May 29, 2024 - 3-5 minutes
Why Certain Pressure Sensitive Adhesives are the Right Choice for Colored PPF
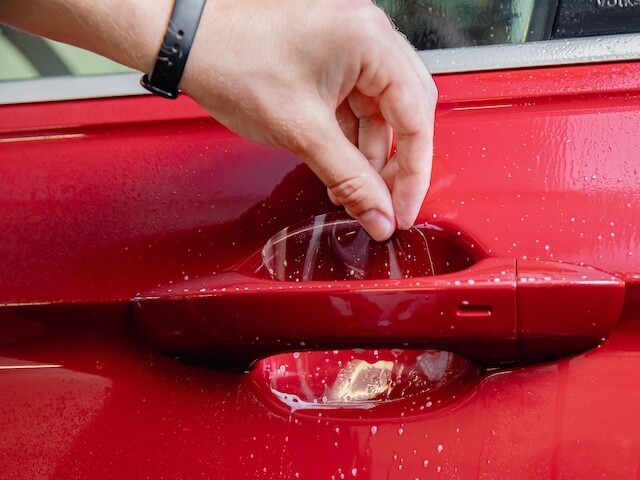
Find out how colored paint protective film (PPF) and advanced pressure-sensitive adhesives (PSAs) enhance sustainability, aesthetics, and customization in the automotive industry. Learn about the key performance features of acrylic PSAs and how they ensure durability, chemical resistance, and repositionability for long-lasting vehicle protection.
As a film manufacturer, the automotive industry increasingly prefers colored paint protective film (PPF) over traditional, clear film. This is because compared to clear film, colored PPF:
- Enhances sustainability: The processing steps to paint vehicles can require high energy levels to complete due to surface preparation, application, curing and often repeating the process for multiple paint layers; utilizing a colored film instead of clear film can help reduce those energy levels as well as the processing steps and required layers.
- Improves aesthetics: Clear PPF provides excellent protection against scratches, chipping and other damage, but its glossy appearance can alter the desired look of the vehicle's paint. Colored PPF can be glossy, matte or satin, so it enables car owners to maintain the vehicle’s original paint color while providing protection. By keeping its appearance and finish over time, colored PPF also helps increase the vehicle’s resale value.
- Increases customization: Just like clear PPF, colored PPF can be manufactured with different surface textures and levels of glossiness to achieve the desired aesthetic effect. This allows end users the option to customize their vehicle with various colors and finishes. It also enables them to purchase a vehicle that maintains desired interests or needs.
However, it can be challenging to manufacture colored PPF that meets overarching sustainability, aesthetic and customization requirements if it doesn’t first use the right pressure sensitive adhesive (PSA) to meet application performance demands. Learn about what performance features your colored PPF adhesive should possess as well as the recommended technologies and how each one meets overarching requirements.
Performance Features Colored PPF PSAs Should Possess
Durability Against External Elements
When using colored PPF, it’s important to utilize an adhesive that can help the film maintain the desired color after trenching and throughout a potential lifespan of 10 to 12 years, which is comparable to many automotive vehicles. This means the adhesive should provide long-term protection with:
- Chemical resistance: The adhesive formulation should be comprised of materials that do not break down easily when exposed to gas, oil, cleaning products or more. This can be achieved by choosing an adhesive that forms a barrier to protect the colored PPF from staining, discoloration or damage caused by chemical exposure.
- Heat and UV resistance: Whether the colored film is enduring extreme or changing temperatures or exposed to UV light for an extensive amount of time, such as when the vehicle is parked outside, it needs to have cohesive strength to provide cold flow prevention; this protects against film distortion that could otherwise lead to scratches on the vehicle over time.
Internal Chemical Stability
An adhesive that has good internal strength can further enhance the overall protection of the colored PPF, helping to expand the lifespan for as long as possible. Therefore, it’s important to choose an adhesive that offers:
- Plasticizer resistance: An adhesive formulation with plasticizer resistance helps it maintain strength and integrity when in contact with flexible materials like polyurethane that are utilized to create colored PPF. If the adhesive lacks plasticizer resistance, it may weaken when used with polyurethane material, leading to loss of bond strength or adhesive failure.
- Migration resistance: Adhesives with high migration resistance are formulated to minimize or prevent their components from transferring into other materials or substrates over time, helping to ensure long-term performance and appearance. If components such as plasticizers or other additives migrate out of the adhesive layer, it can lead to discoloration, staining or other undesired effects on the colored PPF.
Repositionability
It’s important for colored PPF to be repositionable during installation to ensure accurate, clean finishes yet still maintain a bond throughout the vehicle’s life. This means the adhesive should offer sufficient:
- Peel strength: The adhesive should offer low peel properties initially to provide repositioning during installation. However, as the adhesive sets and cures over time, it needs to gradually develop higher peel strength to ensure a durable and long-lasting bond with the colored PPF.
- Initial tack levels: Similar to peel strength, the adhesive should have a balance between initial tack and final adhesion. The initial tack will provide the stickiness to hold the colored PPF in place during installation while still allowing for repositioning if adjustments are needed before it fully sets.
