May 20, 2022 - 10 min
Why Polyurethane May be Holding Back Your Automotive Exterior Assembly
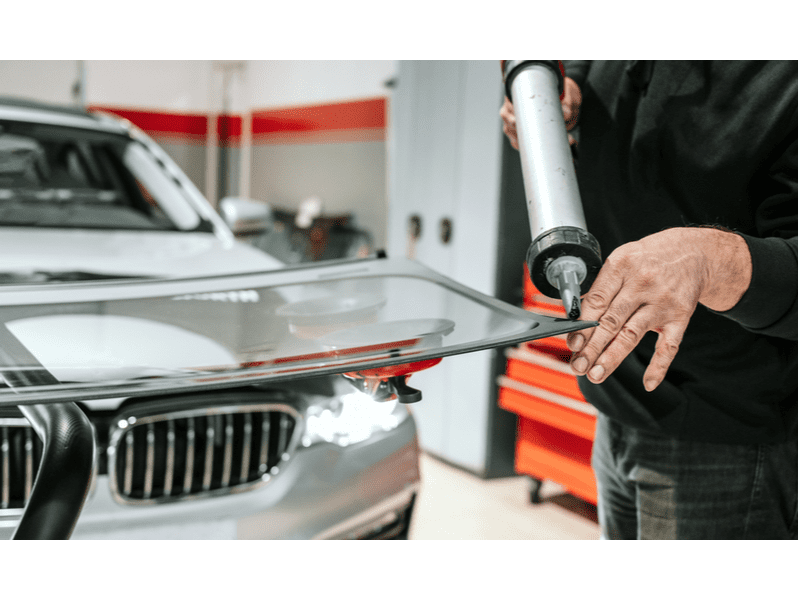
Polyurethane (PU) is the most popular polymer for automotive exterior adhesives and sealants due to its weather resistance and cost effectiveness. However, despite its popularity, it does include some limitations. In particular, it possesses:
- Raw materials that contain harmful chemicals, impacting the environment
- Primer requirements, increasing production time and error likelihood
- Little resistance to low application temperatures, causing curing challenges and increasing performance failure likelihood
Fortunately, adhesives and sealants based on SMP (silyl modified polymer) technology offer similar advantages to PU while also being able to overcome its limitations. Read how SMP can move your automotive exterior assembly forward.
Polyurethane Limitations
PU has been a common solution for automotive exterior body parts, including coating and refinishing applications. PU enables lightweight substrate bonding, which improves fuel efficiency. Its thermoforming precision allows for detail and texture in product positioning, enhancing exterior design capabilities. However, some PU features may not make it the right adhesive choice for all automotive exterior assembly:
- Harmful chemicals: PU contains isocyanates, which can pose as a safety hazard for workers. Additionally, many PU adhesives and their required primers contain solvents to address metal substrate coarseness. However, like isocyanates, solvents can have adverse affects on workers and the environment.
- Primer requirement: In order to have exterior weathering and chip protection, manufacturers must apply a PU surface primer. This means they must include an additional step in their processes, which results in additional operational costs.
- Curing challenges: Minimal resistance to low application temperatures can cause problems when PU is curing. Its dimensions can change during the cool down process, causing shrinkage and increasing stress on the material itself, which can affect product performance. While upfront costs for PU may be cost-effective, shrinkage or stress may end up affecting overall costs by increasing downtime to fix shrinkage or stress.
How SMP Addresses PU limitations
Formulated to have both adhesive and sealant properties, SMP technology is useful for acrylic panel bonding, vehicle trims and glass bonding applications, overcoming PU limitations in the following ways:
- Isocyanate and solvent-free: SMP’s ability to meet health safety requirements is one of its biggest advantages over PU. Formulated with no isocyanates and solvents, manufacturers can use SMP without worrying about any extra potential health hazards.
- Primerless capabilities: SMP can serve as a pre-treatment and eliminate the usual priming steps required with PU. This will increase operation speeds and reduce overall production costs. Additionally, you’ll decrease product volume needs and potential manufacturing errors.
- Low application temperature resistance: SMP can adhere in low temperature conditions, including temperatures as low as -52⁰F (-46⁰C). Unlike PU, it will remain flexible at lower temperatures while curing, which is necessary to avoid cracking if dimensions shrink.
Additional Benefits of SMP
Along with addressing PU limitations, SMP offers further advantages for your automotive exterior assembly:
- Fast curing: SMP cures quickly between two substrates and offers sufficient green strength to allow for accurate assembly without concerns of substrate slumping. This reduces changes of the substrates not fitting together properly after bonding.
- Weathering protection: SMP offers UV and temperature resistance, enabling it to maintain performance even after repeated exposure to the elements. Additionally, its flexibility allows it to reduce stress areas and protect against moisture that could cause corrosion over time.
- Aesthetic appeal: SMP is paintable, providing a simple method for gaining aesthetic appeal consumers desire without the need for a prime coating beforehand. With the absence of isocyanates, there is no longer possibility for a chemical reaction to cause bubbling. SMP eliminates the need for mechanical fasteners, reducing the vehicle’s overall weight. Additionally, this allows for other lighter weight substrates to be used.
Why Choose Bostik’s SMP for Automotive Exteriors
Our Bostik team’s expertise will guide you in utilizing SMP technology wherever you may typically rely on PU for your automotive exterior bonding needs. Our SMP technology addresses PU limitations and more, offering:
- Elasticity properties ranging from -40⁰ F (-40⁰ C) to 248⁰ F (100⁰ C), allowing SMP to withstand flexing and movement across temperature extremes
- High green strength, which provides the right amount of time to position automotive parts correctly while ensuring a fast, strong bond that will prevent any slumping while curing
- Long-lasting protection by mitigating chalking, shrinking or cracking over time to resist harsh UV and weathering conditions
Ready to replace PU with SMP for your automotive exterior applications? Contact a Bostik representative to get started.
Learn more about how SMP practices and benefits:
What are Silyl Modifed Polymers (SMP)?
Improve Transportation Production with Dual SMP Technology
Direct-Glazing Adhesive Challenges and How SMP is the Industry Solution