Feb 19, 2024 - 3-5 minutes
How to Minimize Performance Issues When Coating Hot Melt PSAs
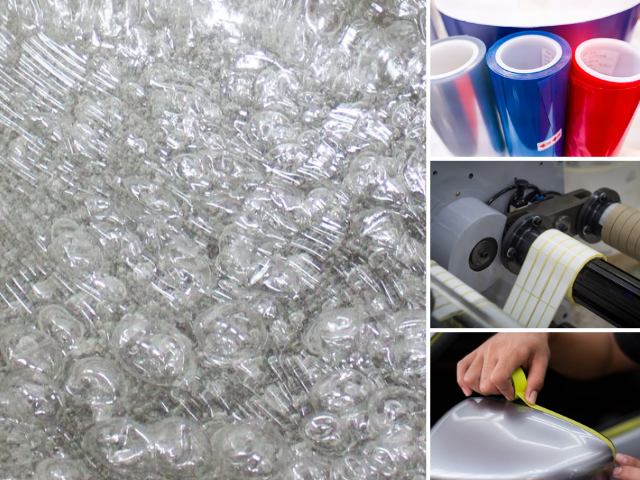
Learn about the causes and impacts of hot melt pressure sensitive adhesive (HMPSA) degradation. Find out how to mitigate hot melt pressure sensitive adhesive (HMPSA) degradation in manufacturing tapes, labels, and specialty films.
When manufacturing tapes, labels or specialty films, you likely try to reduce hot melt pressure sensitive adhesive (HMPSA) performance issues as best you can. This is because degradation can lead to either the breakdown of polymers or crosslinking, which both can have various impacts on HMPSA end-use performance.
Find out what causes degradation, how it can lead to polymer breakdown or crosslinking and how you can overcome any potential setbacks during the coating process.
Factors That Can Lead to Degradation
Two main factors can lead to degradation and impact end-use performance once you are coating HMPSAs in your processes:
- Heat exposure: Based on your specific processing system, it is possible more heat is applied than necessary during production, which can lead to changes in the adhesive’s structure such as reduction in molecular weight. Further, if the adhesive experiences overheating, its polymer chains can break down. Both scenarios may cause thermal degradation and decrease the formulation of bonding properties that enable your desired performance levels.
- Oxidation: Again, based on your specific processing system, oxygen exposure at elevated temperatures for extensive periods of time can alter adhesive properties, including causing discoloration or char formation. Oxidation can also be accelerated if the adhesive is exposed to air at elevated temperatures, as that further weakens the polymer structure.
Both heat exposure and oxidation can change the adhesive’s elasticity and viscosity levels, altering how it meets dispensing requirements and spreads across a substrate at the desired rate of flow. This, in turn, can impact the following:
- Coat weight: When heat and oxidation reduce polymer molecular weight, the overall viscosity can increase or decrease, especially under shear stress. This might mean you need to pump less despite your current equipment settings, and therefore may cause unexpected changes in coat weight and performance.
- Wettability: Changes in viscosity due to degradation can impact the wetting behavior, changing the bonding compatibilities with your desired substrates. If the adhesive’s ability is compromised, it may cause inconsistencies in coating surfaces evenly, which may also impact the ease of application in addition to ensuring proper bond strength throughout.
Additional Factors That Can Lead to Degradation
While heat exposure and oxidation play a main role in the possibility of degradation occurring, it’s important to consider these other factors that may also contribute:
- Production processes: Production processes including storage or operation times can contribute to adhesive degradation. Further, elevated temperatures or oxygen exposure that occurs during any of these stages may also impact the adhesive’s end-use performance.
- Storage: If raw materials are exposed to temperature extremes, oxygen or humidity during storage due to insufficient packaging, the adhesive formulation may not offer stable performance later when in use. This is why it’s important the packaging remains completely sealed until in use.
- Operation times: If the adhesive sits in a melt tank for an extended amount of time, it can degrade due to oxygen or prolonged temperature exposure. Further, it can worsen if it never gets cooled properly while sitting.
- Moisture exposure: HMPSAs are sensitive to moisture; if exposed, the adhesive can experience hydrolysis where the water molecules break the polymer chains. This can reduce the molecular weight and cause degradation.
- Contamination: Impurities or contaminants can get into the hot melt tank from equipment or raw materials, especially when switching out adhesives in your equipment. This may initiate chemical reactions and impacts the adhesive’s stability, which is why it’s important to complete the purge process before using a new adhesive technology.
Note About Degradation For Label Applications Specifically
Another factor that directly impacts label converters involves adjusting small components such as facestock, release liners and direct or transfer coating. These changes may impact the way your HMPSA performs if it hasn’t been formulated for specific substrates, tack and peel, bond strength or removability.
When degradation occurs in your processes, the polymer will either break down from various chemical or physical processes, or crosslinking agents will be altered. Both scenarios will cause performance changes in your HMPSA.
Performance Changes Related to HMPSA Polymer Breakdown
Polymers in HMPSAs are considered the “backbone” of the adhesive, as they provide internal strength to the HMPSA by improving elasticity and increasing viscosity. When breakdown occurs from HMPSA degradation, internal cohesive strength and the polymer’s ability to hold molecules together can be altered. While these changes may be positive or negative, it can lead to performance results you may not be expecting for your end-use application.
