reports, adhesive samples, internal testing and more, to ensure:
- The correct adhesive technology has been chosen for you and your customers’ needs
- Potential issues are addressed to help the new adhesive run smoothly and quickly
- You understand what worked or what didn’t work after a trial has been completed
- Personalized Support
By coming onsite for the trial, our experts are there to answer any questions you may have about your specific needs and identify other ways to optimize your production lines, saving you time and money.
Additionally, our experts will train your line operators and engineers to ensure they know how to properly run the adhesive after the trial is over.
- Extensive Capabilities
Our analytical lab and testing facilities allow us to ensure the recommended adhesive technology is ideal for your application before the trial begins. We offer extensive microscopy capabilities and can evaluate a trial coating.
We also offer an in-house pilot coater to conduct an adhesive trial with your substrates on your behalf, if you’re unable to get production line time for a trial at your plant.
Want to get started with a flexible packaging adhesive trial? Contact a Bostik expert today!