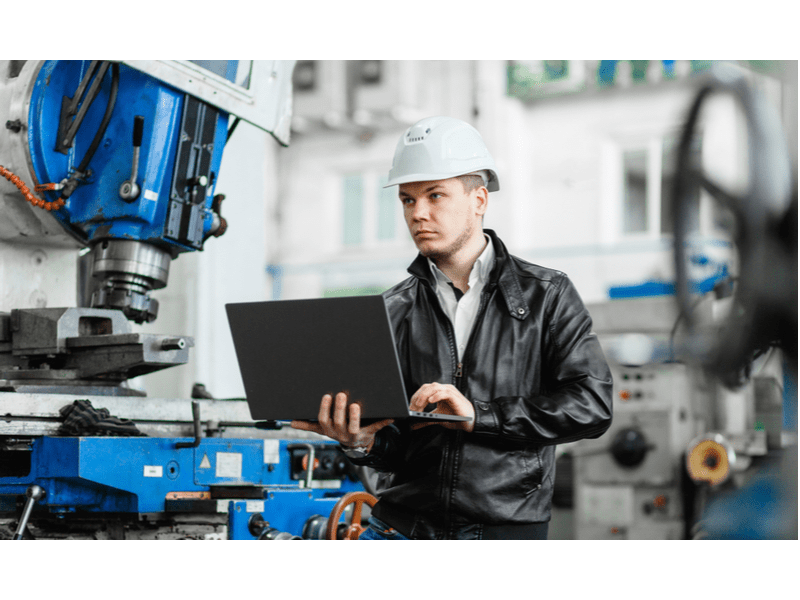
At your MRO plant, it’s important your production processes run smoothly and products are manufactured efficiently and effectively. While locking devices are traditionally the go-to solution for protecting nuts and bolts, threadlocking adhesives offer a better, long-term solution that improves equipment and enhances processes. However, some misconceptions may be stopping you from utilizing them at your plant.
Get the facts about these adhesives, and learn how they can help your plant compared to locking devices.
Misconception #1: Threadlocking adhesives are for permanent use only
Threadlocking adhesives are applied to nuts and bolts to mitigate equipment vibration and protect against corrosion from moisture infiltration. Because they set to form a thermoset plastic bond between the nuts and bolts that is more durable than a nylon nut, many manufacturers think this means their bond is permanent and that they are unable to be removed if necessary.
Truth:
In fact, threadlocking adhesives are available in service removable options. These adhesives can be removed with a simple hand tool and are not permanent bonds.
Misconception #2: Threadlocking adhesives aren’t available in various grades
While many manufacturers know what threadlocking adhesives are, they often think these adhesives are available in one grade only. Likely used to the wide array of shapes and sizes that locking devices come in, this perception can turn them away from using these adhesives, thinking they won’t be able to meet specific use cases.
Truth:
Threadlocking adhesives are available in different ranges for numerous applications. For example, low-strength threadlocking adhesives are designed for anything less than ¼” and are even for softer metals like aluminum. This capability enables manufacturers to remove them quickly after application if needed. Threadlocking adhesives are also available in high strength formulations for more permanent application requirements.
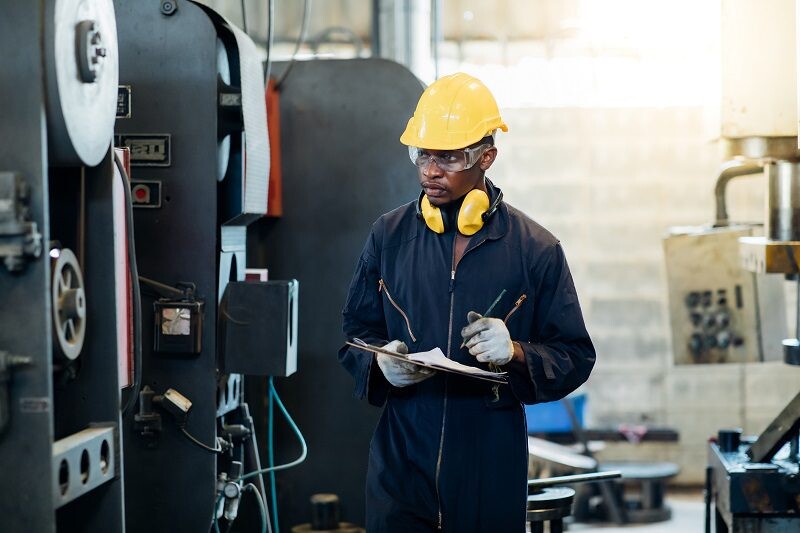
Misconception #3: Threadlocking adhesives increase plant costs
Manufacturers are familiar with locking devices and likely have them in every shape and size available in their inventory. While they may fail or get lost, they are inexpensive to replace when needed and doing so isn’t an issue. Comparatively, they may see the upfront cost of threadlocking adhesives as more expensive than locking devices and are not interested in using them as a result.
Truth:
While threadlocking adhesives may cost more upfront, they enable plants to reduce costs overall in the following ways:
- Reduced accident likelihood: Locking devices inherently fail because of heavy equipment vibration and this can cause equipment to come off its track and trigger work-related accidents. Additionally, failures of locking devices on equipment can create a workplace hazard. Threadlocking adhesives eliminate these issues.
- Decreased equipment maintenance: Even when using locking devices, nuts and bolts do not have 100% metal-to-metal contact. As a result, air and moisture can infiltrate and cause corrosion. Over time, corrosion can cause the nut and bolt to seize together making it hard to disassemble the equipment and require costly maintenance and repairs. Threadlocking adhesives are able to provide that 100% contact to protect against corrosion.
- Heightened plant efficiencies: Plants often have entire storage rooms dedicated to various locking devices shapes and sizes. Threadlocking adhesives don’t require large storage space, ensuring plant space can be used more efficiently. They can easily fit in a toolkit for on-the-spot needs, also saving manufacturers time from searching for the right locking devices for a given nut and bolt. Additionally, one product will work across different nut and bolt sizes, further streamlining production. Threadlocking adhesives help create a proactive approach to maintenance repairs at a facility.
- Increased product mileage: With threadlocking adhesives, a little goes a long way. For example, a small, 50ml bottle can be used 800 times when compared to locking devices for a 3/8” nut and bolt size, which also aids in inventory cost reduction.*
*based off expert internal testing
Why Choose Bostik’s Born2Bond ™ Threadlocking Adhesives
While locking devices have historically been a popular maintenance option with fasteners, threadlocking adhesives offer distinct advantages. In addition to enabling maintenance teams to be proactive instead of reactive, they unify the assembly process, ensuring that all equipment is functioning to the same performance level. At the same time providing vibration and corrosion resistance. Bostik’s Born2Bond threadlocking adhesives in particular are:
- Single component to increase ease of use
- Oil tolerant to improve performance
- Primerless technology, can be used on inactive metals such as plated parts, stainless steel, zinc, black oxide and aluminum.
- Available in multiple strengths and viscosities to enhance flexibility
Are you ready to improve your MRO practices with our threadlocking adhesives? Contact a Bostik representative to learn how you can easily make long-lasting changes to your maintenance processes.
Learn more about our threadlocking adhesives and other MRO products here.