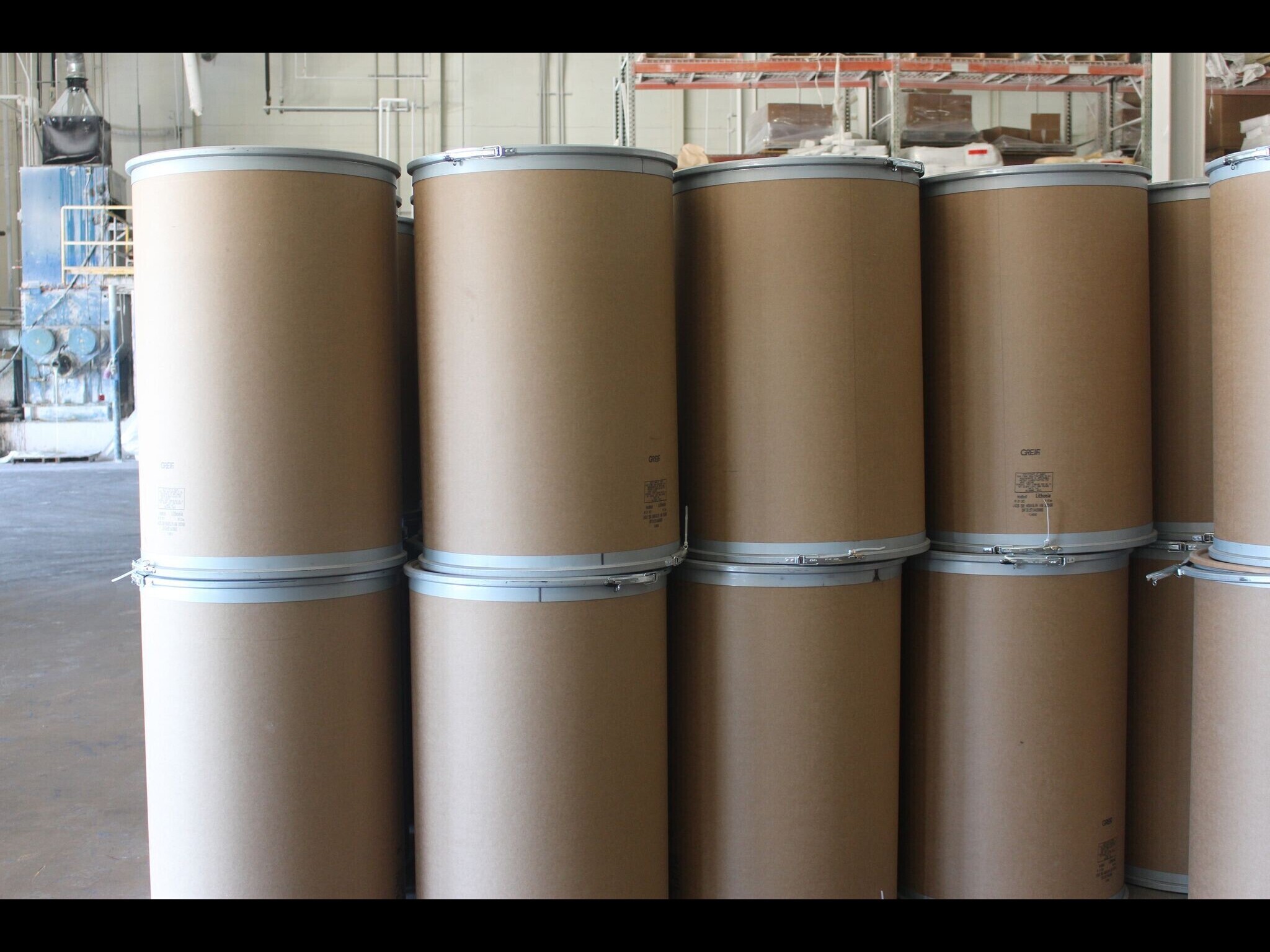
Hot melts are often a go-to adhesive choice due to their versatility, strength and flexibility. As a result, manufacturing plants invest large sums into their hot melt equipment to support their production needs and are keen to spend necessary funds to ensure proper equipment maintenance and repairs are conducted. This means that operating hot melt adhesives in production lines can be costly.
Fortunately, hot melt drum unloaders are an option that can reduce overall production expenses. Gain insight into important measures that make cost savings easy to accomplish.
Cost Saving Measure #1: Decrease Charring Likelihood and Energy Usage
Adhesive charring is a leading cause of hot melt equipment downtime costs. Charring occurs when the adhesive properties are altered through thermal degradation and oxidation; the adhesive loses its thermoplastic nature and overheats, or chars. Charring can go on to clog filters, which negatively affects production throughput.
Common Reasons for Charring
Typically with an adhesive holding tank, all the adhesive is melted upfront and remains in the tank. If it’s not used at once, it can start to degrade due to oxygen exposure. Therefore, if production is stopped overnight and no longer continually kept heated and softened or if the adhesive is stagnant in the holding tank for any downtime, the adhesive can start to char, leading to:
- Increased adhesive waste
- Heightened downtime to clean the char
To counteract this as much as possible, production lines that use holding tanks usually keep their adhesive temperature at just above an adhesive’s softening point when operations are on pause. This helps the adhesive sit at the lowest temperature possible to reduce char formation and adhesive degradation. It also helps control the viscosity levels, which determine adhesive flow. However, this approach can increase energy usage and associated costs throughout the plant.
Fortunately, the use of a holding tank is optional with hot melt drum unloaders; instead, a drum unloader can be directly connected to the line. This allows you to only soften and melt the adhesive as it’s needed, lessening the chances of charring as well as decreasing energy usage and overall production costs.
Cost Saving Measure #2: Decrease Material Expenses
Drum unloaders also allow you to reduce your overall material expenses in the following ways:
Decreased material waste: When using a drum unloader, you can unlatch the drum’s lid and bottom when its adhesive volume gets low. This allows you to retrieve any adhesive that remains on the cookie plates, which the platen seal ring was unable to extract. Typically, this results in an extra inch of material; by considering the cost per pound of adhesive, this could help you utilize 99 percent of material inside the drum.
Reduced processing needs: Drum unloaders are designed to get more adhesive through a line per hour compared to other equipment options. This enables drum unloaders to better handle wider lines that require more adhesive. Drum unloaders also offer fast speeds for changing out drums. This reduces downtime and helps prevent injuries related to lifting or dumping material from the drums, allowing manufacturers to keep operation costs down.
How Bostik can Help with Drum Unloaders:
In addition to offering guidance and testing to determine the right adhesive for your application needs, Bostik’s industry experts can help you decide if drum unloaders are right for your adhesive application processes and further discuss ways it can reduce costs.
Do you still have questions about how drum unloaders can reduce your costs? Contact a Bostik representative to learn more about the benefits.
Learn more about drums and tips for efficient adhesive manufacturing:
5 Tips for Hot Melt Drum Unloader Preventive Maintenance