Changes with Internal Cohesive Strength
An HMPSA’s internal strength always consists of a balance between adhesive flow, wet out and bonding according to your application needs. When the polymer breakdown takes place, these components can become unbalanced. It’s possible the HMPSA may still be reusable if heated and cooled, but it could result in unexpected performance changes, such as reduced strength. However, if the HMPSA is heated for too long or exposed to too much oxygen, it will not be reusable at all. If changes occur with the balance of internal strength, it can also impact:
- Shear: If cohesive strength lessens, the HMPSA may become more susceptible to shear-induced deformation or failure because the adhesive may no longer be capable of withstanding external forces. This may shorten the end-use application’s lifespan, especially for durable labels or films that require strong shear.
- Tack levels: While tack typically enables HMPSAs to adhere to difficult substrates, an imbalance of internal strength may affect this capability. This is because an altered molecular structure will not be able to properly form and maintain its bond (i.e., its tack) with minimal pressure. This can cause inconsistent bonding strength amongst products or decrease overall performance for applications that require strong bonding to difficult substrates such as corrugate.
Performance Changes Related to HMPSA Polymer Crosslinking
Crosslinking involves forming covalent bonds between polymer chains in HMPSAs. Degradation can alter crosslinking agents and lead to unexpected performance results, including:
- Changes in overall tack: If crosslinking leads to increased covalent bonds between polymer chains, low pressure can occur. This will result in decreased tack, as its ability to adhere to difficult substrates weakens with low pressure. On the other hand, if there are the same or less covalent bonds formed, tack may remain the same or increase, leading to more wet out. While this may increase the adhesive’s ability to adhere to difficult substrates, it can also result in oozing and impact the aesthetics of the application.
- Reduced flexibility: As mentioned above, altered crosslinking can lead to changes in wet out, which may impact the adhesive’s ability to conform to surfaces where flexibility is necessary. It’s possible the HMPSA could experience brittleness, making it difficult to withstand deformation or mechanical stress.
How Bostik Can Help You Address Performances Changes After HMPSA Degradation
As the adhesive solutions segment of Arkema, Bostik’s technical experts are here to help you address performance issues that may arise once you are in the coating process. Our HMPSAs are designed to address your specific application needs with the ability to overcome degradation-related issues that may occur.
Bostik’s HMPSA Formulations
Designed to provide a balance of adhesive flow, wet out and bonding capabilities, the polymers in Bostik’s HMPSAs offer the necessary elasticity and viscosity levels for your end-use application needs. For example:
- Tackifying resins in our formulations help strengthen the bond between two substrates and ensure optimal tack balance for desired peel adhesion performance. They also provide softening and plasticizing effects to enhance overall flexibility.
- Plasticizer additives can also help enhance overall flexibility and maintain a certain amount of flow. Further, they can improve thermal stability and increase wet out capabilities.
Additionally, Bostik can help minimize oxidation exposure within the initial formulation to reduce possibilities of changes in internal strength during the coating process. In particular, this entails incorporating:
- Antioxidants, which slow down oxidation processes by preserving the molecular structure of the polymer, helping maintain cohesive strength. They also mitigate thermal stability when the adhesive is enduring high temperatures, protecting against heat-induced degradation. This ability to slow down oxidation and enhance thermal stability helps extend the overall shelf life of HMPSAs to streamline supply costs.
- UV stabilizers, which are designed to protect polymers from ultraviolet radiation, as it can cause changes to molecular structure and reduce cohesive strength. By absorbing or dissipating UV energy, UV stabilizers prevent any negative impacts to the HMPSA. This is particularly useful for outdoor applications that may ensure sun exposure or temperature changes.
Additionally, our HMPSAs help you reduce environmental impact. Comprised of 100% solids, they are low VOC formulations that offer fast set-up times to create a streamlined, safe work environment. Further, our formulations are compatible with bio-based raw materials to decrease carbon emissions.
Bostik’s Troubleshooting Support
If you experience performance issues during the coating process, we’re here to help. Our technical support can assist you in identifying challenges leading to degradation and developing strategies that will prevent it from happening in the future. We will work with your facility to determine what tactics are most suitable for your specific processing needs. Our experts can also conduct trial testing on our pilot coater to identify a solution that meets your performance requirements while also helping to prevent future degradation.
Are you interested in learning how:
- Our HMPSAs can help you achieve optimal performance results?
- Our technical support team can help you address performance issues occurring with your current processes?
Contact a Bostik expert to learn how we can enhance end-use performance levels and help you overcome performance issues on your production line.
For other tips to help you achieve optimal performance and processes, check out these blog posts:
What You Need to Know Before Switching Adhesives in Your Hot Melt Tank
5 Tips for Hot Melt Drum Unloader Preventive Maintenance
6 Easy Hot Melt Tank Preventive Maintenance Tips
©2024 Bostik, Inc. All Rights Reserved
All information contained herein is believed to be accurate as of the date of publication, is provided “as-is” and is subject to change without notice. To review our full U.S. Legal Disclaimer, visit: https://bostik.com/us/en_US/privacy-policy/legal-disclaimer