Jan 19, 2022 - 10 min
How Resealable Packaging with M-Resins Reduces Plastic and Food Waste
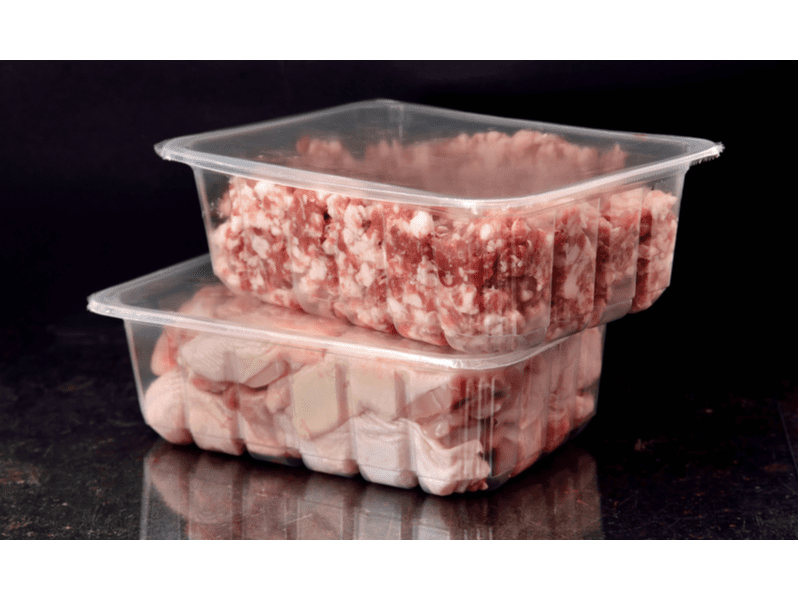
As consumers become increasingly aware of the amount of food and plastic waste ending up in landfills, state and national governments are making note, too. In the U.S. alone, around 10 thousand tons of plastic and 80 billion pounds of food contribute to landfill waste each year, more than any other country worldwide.
While packaging waste should be minimized, well-designed packaging can eliminate its weight or more in plastic and food waste. Therefore, as the need for improved sustainability grows, many food packaging manufacturers are turning to resealable technology to limit environmental impact. When doing so, it’s important for them to understand how adhesive choice can further enable them to achieve sustainability goals. Find out how resealable packaging allows you to reduce plastic and food waste and why Bostik’s M-Resins make it even easier.
Benefits of Reseal Technology
How Reseal Technology Reduces Plastic Waste
When designed properly, flexible reseal packaging can reduce the amount of plastic packaging material used in more traditional, fully rigid containers. For example, a flexible, resealable lid results in a package that weighs 30% less when replacing a rigid lid or clamshell. When resealable lidding films are used with mono-material trays (e.g., APET), the sustainable benefits are further amplified, because they enable the tray to be recyclable. This greatly reduces the total environmental impact of the resealable package.
With non-reclosable plastic packaging, consumers often store leftovers in additional packaging. Reseal technology, on the other hand, allows for all contents can stay fresh and secure in the same packaging. This means that secondary packaging isn’t used and additionally disposed.
How Reseal Technology Reduces Food Waste
In a 2020 study* on food packaging sustainability, researchers found that packaging only represents a minor part of the total environmental impact of food products. Food itself, however, can have an environmental impact 30 times greater. Fortunately, reseal technology keeps food fresher for a longer period of time than other packaging formats. Saving 3.5% of the food in a package from spoiling can fully offset the environmental impact of the package.
How Bostik’s M-Resins in Your Reseal Technology Further Help Reduce Plastic and Food Waste
What are M-Resins?
Ideal for multi-serve food packaging applications, such as sliced meat, cheese and baked goods, M-Resins are based on extrudable, PSA technology and can make up the resealability within multi-layer lidding films. These specialty films can be heat sealed to a rigid or semi-rigid tray to make a hermetic seal. When films are peeled for the first time, the M-Resin layer is revealed and able to provide resealability for re-opening and closing the lid.
M-Resins can be processed on standard multi-layer extrusion equipment, including blown and cast film lines. When seven or nine layer lines are used, the resulting films can be down-gauged to bring high performance and functionality in a thin and lightweight structure. When these thin, multilayer films replace a mono-layer rigid lid or clamshell design, the weight savings of the entire package can decrease by as much as 30%.
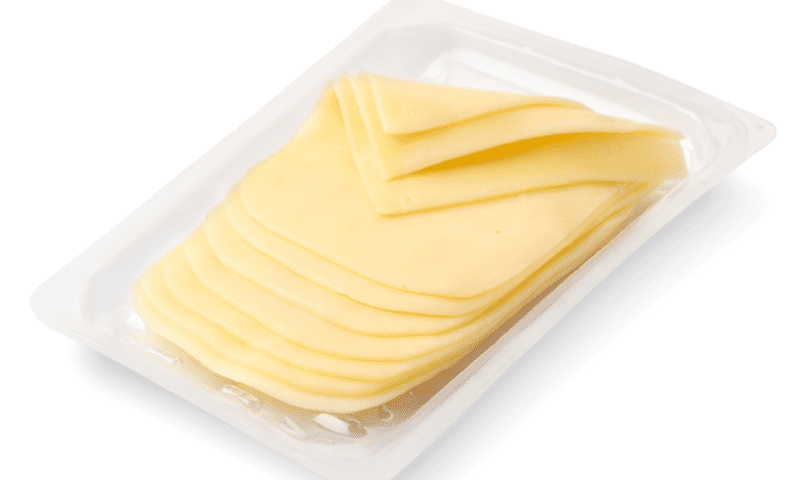
Why are M-Resins better for reducing plastic and food waste than other reseal technologies?
M-Resins were designed to streamline the way flexible lidding films are manufactured and ultimately used. They are integrated into the core film and eliminate the need to apply secondary adhesives and labels, offering:
- Enhanced Usability: As mentioned before, M-Resins can be processed on conventional, multilayer cast and blown film lines. They are designed to coextrude well next to a variety of polymers, which allows for using the same M-Resin grade across multiple film structures with different functional or sealant layers.
- Increased Efficiencies: Films containing M-Resins are functional without the need for laser scoring and can be sealed to packages using conventional tray lidding equipment. This allows manufacturers to utilize equipment they already have instead of making new investments. Sealing can be achieved with the same conditions and line speeds as traditional, single-peel films, making the switch seamless for brand owners.
Why Work with Bostik?
With more than 125 years of industry experience, Bostik used its expertise to patent M-Resins as the first extrudable reseal adhesive technology, making us a trusted leader in the market. Additionally, our technical experts can create custom resins to meet your specific needs. Ready to get started using M-Resins to reduce plastic and food waste? Contact a Bostik expert today!
To learn more about M-Resins and how they help you, check out:
Video: M-Resin Adhesive Technology
Virtual Demo: Learn About Bostik M-Resin® Reseal Technology
4 Ways Bostik’s M-Resins are the Smart Solution for Resealable Packaging
*ecoplus, BOKU, denkstatt, OFI (2020): Food Packaging Sustainability: A guide for packaging manufacturers, food processors, retailers, political institutions & NGOs. Based on the results of the research project "STOP waste – SAVE food". Vienna, February 2020