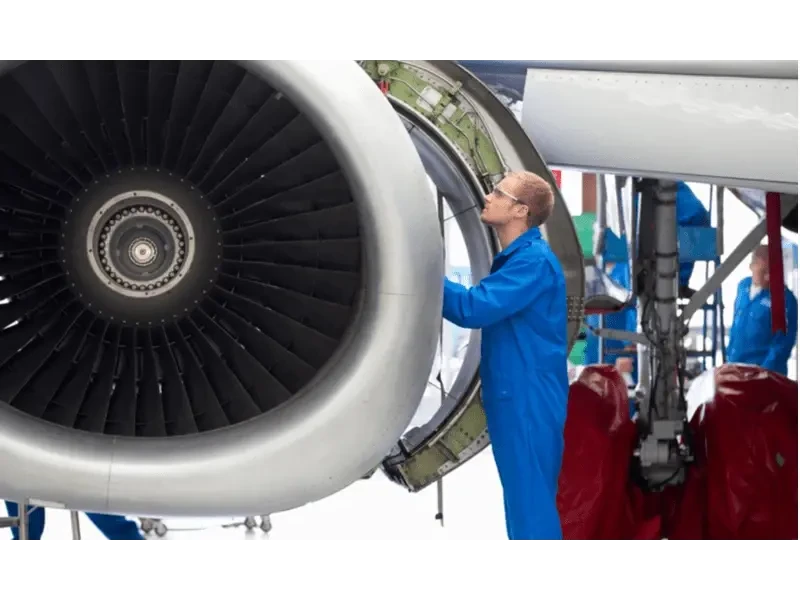
Manufacturing processes of aircraft are changing due to numerous changes to the industry in recent years, and it’s making OEMs take a closer look at how they can reduce spending. As manufacturers look for areas to save on their production and operations, they should consider the four ways adhesives can reduce costs:
1. Switching to Polyurethane Films
Epoxy films are often used for strong bonding, but can become too delicate for aircraft interior application needs. This can lead to issues with substrate failure and unsuccessful processing.However, non-epoxies like thermoset or thermoplastic polyurethane films can solve these problems, reducing the need for repairs. It can protect wings, stabilizers, struts and landing gear from abrasion, UV light and water erosion.
- Thermoset: This material forms an irreversible chemical bond once it cures. It offers increased strength and higher heat and chemical resistance than epoxy films. Thermoset film can provide increased rigidity due to cross-linking chemistries that happen when it is cured.
- Thermoplastic: This material becomes soft when heated, then sets when it’s cooled. The heating and cooling process for thermoplastic film can be repeated numerous times.
Polyurethane films can be stored at room temperature with a shelf life of a year or longer, whereas epoxies need to be kept in conditions below 40 degrees and will last between one to six months. Unlike epoxies, polyurethane films do not require the use of an autoclave, which can raise production costs exponentially. The curing time for polyurethane lasts between 10 to 20 minutes at lower temperatures than epoxies, which typically need a 60-minute curing time. Polyurethanes also do not need a primer during surface preparation, while epoxies often do. This helps manufacturers reduce process time and material costs.
2. Increase Production of Smaller Aircraft
More OEMs are increasing their production of smaller aircraft because they have better fuel efficiency than larger aircraft. Better fuel efficiency helps reduce operating costs. This also means manufacturers can use lighter weight materials in the assembly of smaller aircraft, which are compatible with lightweight adhesives, as opposed to heavier, more expensive hardware. OEMs can save weight with adhesives rather than mechanical fasteners that require thicker substrates to support stresses around bolt holes. Up to $1,000 in fuel costs can be saved over the lifespan of an aircraft for every pound of reduced weight.
3. Consider Adhesive Options for Interiors
Adhesives have the ability to both enhance the interiors of an aircraft while reducing production and operation costs for manufacturers. Some of the adhesives experiencing heightened demand for interiors include:
Aerospace plastics: Plastics are versatile, and can be used in many applications like seats, trim, entertainment systems, windows and overhead bins. This helps manufacturers reduce costs by only needing to invest in one adhesives for multiple substrates. Plastics also provide innovation opportunities with the ability to be easily molded into both ergonomic and aesthetically pleasing designs. Plastics have already been utilized in touchless bathrooms, extra storage and removable tray tables. Designers can also consider more options for color palettes, textures and patterns while not compromising on durability and function.The lightweight of plastic material can also reduce costs by contributing to fuel efficiency. Some plastic components are up to ten times lighter than previous metal components.
Web Adhesives: Another factor manufacturers have to take into consideration is governmental pressures to increase output, fuel efficiency and safety. Aircraft interior web adhesives are ideal for seating, upholstery and decorative trims. The permeability of web adhesives allows them to help reduce weight while still providing strong adhesion. They alsoprovide a range of melting points for different applications and substrates. For example, webs such as PE75 and PE85 have low melting points and can be used for low melting foams in aircraft seating. Other web adhesives have higher melting points and can handle applications like skin-to-core bonding that require higher temperatures while in use.Manufacturers should be sure the web adhesive has the correct melting point for the desired performance, other the substrate could be damaged during the adhesive application.
4. Making on-site repairs
The growing changes in aircraft manufacturing is also helping save production time and costs on repairs. More OEMs are using composites with carbon fiber and epoxy, which helps save expenses. In fact, carbon fiber is expected to be worth $6.3 billion by 2025, which is nearly an 11% growth rate from recent years. With the help of structural adhesives, composites have gone from being secondary materials in aircraft to making up half of the structures, reducing the weight in engines and aircraft bodies. Structural adhesives also assist in lowering the temperature and vibration levels, which means there will be fewer repairs needed and more cost savings. The use of structural adhesives and composite materials requires less equipment for repairs, making it easier to complete repairs at the gate. This can decrease the amount of wasted air time to maintenance locations.
How Bostik Can Help You Save
Bostik offers a range of adhesive technologies for aircraft interior applications including:
- Film adhesives: These solutions form a thin, flexible layer that can be heat activated or pressure sensitive, helping ensure repeatable performance characteristics for your application needs.
- Liquid adhesives: From water-based to solvent-based, these products offer versatility and scale for any size aircraft interior application.
- Web adhesives: Offering consistent usage control while optimizing weight to performance criteria, Bostik’s web adhesives are VOC-free and handle like fabric for easy application bonding. Bostik webs can also be pre-applied to one substrate and then bonded to another substrate in a secondary process.
Contact a Bostik representative today to begin finding ways to reduce costs with your aircraft manufacturing processes.
Other content relevant to this topic:
Three Key Usage Considerations for Aircraft Interior Web Adhesives
What Aerospace Megatrends Mean for Adhesives
Aircraft Manufacturing Trends, Smart Solutions That Address Them