Jul 14, 2023 - 3-5 minutes
Bostik Spotlight Q&A: How Our Food Packaging Technical Expertise Helps You
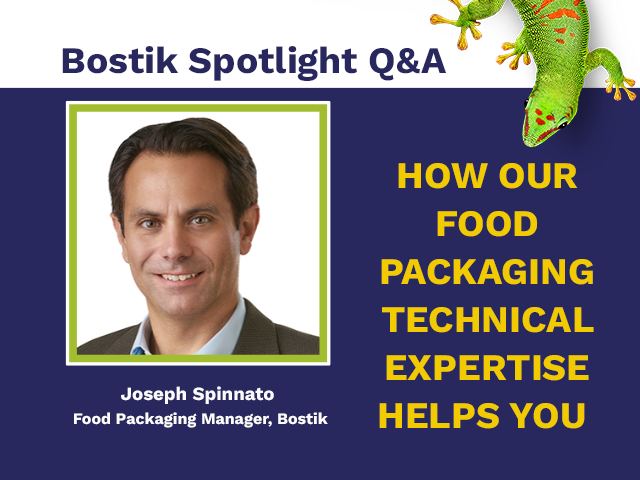
Ensure your flexible packaging complies with food safety regulations. Learn from Bostik's Food Packaging Manager, Joe Spinnato, about navigating chemical migration regulations and how Bostik's technical support team can help you deliver safe, compliant packaging.
Q: Can you start off by sharing with us a bit about what your role entails and your expertise?
A: A big part of my role involves developing protocol for chemical migration testing in food. This helps our team design laminating adhesives and coatings for food packaging products that are safe and compliant with FDA guidance. I also co-chair the Food Safety Alliance for Packaging, which helps educate the supply chain about food packaging safety and regulation.Q: What is a common struggle that converters face when trying to address food safety regulations?
A: Overall, there is a gap in knowledge around packaging materials and food safety. The FDA does not provide specific guidance on temperatures and conditions or what materials act as functional barriers. This means converters are left to determine what substrates and adhesives can be used safely when in contact with the food, which often leads to companies either making assumptions or inferences about safety and migration. This increases the risk of food adulteration. As a result, brand owners can be negatively impacted if their products experience any safety issues."...converters are left to determine what substrates and adhesives can be used safely when in contact with the food, which often leads to companies either making assumptions or inferences about safety and migration. This increases the risk of food adulteration."
Q: How does Bostik’s technical service team assist converters in addressing this gap in the market?
A: Our team of industry experts takes a step further by developing a food safety testing protocol. When converters partner with Bostik, we will conduct testing and analysis on their food packaging for potential chemical migration. This testing determines whether the package will meet FDA standards and if there needs to be additional testing. We take the time to explain why something is or is not meeting the testing standards so that converters gain an understanding of why the packaging has passed or not. This helps arm them for success in package designs going forward. Our approach formalizes migration testing throughout the food packaging industry to ensure converters deliver safe products to brand owners.Q: What can converters expect if they partner with Bostik to complete testing for food packaging?
A: Once we’ve had the initial conversation regarding our customers end-uses, such as food type, shelf-life and temperature, we determine the best route to take for testing. Sometimes, we have already developed an adhesive that meets the necessary certification requirements. If they have a need that we haven’t yet tested, we can conduct chemical migration testing to address their end-uses. Converters send us their packaging materials for lamination with our adhesives on our in-house laminator to make the packaging structure. We then test the packaging structure in an appropriate food simulant and look for chemical migrants using our analytical equipment. By utilizing equipment at our facility, the converters can get testing completed with minimal delay. Because we have our own pilot laminator, they don’t need to use their own production lines that they rely on for day-to-day operations.
Q: You mentioned Bostik has its own laminator and analytical equipment. Can you expand upon the value to converters?
A: Our pilot laminator is a productions scale laminator that allows us to test product performance, such as bond strength and material compatibility, on film, paper and foil. We can also test for product performance and chemical resistance. This laminator enables real-world testing conditions to ensure it works for converters on their own production lines. We can run water-based, solvent-based and solvent-free adhesives and coatings.Specifically for migration testing in food packaging protocol development, we can study food simulants at sub parts-per-billion levels with our analytical equipment at our research center in Dublin, Ohio. We use this equipment to develop FDA letters for converters, which provides a full analysis of whether their food packaging met food regulations.
Q: If converters want to speak to you directly, what knowledge can you provide to help their food packaging?
A: I often serve as a food safety consultant to our customers. Typically, converters are looking for general feedback on how they can reduce chemical migration, or they are struggling to interpret detailed food regulations themselves. I provide that clarity and help them determine what testing methods will work best for their needs.It’s also important to note that I work with our customers throughout their entire production. I’m involved in those first initial discussions when they’re looking for help with testing. Other times, they may already have a food package out there that they want to expand uses, or they have problems that need to be addressed quickly. Overall, our partnerships last for years, as they know they have a trusted Bostik expert they can call when needed, especially when they need answers fast. When customers work with our technical service team, they will receive more than just an adhesive solution; they have reliable, trusted experts throughout the entire process.
"When customers work with our technical service team, they will receive more than just an adhesive solution; they have reliable, trusted experts throughout the entire process."
©2023 Bostik, Inc. All Rights Reserved
All information contained herein is believed to be accurate as of the date of publication, is provided “as-is” and is subject to change without notice. To review our full U.S. Legal Disclaimer, visit: https://bostik.com/us/en_US/privacy-policy/legal-disclaimer