Nov 10, 2023 - 3-5 minutes
Brand Owners: Why Your Packaging Needs Heat Seal
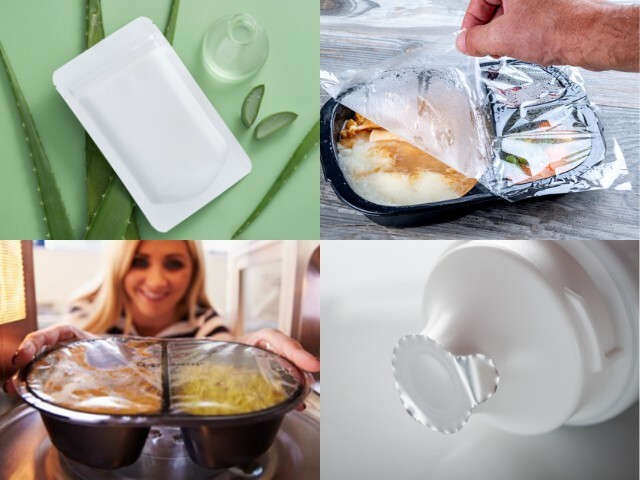
Learn how Bostik's heat seal technology addresses three key sustainable packaging goals, including reducing food and package waste, material reduction benefits, and recyclable compatibilities.
According to a 2022 report from the Flexible Packaging Association (FPA), 75 percent of survey respondents say they expect to increase their use of heat seal adhesive technology in coming years compared to their 2022 usage. Additionally, heat seal adhesives overall ranked as the third highest growth coating segment, which the FPA stated is a sign they will continue to be used more across applications.
Therefore, as a brand owner, it’s important to consider why converters are utilizing heat seal adhesive technology so frequently and how choosing packaging made with this technology can help you accomplish three key sustainable packaging goals.
What is Heat Seal Adhesive Technology?
Heat seal adhesive technology is an adhesive bonding process that uses heat to seal a variety of substrates together. These substrates include PET, PE, PP, PVC, PS, foil and paper. It can be customized for peelable or lock seals for lidding (tray and cup) as well as for labels, making it usable for a range of food, medical and industrial applications. Some key benefits of heat seal technology include:
-
Processing versatility: Heat seal adhesives can be coated or extruded, which expands the converting options and simplifies the steps to creating your end-use package. For example, a converter can purchase a film with heat seal coating extruded by the film suppliers or custom formulate with a heat seal coating to better control the peel force via coat weight and application pattern. Having multiple sourcing options helps ensure supply security to you with the end-use package structure.
-
Wide application use: Because heat seals are compatible with many substrates, you can use this packaging format for different end-use applications. Some applications already utilizing heat seal technology include dairy, produce, dual ovenable, shrink sleeve, microwave, condiment, blister and sterilization applications. Along with being able to expand the types of products you’re able to package with just one format, rest assured that your package will have been made in an energy efficient way, and your converter can reduce SKU complexity by relying on one heat seal technology for multiple package structures.
Heat seal technology is often used to create protective seals in pouches, bags, blister packs and sachets, though it also can be used in non-food packaging formats:
-
Medical devices: Sterile medical devices and diagnostic test kits packaging
-
Cosmetics and toiletries: Lipstick, eyeshadow and mascara packaging, wet wipes, facial mask pouches and toothpaste tubes packaging
-
Consumer electronics: Battery and memory card packaging
-
Automotive: Airbag and sensor packaging
How Heat Seal Technology Helps You Address Key Sustainable Packaging Goals
Sustainability Goal #1: Decrease Food and Package Waste
Heat seal technology’s performance features help contribute to decreasing food waste and package waste by preserving food and being an alternative technology to rigid packaging.
To decrease food waste, heal seal offers:
-
Chemical resistance in a heat seal helps protect the package from a product that has high acidity or chemical content. This will prevent the food from deteriorating the package seal and getting out before it is used by the end user.
-
Anti-fog abilities prevent water droplets from forming on the lid of the package so consumers have direct visibility to the product. This helps increase the likelihood that a consumer will purchase the product because they can determine if the product is fresh or free of defects.
To reduce package waste, it offers:
-
Lightweighting: Heat seal technology allows brand owners to transition from rigid top packaging to flexible film lidding to reduce plastic usage. This weight reduction can lower shipping and transportation environmental impact.
-
Reduced excess packaging: Heat seal technology provides the ability to package custom product shapes, reducing the use of excess materials needed to fit around it. The seal protection also reduces the need for secondary packaging that would result in additional waste.
-
Minimal product loss: By preventing leakage, heat seal technology reduces any product loss during storage, transportation, and consumer use. This decreases the likelihood of products being returned or disposed of due to damage, and therefore additional package waste.
By using packaging made with heat seal technology, you help reduce plastic usage and reach sustainable packaging goals; this in turn can help you directly address concerns from non-governmental organizations (NGO).
Sustainability Benefit #2: Material Reduction
Heat seal technology provides dual functionality, allowing you to get two key performance features from one solution. While the specific dual functionalities can vary depending on your performance requirements, it allows your packaging to use about 30% less material*.
-
Coatings: Dual functionality allows your converter to reduce the number of coating layers necessary to get your desired performance levels, because at least two performance capabilities, such as chemical resistance and anti-fog abilities, can be formulated into a single coating layer.
-
Extrusion: Dual functionality also enables your end-use package to incorporate dual ovenable capabilities with chemical resistance so it can easily move from a freezer to an oven or microwave without experiencing any adhesive breakage. This allows your end user to use the same package for cooking the food that was used for selling the product, further contributing to reduced material waste.
Sustainability Goal #3: Recyclable Compatibilities
Heat seal technology enables the end user to cleanly peel the lidding away from a tray or cup, allowing the tray or cup to be recycled without adhesive contamination. Heat seals are capable of this by adhering better to the film than the rigid plastic to prevent cohesive failure when peeling off the lid. This is why it’s also encouraged for converters to consider using heat seal technology with paper or CPET trays and single-ply lidding to enhance recyclability.
How Bostik’s Heat Seal Technology In Your Packaging Can Help You Accomplish Sustainable Goals
With a portfolio of both coating and extrudable solutions, Bostik can easily help reach your sustainable packaging goals with heat seal technology for your desired packaging format. Our solutions are compatible with recyclable substrates such as PET, APET, CPET, PETG, PVC, PS, PP paper and foils, offering dual functionality to ensure your packaging provides the right performance levels.
Aquagrip® and Pureseal® are water-based coatings suitable for high-temperature food and medical applications and shrink labels, with the ability to withstand microwaving, ethylene oxide (ETO), steam sterilization.
Vitel® solutions include both solvent based coatings and extrudable options for food and medical lidding applications. Our patented polyester resin technology also allows for dual ovenable capabilities.
Are you interested in learning how heat seal technology can help address sustainable goals specific to your packaging needs? Contact a Bostik expert to learn how we can help your brand improve its overall sustainability.
*based on internal testing
Other Relevant Content:
On-Demand Webinar: Heat Seal Benefits Unveiled: Markets, Benefits and Applications
On-Demand Webinar CoPET Heat Seal Coatings for Sustainable Packaging Design
On-Demand Education Series: Heat Seal Solutions with Bostik Vitels®
©2023 Bostik, Inc. All Rights Reserved
All information contained herein is believed to be accurate as of the date of publication, is provided “as-is” and is subject to change without notice. To review our full U.S. Legal Disclaimer, visit: https://bostik.com/us/en_US/privacy-policy/legal-disclaimer
See also
Back to all articles- Advanced Packaging
- Advanced Packaging
- Advanced Packaging