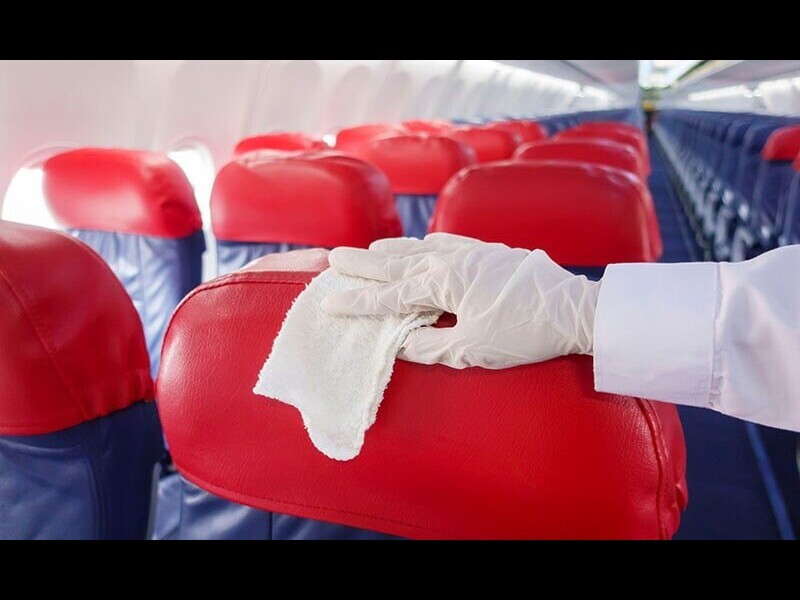
A recent study determined that consumer travel choices are based on aircraft cleanliness as much as price. To meet these heightened demands, it’s imperative that aircraft interior manufacturers consider new methods during the design phase to improve cleanliness onboard.
Learn about three key hygienic innovations that could be implemented in your aircraft interior production process that still meet passenger preferences for comfort, safety and privacy.
Touchless Lavatories
Aircraft lavatories are a common point of concern for passengers when it comes to cleanliness. Though flight crews have strict rules for sanitation, it is still possible to spread germs between cleanings through high-touch areas like the lavatory.
To address these concerns, aircraft interior manufacturers should consider designing touchless lavatories. Several projects for touchless lavatories have been prototyped in recent years, including touch-free soap dispensers, hand dryers, faucets and toilets. These innovations use motion-sensing technology to eliminate buttons and handles, where germs are frequently found. By reducing the number of surfaces a passenger must touch, fewer germs will be spread in the lavatory.
Besides improved cleanliness, touchless lavatories enable other benefits, such as:
- Reduced waste: By switching from paper towel dispensers to touch-free hand dryers, aircraft passengers will produce less waste during flights.
- Improved water preservation: Automated flushing and faucet systems can control how much water a passenger may use in the lavatory. This helps stretch the supply of fresh water within the aircraft.
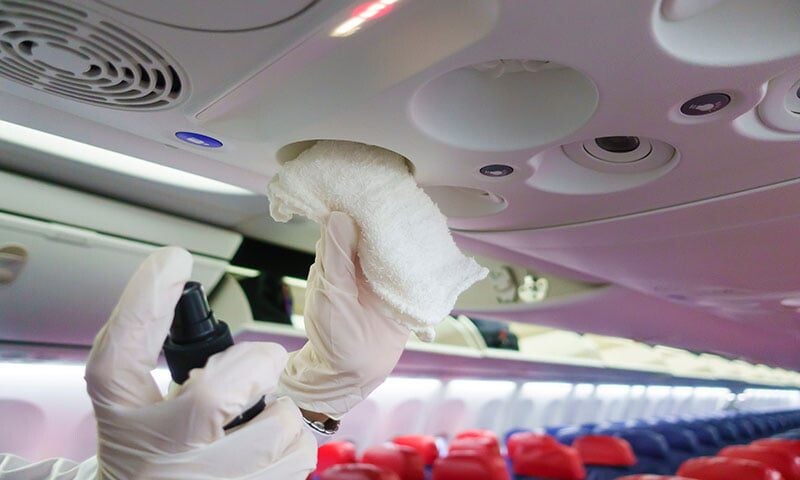
Seating Modifications
In addition to the lavatory, passengers may also be wary of spreading germs through their seats. To address these concerns, consider introducing modified seating in aircraft interior designs to help reduce the spread of germs. Staggered seating and cabin dividers can help reduce the amount of contact between passengers.By adding more distance between rows or implementing physical barriers between passengers, the chances of germs being spread from person to person are decreased.
These seating modifications offer additional benefits, such as:
- Increased privacy: Passengers who wish to sleep, read or work during flights may find cabin dividers useful for providing privacy from other riders.
- Improved safety: Staggered seating can provide more space between rows, enabling passengers to easily move in the event of an emergency.
Simplified Seat backs
A recent study found that the seat back pocket is one of the most contaminated areas in an aircraft cabin.This is because the seat back is a high-touch area. In-flight literature is stored in the seat back pocket, which can be touched by dozens of passengers in one day. Passengers may also use the pocket to store snacks or personal items. This can also contribute to the spread of germs.
To address this, aircraft interior manufacturers should consider redesigning new, innovative seat backs that remove seat back pockets altogether. For example, instead of printing safety guides and in-flight menus, include information on literature panels applied to the seat back. This ensures that passengers can still get the information they need and reduces the number of touched surfaces. Removing the seat back pocket also encourages passengers to hold onto trash and personal items, helping to further improve aircraft cleanliness.
Simplifying seat backs also enables some other benefits, such as:
- Quicker clean-up speed: By removing the seatback pocket, flight crews can reduce the amount of time collecting trash between flights, making the clean-up process faster.
- Reduced printing fees: Implementing literature panels can take away the need for printed materials, helping airlines to reduce costs.
How Can Adhesives Help You Incorporate These Aircraft Cleanliness Innovations?
While adding these hygiene-improving innovations enables aircraft interior manufacturers to meet passenger demands for increased safety, they could pose challenges to the manufacturing process, such as:
- Added weight: Implementing new equipment on the aircraft may increase its overall weight.
- New production materials: You may need to implement new materials into your production process to bring these enhancements to life. These changes may require downtime, maintenance and other expenses.
Fortunately, Bostik’s adhesives can help mitigate some of these challenges. We offer lightweight adhesive solutions that work with a variety of innovative aerospace substrates to make it easy to implement new features. Plus, our experts can custom formulate solutions for specific applications. Rest assured knowing we’ll work with you directly to ensure testing is complete. Contact a Bostik representative today to learn how adhesives can help you meet consumer demands for aircraft cleanliness.