Why Bostik’s Acrylic Pressure Sensitive Adhesives (PSAs) are the Right Choice for Colored PPF
Pressure sensitive adhesives (PSAs) based on acrylic technology allow the colored PPF to provide high strength with a clean appearance. The recommended acrylic types include:
-
Specialty solution acrylic
-
UV acrylic
-
Waterborne acrylic
How These PSA Technologies Meet Colored PPF Performance Needs
All of these technologies help you achieve important performance features for colored PPF by offering:
- Durable performance: These PSA technologies form strong bonds to resist external elements including chemical exposure, changing or extreme temperatures and UV light over time. This helps ensure the colored PPF will outlast various elements it endures throughout its lifespan to maintain its appearance and quality.
- High cohesive strength: These PSAs have high cohesive strength that holds the adhesive’s molecules together, helping to resist any softening or weakening from plasticizers and chemical migration into other materials of the colored PPF. This enables the colored PPF to maintain strong bonding and structural integrity over time.
- Repositioning capabilities: These PSAs balance peel and tack capabilities to enable repositioning of the colored PPF before it develops a strong, long-term bond. This enables easy workability for the installers while ensuring the colored PPF will protect from scratches and chipping throughout the lifespan. Further, PSAs provide the ability to fully remove the colored PPF if necessary later in the vehicle’s lifespan.
How These PSA Technologies Help Improve Colored PPF Sustainability:
Each acrylic PSA technology also offers sustainable benefits; however, the type of acrylic will determine the level of sustainability you’re able to achieve. For example:
- Decreased energy usage: Solvent-based, UV acrylic and waterborne acrylic PSAs all contribute to helping you reduce the overall energy levels in your facility. While specialty solution acrylic PSAs do still contain solvents, they have high solids content to decrease the time required to dry, which contributes to reduced energy usage. However, because both UV and waterborne acrylic are solventless solutions, they are often seen as more sustainable. They also have fewer processing steps and don’t need to run drying ovens and oxidizers. Of these three options, UV reduces energy usage the most, though, because it’s a 100% solids solution.
- Less material replacement: If your application requires extended durability, then either specialty solution acrylic or UV acrylic PSAs will work well due to their high bond strength. Additionally, both options can help you extend the overall product life of the vehicle by maintaining appearance, which can help a consumer be less inclined to repaint an existing and therefore reduce material use. This can also help enable the colored PPF to contribute to increased resale value later.
- Improved safety: As mentioned above, while specialty solution acrylic PSAs do contain solvents, they are formulated with high solids content. This helps to improve worker safety and reduce exposure to solvents. However, waterborne and UV provide further advantages to worker safety. By containing zero solvents, they can help improve worker protection by reducing the use of hazardous materials in your facility. These solutions also help decrease fire risks, since you do not have to take special precautions for storing and shipping material with solvents.
How These PSA Technologies Help Enhance Colored PPF Aesthetics:
Solvent-based, UV acrylic and waterborne acrylic PSAs all help maintain overall colored PPF aesthetics for the long-term. For example, they are designed to prevent cold flow interaction by enhancing stability and reducing creep, which protects the film from aging or turning yellow over time. They also all offer high levels of clarity and transparency. This allows for colored PPF to maintain its vibrancy throughout the vehicle’s lifespan.
How These PSA Technologies Help Increase Colored PPF Customization:
Specialty solution, UV and waterborne acrylic PSAs offer a range of solutions to help ensure your colored PPF has the desired surface textures and glossiness needed for the end-use application. It’s important to work with a reliable adhesive supplier that can assist you directly with customization options, as this can help reduce complexities in providing your end users various color or finish options they may want. Further, working with a reliable supplier will ensure the customized formulation provides key performance features that will work with your equipment capabilities and provide long-term application usage.
Why Work with Bostik
Bostik offers the most complete and integrated portfolio of PSA offerings on the market, helping you to develop high-performing colored PPF that addresses the specific needs of each vehicle where it’s applied. Our range of PSA technologies allows you to choose an option that is compatible with equipment you already own, saving costs and downtime while also achieving high performance and sustainability improvements. Along with our high-performing PSA solutions, you’ll also receive:
- Technical support: We help you determine the right PSA technology based on your specific performance and coating needs. Our assistance with trial testing helps you continue regular production schedules until you have made a decision on the right solution.
- Troubleshooting: We help you manage any issues that arise on your coating lines, helping identify ways to make improvements for efficient production.
Are you interested in learning how PSAs can help you design high-performing colored PPF? Contact a Bostik expert to learn how we can help you determine the right PSA technology for your application needs.
Other Relevant Content:
What You Need to Know to Make the Switch to UV Acrylic PSAs
Understanding UV HMPSAs and How They Benefit You
Improve Your Environmental Footprint with Specialty Film PSAs
What to Know Before Selecting a Specialty Film Pressure Sensitive Adhesive
©2024 Bostik, Inc. All Rights Reserved
All information contained herein is believed to be accurate as of the date of publication, is provided “as-is” and is subject to change without notice. To review our full U.S. Legal Disclaimer, visit: https://bostik.com/us/en_US/privacy-policy/legal-disclaimer